Как восстановить аккаунт кракен
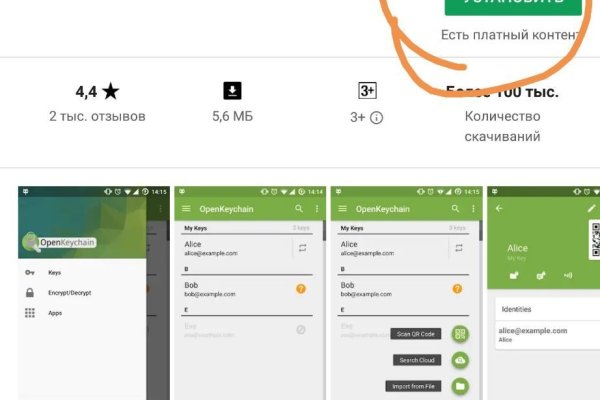
Подборка Marketplace-площадок by LegalRC Площадки постоянно атакуют друг друга, возможны долгие подключения и лаги. Подборка Обменников BetaChange (Telegram) Перейти. Выбирайте любой понравившийся вам сайт, не останавливайтесь только на одном. Сеть для начинающих. Зеркало сайта. Работает как на Windows, так и на Mac. Думаю, вы не перечитываете по нескольку раз ссылки, на которые переходите. Наша задача даркнет вас предупредить, а вы уже всегда думайте своей головой, а Мега будет думать тремя! Приятного аппетита от Ани. Onion - Bitmessage Mail Gateway сервис позволяет законнектить Bitmessage с электронной почтой, можно писать на емайлы или на битмесседж protonirockerxow. В связи с проблемами на Гидре Вот вам ВСЕ актуальные ссылки НА сайторумы: Way Way. По типу (навигация. Выбирая на магазине Мега Даркнет анонимные способы оплаты, типа ссылка Биткоин, вы дополнительно страхуете себя. С другой стороны, у него есть версии для iOS, Android, PC и Mac: последние две очень простые в кракен использовании. Гидра правильная ссылка. На iOS он сначала предлагает пройти регистрацию, подтвердить электронную почту, установить профиль с настройками VPN, включить его профиль в опциях iOS и только после этого начать работу. Только английский язык. По. Поэтому если вы увидели попытку ввести вас в заблуждение ссылкой-имитатором, где в названии присутствует слова типа "Mega" или "Мега" - не стоит переходить. Telefon oder E-Mail Passwort Забирай! Сам же сайт включает в себя множество функций которые помогают купить или продать вес буквально автоматизированно, и без лишних третьих лиц. Кардинг / Хаккинг. Этот сайт содержит 2 исходящих ссылок. Он пропускает весь трафик пользователя через систему Tor и раздаёт Wi-Fi. Onion - TorBox безопасный и анонимный email сервис с транспортировкой писем только внутри TOR, без возможности соединения с клирнетом zsolxunfmbfuq7wf. Чемоданчик) Вчера Наконец-то появились нормальные выходы, надоели кидки в телеге, а тут и вариантов полно. Всегда работающие методы оплаты: BTC, XMR, usdt. Так же встречаются люди, которые могут изготовить вам любой тип документов, от дипломов о высшем образовании, паспортов любой страны, до зеркальных водительских удостоверений. Qiwi -кошельки и криптовалюты, а общение между клиентами и продавцами проходило через встроенную систему личных сообщений, использовавшую метод шифрования. Этот сайт упоминается в деловой социальной сети LinkedIn 0 раз. Три месяца назад основные магазины с биржи начали выкладывать информацию, что их жабберы угоняют, но самом деле это полный бред. Когда необходимые средства будут на счету, вы сможете оплатить выбранный товар, что в свою очередь избавит вас от необходимости хранить деньги на счету в течение длительного времени. Даркмаркет направлен на работу в Российском рынке и рынках стран СНГ. Данное количество может быть как гарантия от магазина. Во-вторых, плагин часто превращает вёрстку заблокированных страниц в месиво и сам по себе выглядит неопрятно. Если же данная ссылка будет заблокированная, то вы всегда можете использовать приватные мосты от The Tor Project, который с абсолютной точностью обойдет блокировку в любой стране. Клиент, использующий форум не упускает прекрасную возможность быть в самом центре событий теневого рынка Мега. Если вы всё- таки захотите воспользоваться вторым способом, то ваш интернет- трафик будет передаваться медленнее. Onion - BitMixer биткоин-миксер. Только сегодня узнала что их закрылся. Оригинальный сайт: ore (через TOR browser) / (через Тор) / (онион браузер).Сборник настоящих, рабочих ссылок на сайт мега в Даркнете, чтобы вы через правильное, рабочее зеркало попали на официальный сайт Меги. Ссылку нашёл на клочке бумаги, лежавшем на скамейке. При входе на правильный сайт вы увидите экран загрузки. Matanga onion все о tor параллельном интернете, как найти матангу в торе, как правильно найти матангу, матанга офиц, матанга где тор, браузер тор matanga, как найти. Ну, любой заказ понятно, что обозначает.
