Кракен kr2web in маркетплейс ссылка
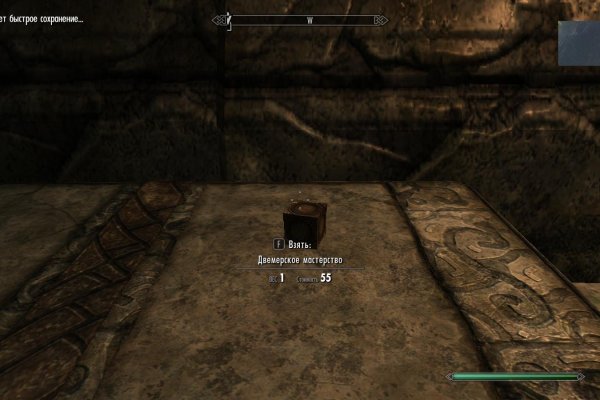
На сайте предусмотрена двухфакторная аутентификация, которую любой может включить в личном кабинете. Он позволяет связать свои публичные ключи PGP с пользовательским профилем. Откройте сайт m на компьютере. В этом случае, в мире уже где-то ожидает вас выбранный клад. Работа с Диском для компьютеров Установите приложение Google Диск для компьютеров. Федерального закона от N 87-ФЗ) (см. Вы можете скопировать свои фотографии и видео на свое устройство. Если фото на Гидру все равно не загружается. Прекратим о грустном. Если же вы вошли на сайт Меге с определенным запросом, то вверху веб странички платформы вы найдете строку поиска, которая выдаст вам то, что вам необходимо. Они пытаются вычислить операторов и администраторов ресурса, чтобы предъявить им обвинения в распространении наркотиков и отмывании денег. С правилами 22:38 Приобретение готовых аккаунтов Hydra Время на прочтение 3 минут(ы) Hydra является не только местом крупнейшей торговли в даркнете, но и сайтом, с помощью которого можно обмануть и хорошо заработать. Остальные используют его для безопасного серфинга по Интернету. Как открыть папку скачанных файлов Как использовать облачное kragl хранилище mega. Поясним, что даркнет это интернет-сеть, для доступа к которой используют специальное программное обеспечение таким образом, чтобы скрыть личность людей и связанную с ними активность в Интернете. Гидре, нужно удостовериться, что с момента покупки не прошло больше 24 часов. Работает с пк и телефона способ TOR browser / ТОР браузер / обзор. Установите флажок "Преобразовывать загруженные файлы в формат Google". Одним из самых главных способов обхода страшной блокировки на сайте Меге это простое зеркало. Если размер и так небольшой, а проблема не решилась, стоит попробовать пересохранить фото, сделав его скриншот. Прихожу в подъезд клад в мусорке. После этого подтвердите. Однако лишь немногие трейдеры на Hydra согласятся кликать на сторонние ссылки.
Кракен kr2web in маркетплейс ссылка - Kra34.cc
Onion - Privacy Tools,.onion-зеркало сайта. Финансы. Ч Архив имиджборд. Onion - grams, поисковик по даркнету. Языке, покрывает множество стран и представлен широкий спектр товаров (в основном вещества). 2qrdpvonwwqnic7j.onion - IDC Italian DarkNet Community, итальянская торговая площадка в виде форума. Bpo4ybbs2apk4sk4.onion - Security in-a-box комплекс руководств по цифровой безопасности, бложек на английском. Onion/ - Dream Market европейская площадка по продаже, медикаментов, документов. Различные тематики, в основном про дипвеб. Onion - VFEmail почтовый сервис, зеркало t secmailw453j7piv. Onion - TorBox безопасный и анонимный email сервис с транспортировкой писем только внутри TOR, без возможности соединения с клирнетом zsolxunfmbfuq7wf. Onion - PIC2TOR, хостинг картинок. Ссылку нашёл на клочке бумаги, лежавшем на скамейке. Onion - Daniel Winzen хороший e-mail сервис в зоне.onion, плюс xmpp-сервер, плюс каталог онион-сайтиков. Связь доступна только внутри сервера RuTor. Onion - Verified,.onion зеркало кардинг форума, стоимость регистрации. Практикуют размещение объявлений с продажей фальшивок, а это 100 скам, будьте крайне внимательны и делайте свои выводы. Onion - простенький Jabber сервер в торе. Mixermikevpntu2o.onion - MixerMoney bitcoin миксер.0, получите чистые монеты с бирж Китая, ЕС, США. Onion - XmppSpam автоматизированная система по спаму в jabber. Напоминаем, что все сайты сети. Раньше была Финской, теперь международная. Onion - Продажа сайтов и обменников в TOR Изготовление и продажа сайтов и обменников в сети TOR. Bm6hsivrmdnxmw2f.onion - BeamStat Статистика Bitmessage, список, кратковременный архив чанов (анонимных немодерируемых форумов) Bitmessage, отправка сообщений в чаны Bitmessage. Проект создан при поддержке форума RuTor. Литература. Onion - Mail2Tor, e-mail сервис. Фарту масти АУЕ! Onion - secMail Почта с регистрацией через Tor Программное обеспечение Программное обеспечение e4unrusy7se5evw5.onion - eXeLaB, портал по исследованию программ. Рейтинг продавца а-ля Ebay. Onion - Alphabay Market зарубежная площадка по продаже, оружия, фальшивых денег и документов, акков от порносайтов. Перемешает ваши биточки, что мать родная не узнает. Без JavaScript. Независимый архив magnet-ссылок casesvrcgem4gnb5.onion - Cases. Ml -,.onion зеркало xmpp-сервиса, требует OTR. Legal обзор судебной практики, решения судов, в том числе по России, Украине, США. Мы выступаем за свободу слова. Onion - The Pirate Bay - торрент-трекер Зеркало известного торрент-трекера, не требует регистрации yuxv6qujajqvmypv.
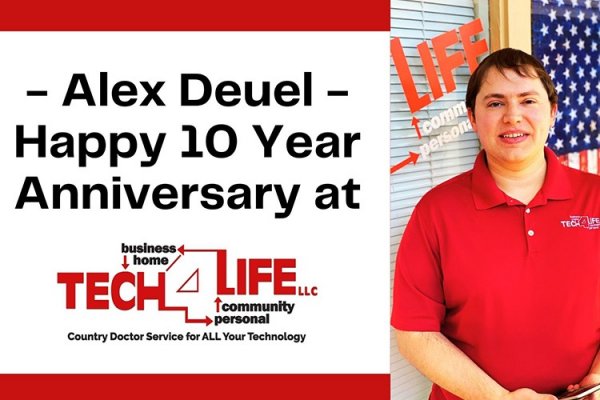