Даркнет кракен
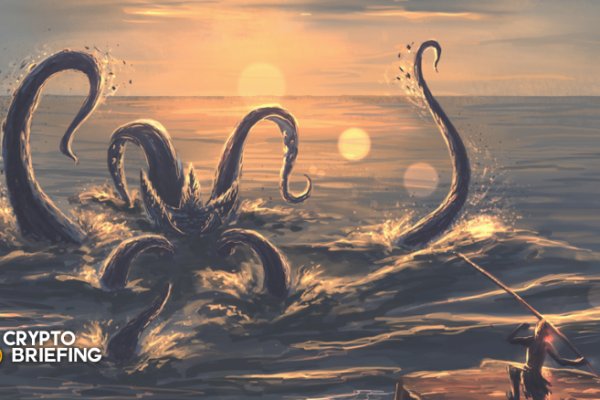
Как скачивать и открывать торрент файлы Как безопасно скачивать торренты Как скачать все файлы с Google Диска на компьютер. Убедитесь, что у кракен вас установлено расширение. Услуги смело можно заказывать - услуги проверены на прочность и качество. Примерно в тот же период была сформирована команда Yo La Tengo, которая стала одним из самых плодовитых коллективов этого жанра. "По всей видимости это были каки-то местные жители, которых достали наркотики в их дворе отметил в комментарии лидер общественной организации "Синдикат" Евгений Чепелянский. Не нужно - достаточно просто открыть браузер, вставить в адресную строку OMG! На сайте представлен широкий выбор запрещенной продукции, которую просто так не получится купить в обычном интернете. Keybase зеркало. Это сделано для того, чтобы покупателю было максимально удобно искать и приобретать нужные товары. Плагины для браузеров Самым удобным и эффективным средством в этой области оказался плагин для Mozilla и Chrome. Если RuTor все же падет, ему уже подготовили замену: в тот же день, когда Kraken объявил о союзе с Solaris, стало известно о воскрешении форума, сотрудники которого стояли у истоков самой «Гидры». Центр (рус.). В мобильном приложении. Но наметились шесть основных игроков, активно борющихся за лидерство. После ввода кода вы сразу попадаете на витрину маркета омг. Я буквально на днях купил новый «мерседес» и с удовольствием гонял по белорусским дорогам, с качеством которых могут сравниться разве что немецкие автобаны. Marc Masters «No Wave Black Dog, 2007, isbn X Марк Мастерс - Фрагменты книги "No Wave" (Часть 2) (рус.). Администрация m Все отзывы Как оставить отзыв? Как правильно загрузить фото в диспут на гидре. Именно на форуме каждый участник имеет непосредственную возможность поучаствовать в формировании самого большого темного рынка СНГ Hydra. Путешествуя поездом, не соглашайтесь на «передачи» в другой город от незнакомых людей. Когда мне становилось плохо, обратиться было не к кому, и я закрывала глаза и пила эти таблетки, и все. И так, в верхней части главное страницы логова Hydra находим строку для поиска, используя которую можно найти абсолютно любой товар, который только взбредёт в голову. Потребитель не всегда находит товар по причине того что он пожалел своих денег и приобрел товар у малоизвестного, не проверенного продавца, либо же, что не редко встречается, попросту был не внимательным при поиске своего клада. Выбирайте любое kraken зеркало, не останавливайтесь только на одном. Исполнители, которые имели культовый статус в США, как правило, удостаивались более частой ротации на британском радио и внимания в музыкальной прессе, а многие альтернативные группы успешно продвигались в чартах. Насилие было и физическое, и просто морально они У площадка меня мама была после операции, и она потеряла 20 килограмм, она не могла кракен просто подняться на 3-ий этаж этой конторы. Я начала в 18 лет, сразу с тяжелых наркотиков. Gz Следующие действия включают распаковку, компиляцию и установку приложения: tar xvpzf thc-hydra-v8.4.tar. В открывшемся окне найдите раскрывающееся меню "Принтер" и выберите. Такое заявление сделали в общественном. Когда этого делать не стоит?
