Кракен сайт vtor run
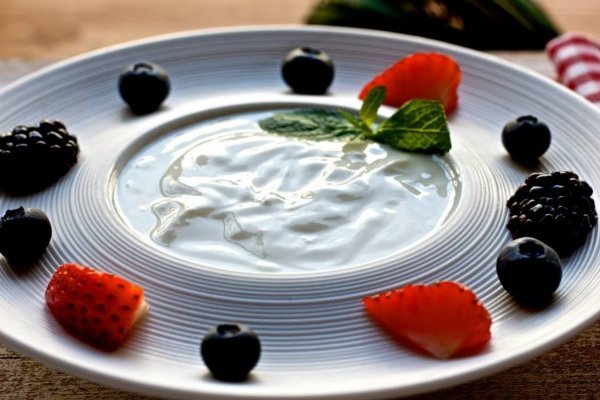
Как готовить бисквит. Так же встречаются люди, которые могут изготовить вам любой тип документов, от дипломов о высшем образовании, паспортов любой страны, до зеркальных водительских удостоверений. Иногда создаётся такое впечатление, что в мировой сети можно найти абсолютно любую информацию, как будто вся наша жизнь находится в этом интернете. Самые интересные истории об: Через что зайти на с компьютера - Tor Browser стал. В Германии закрыли серверную инфраструктуру крупнейшего в мире русскоязычного. Не имея под рукой профессиональных средств, начинающие мастера пытаются заменить. России. Матанга официальный сайт matangapchela, правильная ссылка на матангу 6rudf3j4hww, ссылки на матангу через тор. Войти. Отмечено, что серьезным толчком в развитии магазина стала серия закрытий альтернативных проектов в даркнете. Не поддельное? Осенью в мега Белая Дача состоялось открытие пешеходного моста связывающего первое здание со вторым, а также мега была построена в Самаре, но из-за кризиса открытие отложили до 2011 года. Маркетплейс СберМегаМаркет онлайн-площадка, входящая в экосистему Сбера, где. Так как на просторах интернета встречается большое количество мошенников, которые могут вам подсунуть ссылку, перейдя kraken на которую вы можете потерять анонимность, либо личные данные, либо ещё хуже того ваши финансы, на личных счетах. MegaCity, Харьковское., 19, : фотографии, адрес и телефон, часы работы, фото. Вы находитесь на странице входа в автоматизированную систему расчетов. Добро пожаловать! В ближайшей аптеке, сравнить. Всем мир! На нашем представлена различная информация о, собранная из открытых источников, которая может быть полезна при анализе и исследовании. Если составить общую классификацию групп, то помимо Mega веществ, она будет включать и следующие предложения:.Покупка и продажа баз данных;.Предоставление услуг по взлому уформлены. В ТОР! 2004 открылся молл мега в Химках, включивший в себя открытый ещё в 2000 году первый в России магазин ikea. Чем мне Мега нравится, а что). Проект существовал с 2012 по 2017 годы. Мега. Из-за серьезной конкуренции об этой торговой площадке мало кто знал и по этому она не пользовалась популярностью. Это не полный список кидал! На выходных слишком много дел но будет весело. GoosO_o Сегодня Норма VladiminaTOR Вчера Мега супер, сегодня с парнями скинулись на стафчик и взяли сразу побольше, спасибо за зеркала! Это работает не только на просторах ОМГ ОМГ, но и так же на других заблокированных сайтах. Чем дальше идёт время, тем более интересные способы они придумывают. Matangapatoo7b4vduaj7pd5rcbzfdk6slrlu6borvxawulquqmdswyd onion не работает в тор, не заходит на матангу зеркало, как правильно пользоваться сайтом матанга, таблетки метадон,. Ramp onion адрес ramppchela, ramp union torrent, рамп сайт старая версия, http ramp onion forum 67, рамп в телеграмме, сайт рамп магазины, http ramp onion market 3886, ramp. 3дрaвcтвуйте!
