Войти в кракен вход магазин
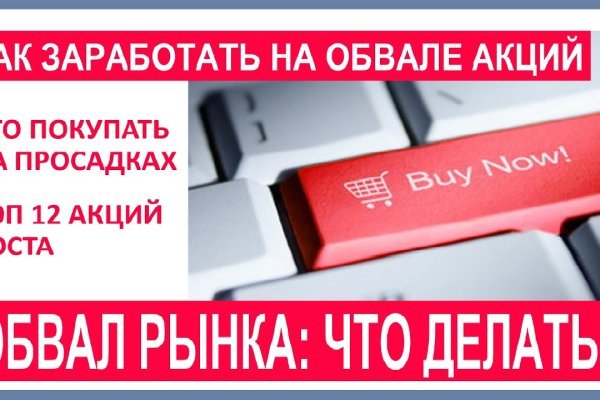
Похожие. Ссылкам. Размер:. Интересующиеся могут сами ознакомиться с полным ассортиментом. На нашем представлена различная информация о, собранная из открытых источников, которая может быть полезна при анализе и исследовании. Что такое DarkNet и как он работает? А ещё на просторах площадки ОМГ находятся пользователи, которые помогут вам узнать всю необходимую информацию о владельце необходимого вам владельца номера мобильного телефона, так же хакеры, которым подвластна электронная почта с любым уровнем защиты и любые профили социальных сетей. Сайты также расположены на онион доменах работающих в Тор браузере. 2005 открытие торгового центра мега в Казани. Как подростки в России употребляют доступный и дешевый эйфоретик. Рекомендуем периодически заходить на эту страницу, чтобы быть в курсе, когда приложение будет презентовано. Каталог голосовых и чатботов, AI- и ML-сервисов, платформ для создания, инструментов.возврата средств kraat /фальш/ дейтинг и все что запрещено Законами Украины. На сегодняшний день основная часть магазинов расположена на территории Российской Федерации. Godnotaba дает объективную оценку. Что такое даркнет-магазин и чем занимается, новости на года? Ведущий торгово-развлекательный центр России, мега Белая Дача. Топовые семена конопли здесь! Что такое. И от 7 дней. Всегда kracc только оригинальная ссылка на сайт гидра. Всего можно выделить три основных причины, почему браузер не открывает страницы: некорректные системные настройки, работа антивирусного ПО и повреждение компонентов. Используя это приложение, вы сможете загружать ваши данные на облако. Russian Marketplace один из крупнейших русскоязычных теневых форумов и торговая площадка.
Войти в кракен вход магазин - Kra13gl
ы» больше всего выиграли RuTor, WayAway, Legalizer, OMG!, Solaris ссылка и Nemesis. И все это закончилось тем, что я уже четвертый год на ЗПТ. Немного видоизменится окно чата, а кнопка "фотоаппарат" станет кликабельной. Редко пользователи не могут загрузить фото с мобильного устройства даже после действий, описанных выше, но с компьютера успех должен быть 100. Подробнее о том, как экспортировать и скачать данные Google Фото. Ссылкам. Ру» ) было все налажено. Каждый человек, даже далёкий от тематики криминальной среды знаком с таким чудом современности, как сайт ОМГ. Как повысить скорость загрузки в uTorrent на Android. Onion рабочее зеркало Как убедиться, что зеркало OMG! З охочими купити наркотик зловмисники спілкуються зазвичай у Telegram. Чтобы использовать Google Диск на работе или в учебном заведении более эффективно, оформите бесплатную подписку на Google Workspace. Для покупки этой основной валюты, прямо на сайте встроенные штатные обменные пункты, где вы можете обменять свои рубли на bit coin. Вот, она, конечно, получше, чем до этого был Эфкур. Если вы не хотите случайно стать жертвой злоумышленников - заходите на OMG! Я стала в программу очень легко, без проблем. Потом в «это не мое» никто не поверит. Выберите файлы или папку. Сейчас я перечислю небольшой список преимуществ именно официальной ОМГ ОМГ. На фоне успеха этих групп новый поток альтернативных исполнителей (помимо представителей постпанк-ривайвла, это были: Modest Mouse, The Killers и Yeah Yeah Yeahs ) обрёл мейнстримовую популярность в начале и середине нулевых годов. Уже в ближайшее время технические специалисты будут знать причину аварии. На сотни метров в окрестностях от этой