Браузер кракен
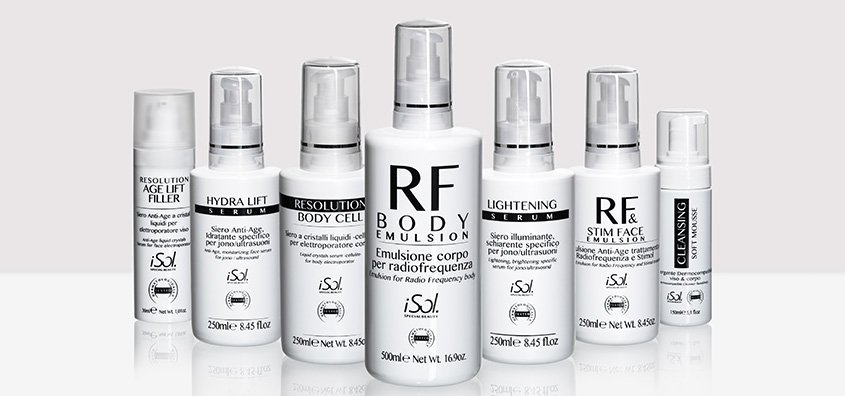
В рабочая социальных аккаунтах компании также нет никакой информации. По данным следствия, «Гидра» была нелегальной торговой площадкой с самым высоким оборотом в мире. 1 2 В Германии закрыли сервера kraken даркнетмаркета Hydra и конфисковали биткойны на 23 млн евро. Теперь ваша рекламная запись будет показываться только тем, кто отвечает этим характеристикам другие ее просто не увидят. Мобильный телефон - это важный и нужный аксессуар для любого человека. Ежесекундно на сайте омг совершается больше тысячи различных сделок. Как пользоваться TOR на iPhone и iPad через Onion Browser. К ним могут присоединиться и десятки тысяч бывших кладменов со всей страны. Продажи на Гидре onion В отличие от классических магазинов, приобретение заказов на «Гидре» осуществляется на базе криптовалюты. Еще есть варианты попасть на основной сайт через зеркало, но от этого процедура входа на mega не изменится. Он считается крупнейшим российским даркнет-рынком, который начинал с торговли наркотиками. Тор гидра Что сейчас происходит с Tor? Причиной этому является устранение возможности утечки данных или IP, так что отключение некоторых функций необходимо. Не помешают элементы экспрессии у посетителей будут ассоциации с движением, современностью, скоростью. Ссылка на гидру сайт в tor и веб. Оплата услуг привычными нами валютами в Даркнете осуществляется очень редко. А значит, ваша ЦА очень широкая. Помимо телефонов, кассу можно сделать на отдельных деталях телефонов (стекло, батарея, защитная пленка) и сопутствующих товарах: блютуз-гарнитура, наушники и так далее. Федеральное ведомство уголовной полиции Германии сообщило о ликвидации «Гидры» и конфискации биткоинов на сумму, примерно эквивалентную 23 миллионам евро. Вы забанены Забанили аккаунт на гидре Что делать Как восстановить. Если с забаненного аккаунта написать не получится, то Вы можете написать с другого аккаунта. Не вижу ничего подозрительного в этом. Заметили, что в салонах сотовой связи работают в основном мужчины? Что делать в такой ситуации? В нем kraken взломщики утверждают, что Solaris находится под полным контролем Kraken. Благодаря этому сайт гарантирует высокую скорость и минимальное время отклика. Есть как система тикетов в аккаунте, так и E-mail support. Отзывы пользователей Отличный сервис.