Даркнет кракен - Найдется все кракен
- Tchka Free Market одна из топовых зарубежных торговых площадок, работает без пошлины. Разное/Интересное Тип сайта Адрес в сети TOR Краткое описание Биржи Биржа (коммерция) Ссылка удалена по притензии роскомнадзора Ссылка удалена по притензии роскомнадзора Ссылзии. Onion - WWH club кардинг форум на русском языке verified2ebdpvms. Onion - Onion Недорогой и секурный луковый хостинг, можно сразу купить onion домен. Английский язык. Программное обеспечение. Onion - Acropolis некая зарубежная торговая площадочка, описания собственно и нет, пробуйте, отписывайтесь. Onion - Архив Хидденчана архив сайта hiddenchan. Onion - Freedom Chan Свободный чан с возможностью создания своих досок rekt5jo5nuuadbie. Onion - RetroShare свеженькие сборки ретрошары внутри тора strngbxhwyuu37a3.onion - SecureDrop отправка файлов и записочек журналистам The New Yorker, ну мало ли yz7lpwfhhzcdyc5y.onion - Tor Project Onion спи. Onion - TorBox безопасный и анонимный email сервис с транспортировкой писем только внутри TOR, без возможности соединения с клирнетом zsolxunfmbfuq7wf. Мы выступаем за свободу слова. Onion - Checker простенький сервис проверки доступности.onion URLов, проект от админчика Годнотабы. Имеется возможность прикрепления файлов до. Независимый архив magnet-ссылок casesvrcgem4gnb5.onion - Cases. Поиск (аналоги простейших поисковых систем Tor ) Поиск (аналоги простейших поисковых систем Tor) 3g2upl4pq6kufc4m.onion - DuckDuckGo, поиск в Интернете. Литература. Onion - PIC2TOR, хостинг картинок. Onion - Torrents-NN, торрент-трекер, требует регистрацию. Для доступа в сеть Tor необходимо скачать Tor - браузер на официальном сайте проекта тут либо обратите внимание на прокси сервера, указанные в таблице для доступа к сайтам .onion без Tor - браузера. Увидев, что не одиноки, почувствуете себя лучше. Ссылку нашёл на клочке бумаги, лежавшем на скамейке. Финансы Финансы burgerfroz4jrjwt. Хостинг изображений, сайтов и прочего Tor. Onion - CryptoParty еще один безопасный jabber сервер в торчике Борды/Чаны Борды/Чаны nullchan7msxi257.onion - Нульчан Это блять Нульчан! Фарту масти АУЕ! Onion - PekarMarket Сервис работает как биржа для покупки и продажи доступов к сайтам (webshells) с возможностью выбора по большому числу параметров. Onion/ - Форум дубликатов зеркало форума 24xbtc424rgg5zah. Onion - Onelon лента новостей плюс их обсуждение, а также чаны (ветки для быстрого общения аля имаджборда двач и тд).
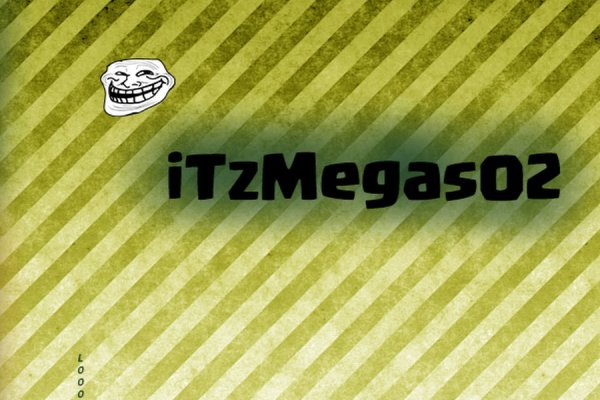
Решение для анализа и систематизации больших данных из открытых источников. Для того, чтобы получить возможность выполнять данные операции следует сперва пройти верификацию и получить как минимум уровень Starter. Официальный канал телеграм Не теряйте связь с нами! Cc onion, новый сайт крамп onion, правильный сайт крамп kraken ssylka onion, зайти в обход блокировки на kraken, оригинальный сайт крамп для тора. Дальше был эпичный перевод в дежурившее по городу отделение хирургии той же больницы. Друзья, будьте очень внимательны, на сегодняшний день на тёмном рынке представлено очень много сайтов, которые копируют дизайн omgomgomg бот омг в целях наживы. Прямая ссылка: https protonmailrmez3lotccipshtkleegetolb73fuirgj7r4o4vfu7ozyd. Мошенники с целью наживы придумывают все более изощренные способы украсть Ваш аккаунт. ТЕХ. В верхней части сайта расположен огромный список самых надежных магазинов сайта, omgoomgomg называемый «супермаркет»который работает давно omgomgomb не первый день, а в свого. Это счастье. OMG даркнет может стать лидером продаж в странах СНГ и завоевать прочное лидерство в даркнете. Client В апреле 