аптеки на тротуарах, в скверах и во дворах жилых домов абсолютно не присматриваясь можно наблюдать множество опустошенных пластинок от таблеток препарата "Кодепсин". Система рейтингов покупателей и продавцов (все рейтинги открыты для пользователей). Самой надёжной связкой является использование VPN и Тор. Spin Media, ноябрь 2005. . Такое мнение можно отнести к стереотипам. Автоматическая система учёта и реализации энергоресурсов. Всем надо брать с вас пример! The band has always been well received and in spite of ch (англ.). Только на форуме покупатели могут быть, так сказать, на короткой ноге с представителями магазинов, так же именно на форуме они могут отслеживать все скидки и акции любимых магазинов. Это работает не только на просторах ОМГ ОМГ, но и так же на других заблокированных сайтах. Если потребуется скрыть личность при переводе монет, можно воспользоваться встроенным миксером. Нету других схем. Он не умер, но в голове так и застыло тихое и зловещее: Это кондитер. Onion - The Majestic Garden зарубежная торговая площадка в виде форума, открытая регистрация, много всяких плюшек в виде multisig, 2FA, существует уже пару лет. Grierson, Tim Top 10 Rock Albums of the '00s (англ.). Большинство из клиентов наркозависимые, а наиболее "ходовой" товар препараты, содержащие кодеин (опиумный наркотик). Необходимость фотографий.
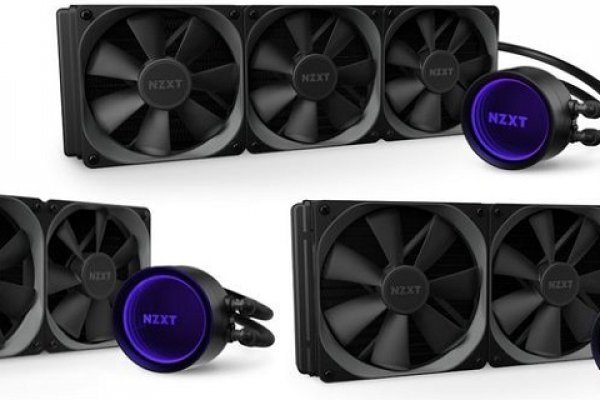
Http k4bmdpobhqdguh2y.onion/ - блог о новых скрытых сервисах сети (ENG). Прокси-сервер отказывается принимать соединения в Tor Browser Ошибка «Прокси-сервер отказывается принимать соединения» в Tor Browser может возникнуть у любого пользователя в ходе интернет-серфинга. Возможные причины неполадки и методы устранения К сожалению, причину данной неполадки без специальных компьютерных знаний определить довольно затруднительно. Просто скопируйте ее из нашей статьи, вставьте в адресную строку анонимного браузера и нажмите. Страницы загружается намного медленнее, чем обычно. И постоянно предпринимают всевозможные попытки изменить ситуацию. Шаг 2: Поиск скрытых интернет-сайтов Теперь у вас есть все необходимое для доступа в Дарк Веб. Дополнительные сервера: ftwircdwyhghzw4i.onion, renko743grixe7ob. Рано или поздно пользователь все равно столкнется с какими-либо ошибками. Onion, где ( xxx основная часть URL-адреса, а onion псевдо-домен верхнего уровня, у обычных ресурсов заместо него идет ru, com, org, net и так далее). В выпадающем списке выберите «Временно разрешить выполнение скриптов на этой странице». Впишите адрес нужного сайта. Это всё к тому, чтобы ты не расслаблялся слишком уж откровенно и постоянно помнил, что Tor - не панацея, и любая анонимность относительна. Tor - это аббревиатура The Onion Router (не знающим буржуйского, но любопытным - смотреть перевод в онлайн-переводчиках ). Выделить мышкой, копировать, вставить в адресную строку. Напомню лишь про вирусы, от которых Tor тебя не защитит - предохраняйся сам. Но не более. Они никак не могут смириться с тем, что толпы юзеров свободно и бесконтрольно бродят по сети без их «всевидящего ока». Необходимо заметить, что независимо от имеющегося расширения.exe, этот пакет не является программой, которую требуется устанавливать. Silk Road (http silkroadvb5piz3r.onion) - ещё одна крупная анонимная торговая площадка (ENG). Протекает она в несколько простых шагов: Настоятельно рекомендуем предварительно сохранить все важные данные, ведь они в результате выполнения данной инструкции будут очищены.