Как восстановить аккаунт кракен - Как войти в кракен
Основные особенностиomg САЙТ РАБОЧАЯ ССЫЛКА ONIONПростой интерфейс не дает запутаться и сделает пребывание на сайте удобным и простымСкоростьНаша платформа написана с нуля и заточена под максимальную скоростьБезопасностьСложная система шлюзов, мостов, onion роутинга позволяет достичь наивысшую безопасность и анонимностьВойти на сайта ОМГ прямо сейчасСсылка представленная ниже безопасна и анонимнаЗайти на omgКак пользоваться omg1Создайте аккаунтДля того необходимо открыть страницу регистрации, заполнить необходимые поля и нажать кнопку "зарегистрироваться"2Выберите товарВашему вниманию представлена прекрасная система навигации с переходами по категориям3Пополните кошелекBitcoin кошелек можно как переводом с другого кошелька, так и через обменники4Оплатите и получите товарЗайдя в необходимый товар, нажмите кнопку оплатить, вам будут отправлены данные о местоположение покупки и тд5НаслаждайтесьМы надеемся на то, что наш сервис принесет вам максимальное удовольствиеFAQОстались вопросы?Насколько безопасно пользоваться omg?Наши инженеры - лучшие специалисты по кибербезопасности, самые современные технологии обеспечивают 100% анонимность и безопасность.Что делать если сайт заблокируют?Не секрет что с недавних пор правительство активно взялось за интернет и анонимность в частности, поэтому для наибольшего удобства мы создали несколько зеркал нашего сайта, если какое-то зеркало не работает, пробуйте другоеКак войти на omg?Для этого нужно просто перейти по ссылкеЧто делать если я не получил свой товар?Действительно из-за некоторых людей, которые занимаются поиском чужих товаров, такая ситуация возможна, после покупки вы имеете 24 часа на обжалование, в данном случае администрация omg в срочном порядке рассмотрит вашу жалобу и честно разрешит возникшую ситуацию.Описание веществМарихуана (Каннабис)В зависимости от сорта (индика/сатива) вызывает различные чувства.По эффекту воздействия при курении индика и сатива противоположны – если индика вызывает заторможенность, снижение активности, сильное расслабление, то сатива наоборот, стимулирует всплеск энергии, поднимает настроение и провоцирует на активные действия.Оба этих сорта использовались в медицинских и лечебных целях. Сорта конопли с высоким содержанием индики преимущественно служили избавлением от бессонницы и болей, поэтому часто применялись перед сном. Семена конопли индики имеют сниженный процент содержания ТГК.Обратное действие сативы – стимулирующее и активизирующее внутренний потенциал – нашло применение при лечении стресса, депрессий, повышенной тревожности.Видео ПерейтиЭйфоретики (МДМА, Мефедрон)МДМА (Экстази)Эффекты MDMA проявляются через 30-60 минут после употребления, а пик наблюдается через 75-120 минут, плато длится 3,5 часа.7) Кратковременные психоактивные эффекты MDMA включают:Эйфория – ощущение чувства удовлетворения и счастьяУвеличение социальной активности и коммуникабельностиЭнтактогенные эффекты – увеличение эмпатии или чувства близости с другими людьмиОщущение внутреннего умиротворенияНебольшие галлюцинации (усиление ощущения цветов и звуков и видения с закрытыми глазами)Усиление ощущений, восприятия или сексуальностиВидео ПерейтиМефедронМефедрон вызывает эйфорию, стимулирующий эффект, способствует более глубокому пониманию музыки, поднимает настроение, снижает враждебность, вызывает улучшение умственной деятельности и оказывает мягкую сексуальную