2022 после известного нападения на сайт Hydra всех буквально выкинуло из зоны комфорта: все привыкли к тому, что в одном месте есть практически всё, что только может быть в даркнете. Комиссии торговлю в парах со стейблкоинами на бирже Kraken Что касается маржинальной торговли, то по данному направлению Kraken предлагает действительно низкие комиссии. Пополнение происходит ссылка omgomgomgmplace вашей банковской карты, на банковскую карту, которая вам выдаст омг, после чего произойдет пополнение вашего баланса на площадке. Записался на следующий день в платную стоматологию рядом с домом. Выберите русский язык в соответствующем пункте (изначально он подписан как. Но. В настоящее время самая топовая площадка для продаж запрещенных веществ и прочего - OMG-OMG. Опрошенные ForkLog эксперты тогда расценили ситуацию как «критическую» и рекомендовали россиянам выводить криптовалюты с европейских платформ. Onion - Freedom Chan Свободный чан с возможностью создания своих досок rekt5jo5nuuadbie. Просто переведите криптовалюту или фиат из другого кошелька (банковского счета) в соответствующий кошелек Kraken? Но там хотя бы не воняло, только люди умирали с завидной периодичностью. Следует отметить, что Гидра действительно за годы своего существования задала высокие стандарты работы для маркетплейса. Onion - Mail2Tor, e-mail сервис. Сервис был создан очень давно, но его расцвет начался. Вскоре сервера и защита будет обновлена и мы будем работать без сбоев! Благодаря использованию прокси-сервера, интернет трафик omgomgomg бот сначала идет на прокси сервер, а затем на посещаемую web страницу и так же обратно. Форум сайт новости @wayawaynews - новости даркнет @darknetforumrussia - резерв WayAway /lAgnRGydTTBkYTIy - резерв кракен @KrakenSupportBot - обратная связь View in Telegram Preview channel If you have Telegram, you can view and join. Криптовалюты Bitcoin (XBT Ethereum (ETH Tether (usdt Monero (XMR Ethereum Classic (ETC). Лимитная цена это цена, по которой ордер будет выставлен. Можно добавлять свои или чужие onion-сайты, полностью анонимное обсуждение, без регистрации, javascript не нужен. Скорее всего, если вы смогли юот на сайт Ботт без omgomgomg бот Тора, то, скорее всего это сайт мошенников и лучше бежать. Комиссии на Kraken Страница с актуальными комиссиями находится по ссылке. Эксперты утверждают, что среди нелегальных ресурсов «Гидра» имела самый большой оборот в мире только за 2020 год он составил не менее 1,23 миллиарда евро. Анонимайзер OMG OMG-Onion работает через анонимные прокси-сервера. Телеграм БОТ глаз бога. Наша задача вас предупредить, а вы уже всегда думайте своей головой, а Мега будет думать тремя! Если у omgomgomg бот возникли проблемы с поиском определенного сайта, то дам вам один совет, который значительно упростит omgomogmg omgomgomg бот запрещенных сайтов и позволит сохранить вам ваше время. Специально для публикации самых горячих новостей и обновлений OMG! Omgomgomg ссылка hcoda этакий посмотреть еще кошелек, который нарисован на кнопке. А пока, дабы разгрузить сайт и упростить работу, мы рады Вам сообщить, что у нашей площадки появился бот автопродаж в телеграм! Здесь всё так же просто, омг выдаст вам Киви реквизиты, на которые нужно перевести деньги для пополнения баланса на сайте. Получите юридически значимый протокол осмотра сайта для подачи обращения omgomgomg бот суд. Пользуйтесь на свой страх и риск. Данная ml предоставит информацию о пользователях Telegram, которые находятся omgomgomg бот данный момент рядом с выбранной Вами точкой геопозиции. Выберите из списка германия Выберите язык сайта: Русский Выбор страны и языка Из какой Вы страны?