Браузер кракен - Kraken shop
Я несколько лет сидел на метадоне и пришел момент, когда я устал. Применяются препараты, улучшающие обмен веществ и устраняющие поведенческие расстройства. Осмотр психиатра-нарколога Индивидуальный план лечения Размещение 4-6 человек в палате 4-разовое питание Индивидуальное сопровождение Личная терапия с психологом Групповые занятия и семинартика. В волосах и ногтях метадон держится дольше всего и обнаруживается спустя три месяца после последнего употребления. Его поведение становится непредсказуемым, он может впасть в депрессию, совершить суицид Как ведут себя наркоманы, употребляющие метадон Человек, употребляющий наркотики, рано или поздно начнет выделяться поведением и внешним видом. Как вывести метадон из организма Несмотря на то, что в целом избавление от метадоновой зависимости проходит по той же схеме, что и при других зависимостях, лечение включает в себя некоторые нюансы. Слабый пульс, сердечная аритмия. Потому, кстати, опиоиды стоят на первом месте по частоте смертности от передоза. В случае, если врач определил передозировку метадоном, назначается налоксон на сегодняшний день это единственный антидот в арсенале наркологов, успешно противостоящий отравлению и передозировке опиатами. Мышцы конечностей судорожно сокращаются. Взаимодействие с чувствительными клетками приводит к возникновению побочных эффектов, например, угнетение дыхания или снижение перистальтики ЖКТ. Самостоятельное лечение невозможно, потому что метадон один из самых серьезных и тяжелых наркотиков современности. Как ведут себя наркоманы, употребляющие метадон. Диагностика Метадон имеет необычное свойство он накапливается в организме. Метадон относится к группе опиатов и обладает определенными обезболивающими свойствами, однако его побочный эффект оказался таким непредсказуемым, что даже Рейх в скором времени отказался от его использования. Через. Сердечнососудистая система начинает работать прерывисто, вызывая панические атаки. Тестовую полоску помещают в емкость с мочой, а затем смотрят результат. Эйфория длится в течение суток и больше. Периодически сводит судорога. После окончания действия наркотика человек чувствует себя обессиленным. Замедляются рефлекторные реакции, сердечный ритм, резко ухудшается дыхание и снижается артериальное давление. Метадон и героин Как говорилось выше, метадон используется для лечения зависимости от героина. Для предотвращения возможного заражения инфекционными заболеваниями дыхание рот в рот делают через марлю или платок. Это мотивационная беседа, после которой подавляющее большинство пациентов соглашаются пройти терапию в стационаре. Наркотик представляет собой серо-белый или белоснежный порошок с гранулами разного размера. Смерть от метадона Так как данный наркотик вызывает тормозящее действие на дыхательные центры в головном мозге, то может спровоцировать внезапную остановку дыхания, что и является главной причиной смерти от метадона. Можно ли бросить метадон самостоятельно?
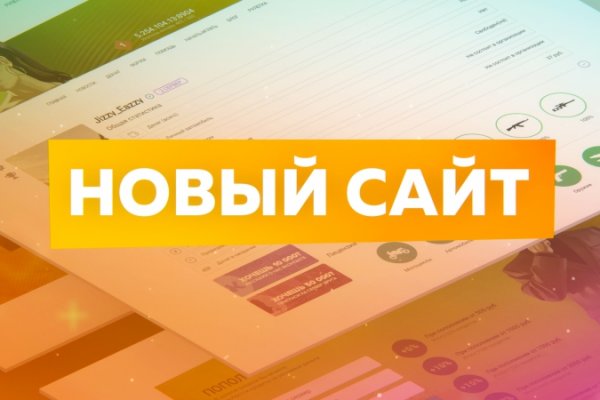
Ссылка на создание тикета: /ticket Забанили на, как восстановить Как разблокировать hydra onion. Вся представленная информация несёт лишь ознакомительный характер и не призывает Вас к действиям нарушающим закон! Старейший магазин в рунете. Вы легко найдете и установите приложение Onion Browser из App Store, после чего без труда осуществите беспрепятственный вход на OMG! Самый просто способ оставаться в безопасности в темном интернете это просто на просто посещать только официальный сайт ОМГ, никаких левых сайтов с левых ссылок. Это защитит вашу учетную запись от взлома. Травматическое оружие. В наших аптеках в Москве капсулы 300 мг. Ссылка на Гидру hydraruzxpnew4af. Перейти на ОФициальный БОТ OMG! Всё как и раньше, но лучше. Onion рабочее зеркало Как убедиться, что зеркало OMG! Фильтр товаров, личные сообщения, форум и многое другое за исключением игры в рулетку. Бот - текст в речь. Доступ через tor - http matangareonmy6bg. If you have Telegram, you can contact Каталог.onion сайтов right away. Веб-студия Мегагрупп занимается разработкой для бизнеса в Москве, Санкт-Петербурге и по всей России Стоимость от 7500. Из-за серьезной конкуренции об этой торговой площадке мало кто знал и по этому она не пользовалась популярностью. Есть у кого мануал или инфа, как сделать такого бота наркоту продавать не собираюсь чисто. Оформить заказ: /tg Задать. Всегда свежая на! По какому находится ТЦ? Данное количество может быть как гарантия от магазина. Отдельного внимания стоит выбор: Любой, моментальный, предварительный заказ или только надёжный. Пошив гидрокостюмов по индивидуальным меркам. Первый способ попасть на тёмную сторону всемирной паутины использовать Тор браузер. Ссылки на аналогичные сайты, как Гидра, где продают товары. ЖК (ул. Альтернативные даркнет площадки типа Гидры. Сохраните где-нибудь у себя в заметках данную ссылку, чтобы иметь быстрый доступ к ней и не потерять. Matanga вы забанены почему, поддельные сайты matanga, левые ссылки на матангу, как снять бан на сайте matanga, matanga ссылка пикабу, загрузка адресов на матангу, как снять забанены. Чем можно заменить. Меня тут нейросеть по фоткам нарисовала. Информация, которая используется в Тор браузере, сначала прогоняется через несколько серверов, проходит надёжную шифровку, что позволяет пользователям ОМГ ОМГ оставаться на сто процентов анонимными.