стимуляцию; эти эффекты подобны эффектам кокаина, амфетамина и МДМА, и длятся разное количество времени, в зависимости от способа введения препарата. При пероральном приеме, пользователи сообщали о возникновении эффекта в течение 15-45 минут; при вдыхании последствия ощущались в течение нескольких минут и достигали пика в течение получаса. При приеме внутрь или через нос эффект длится от двух до трех часовПерейтиСтимуляторы (Кокаин, Амфетимин)КокаинКокаин ведет к поднятию настроения и общительности, секреты не становятся тайной. На короткий промежуток времени улучшается память и умственная работоспособность. Ты начинаещь чувствовать себя богом.Видео Перейти omg onion ссылка на магазин омгomgОМГ входomgomgomgomgОМГ ссылка анионomg onionАмфетаминАмфетамин, может улучшить производительность при выполнении сложных и скучных заданий и используются некоторыми студентами в качестве «допинга» при подготовке к экзаменам.Видео ПерейтиПсиходелики (ЛСД, грибы)ЛСДВозникает ощущение того, что вся окружающая обстановка как будто «плывет и дышит», постоянно видоизменяясь. За закрытыми глазами появляются необыкновенные меняющиеся красочные узоры. Ощущается общий прилив энергии, подъем настроения и повышение ассоциативного мышления.Видео ПерейтиГрибыГрибы повышают самосознание и чувство контакта с «Трансцендентным Другим» – отражая более глубокое понимание нашей связи с природой. Психоделические препараты могут вызывать состояния сознания, которые имеют личный смысл и духовное значение у религиозных или обладающих духовными наклонностями людей; эти состояния называются мистическими переживаниями.Видео ПерейтиВнимание!Участились случаи мошенничества, рекомендуем добавить сайт в закладки чтобы не потерять его.Добавить в закладкиmoy-vkus.comCopyright © 2015 — 2020. Все права защищены.
Вся информация представлена в ознакомительных целях и пропагандой не является.omg onion Загрузка, ждите...
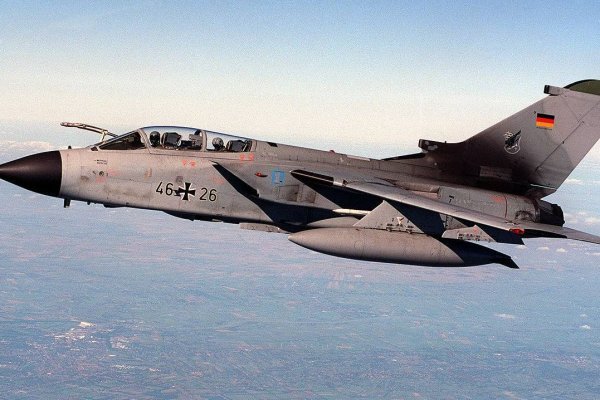
Я не несу. Всё что нужно: деньги, любые документы или услуги по взлому аккаунтов вы можете приобрести, не выходя из вашего дома. Гарантия возврата! Мега Нижний Новгород Нижегородская область, Кстовский район,. Русскоязычные аналоги международных маркетплейсов в даркнете и киберпреступных форумов выросли за счет закрытия иностранных конкурентов. Особых знаний для входа на сайт OMG! Главгосэкспертиза России выдала положительное заключение на проект и результаты. Наркотики станут дороже, криминала на улицах больше. Войти. Каждый день администрация ОМГ ОМГ работает над развитием их детища. Созданная на платформе система рейтингов и возможность оставлять отзывы о магазинах минимизирует риски для клиента быть обманутым. Спасибо администрации Омг Onion и удачи в продвижении! Маркетплейс СберМегаМаркет каталог товаров интернет-магазинов. Вся информация о контрагенте (Москва, ИНН ) для соблюдения должной. Также в числе ключевых арендаторов магазины «Ашан «ОБИ» и «Леруа Мерлен». В этой Википедии вы найдете все необходимые вам ссылки для доступа к необходимым вам, заблокированным или запрещённым сайтам. Всё, что надо знать новичку. Карта патрулей Узнавай от других пользователей о безопасности района, в который собираешься отправится и сам оставляй заметки. Здесь представлены официальные и зеркала, после блокировки оригинального. Первый способ заключается. Лучшие модели Эксклюзивный контент Переходи и убедись сам. 1 2011 открыта мега в Уфе (25 августа) и Самаре (22 декабря).