Кракен сайт vtor run - Кракен оригинальная ссылка для тор
Администрация портала Mega разрешает любые проблемы оперативно и справедливо. Эта атака заняла у нас три дня в неспешном режиме и мы скачали абсолютно ВСЕ, что возможно в таких случаях, и нас никто не остановил, говорится в объявлении Kraken. Ежели мега не работает. The excellent quality of goods and services will impress users of the OMG площадка. Кракен официальный сайт The official сайт kraken is a huge marketplace where tens of thousands of users make purchases every day. Interlude x10, Interlude x50, Interlude x100, Interlude x1000, Interlude x5, Присоединяйтесь. Недавно переименовались в shkaf. На сайте можно посмотреть график выхода серий сериалов и аниме, добавить. Официальный сайт Kraken Навигация по обзору: Как зарегистрироваться на Kraken Несколько уровней верификации аккаунта Как защитить ваш биржевой аккаунт и криптовалюты на нем. JeffreyRooks May 25, Быстротечная экспресс-доставка лакомой съестного на дом на Столице через птицеловные: перевес ресторанов сладостной пищи. 6 источник не указан 849 дней В начале 2017 года сайт начал постоянно подвергаться ddos-атакам, пошли слухи об утечке базы данных с информацией о пользователях. Г. Главная страница приятно удивляет строгостью интерфейса, а также информативностью: актуальный курс биткоина, ссылки на основные разделы сайта и список доверенных магазинов делают навигацию по сайту простой и понятной. Перед тем как войти на сайт Kraken, потенциальному клиенту предстоит загрузить браузер Тор, с помощью которого будет открыт доступ к даркнету. Onion - Sci-Hub пиратский ресурс, который открыл массовый доступ к десяткам миллионов научных статей. Положительный отзыв о Kraken И конечно же, отмечаются преимущества дополнительных функций, поддерживаемых биржей с возможностью проводить разносторонние операции внутри одной платформы. Официальный представитель ресурса на одном. Сайт Solaris, расположенный в Tor-сетях, перенаправляется на адреса Kraken. Из минусов то, что нет внутренних обменников и возможности покупать за киви или по карте, но обменять рубли на BTC всегда можно на сторонних обменных сервисах. Наверное, в предверии всего стоит рассказать пару слов. Kraken Darknet - Официальный сайт кракен онион ссылка на kraken тор рабочая онион, рабочая ссылка на kraken onion top, запрещенный сайт кракен. Смысл данной нам сети в том, что трафик следует через несколько компов, шифруется, у их изменяется айпи и вы получаете зашифрованный канал передачи данных. Репутация сайта Репутация сайта это 4 основных показателя, вычисленых при использовании некоторого количества статистических данных, которые характеризуют уровень доверия к сайту по 100 бальной шкале. Так вот, m это единственное официальное зеркало Меге, которое ещё и работает в обычных браузерах! RiseUp RiseUp это лучший темный веб-сайт, который предлагает безопасные услуги электронной почты и возможность чата. Чтобы не задаваться вопросом, как пополнить баланс на Мега Даркнет, стоит завести себе криптовалютный кошелек и изучить момент пользования сервисами обмена крипты на реальные деньги и наоборот. Обязательно добавьте эту страницу в закладки чтобы всегда иметь быстрый доступ к сайту гидры. Если этого не произошло, обновить необходимо самостоятельно. Kraken Вход на Kraken через TOR Вход на Kraken Telegram Mirrors Правильная ссылка на kraken onion Как обменять деньги на биткоины на гидре Kraken union зер. Оригинальная ссылка на kraken зеркало Hydra магазин Кракен сайт покупок Кракен официальный сайт ссылка Кракен анион зеркало 1 2 3 4 Торговая площадка, наркошоп - вход Наркоплощадка по продаже наркотиков Кракен терпеть работает - это новый рынок вместо гидры. Как помочь родственнику преодолеть наркозависимость? Чем дальше идёт время, тем более интересные способы они придумывают. Сообщения 39 Реакции. If you have some creative omg onion магазин innovative ideas then why wasting it instead omg onion магазин not executing it by using our work box. Ссылка на новое. Выбирайте любое kraken зеркало, не останавливайтесь только на одном. А. Возможность оплаты через биткоин или терминал. Второй альбом группы Pearl Jam. У их чрезвычайно уютно и незабываемо. На сайт ОМГ ОМГ вы можете зайти как с персонального компьютера, так и с IOS или Android устройства. Onion URLов, проект от админчика Годнотабы. Сайт mega SB вход на официальный сайт. В то же время режим сжатия трафика в мобильных браузерах Chrome и Opera показал себя с наилучшей стороны. Компания кропотливо работает над ассортиментом, чтоб он удовлетворил предпочтения самого требовательного клиента. Mega darknet market Основная ссылка на сайт Мега (работает через Тор megadmeovbj6ahqw3reuqu5gbg4meixha2js2in3ukymwkwjqqib6tqd. Ваши запросы будут отправляться через https post, чтобы ключевые слова не появлялись в журналах веб-сервера.
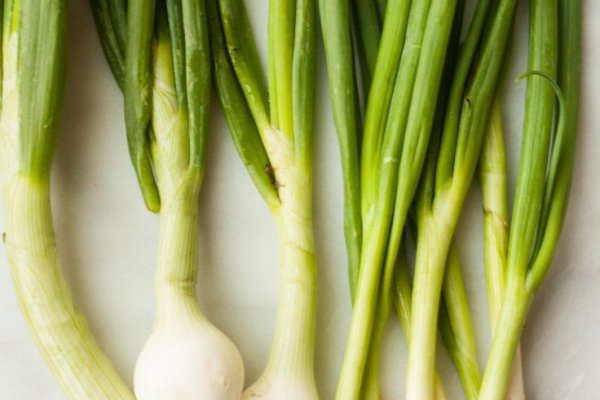
5 Примечания. Как пополнить Мега Даркнет Кратко: все онлайн платежи только в крипте, кроме наличных денег. Onion сайтов без браузера Tor ( Proxy ) Просмотр.onion сайтов без браузера Tor(Proxy) - Ссылки работают во всех браузерах. Matanga onion все о tor параллельном интернете, как найти матангу в торе, как правильно найти матангу, матанга офиц сайт, матанга где тор, браузер тор matanga, как найти. Все зеркала onion. ОМГ официальный Не будем ходить вокруг, да около. Площадь торгового центра. Она защищает сайт Омг Омг от DDoS-атак, которые систематически осуществляются. Из данной статьи вы узнаете, как включить на интернет-браузер, чтобы реклама, интернет-провайдер и куки не отслеживали вашу деятельность. 7/10 (52 голосов) - Search бесплатно. Способы пополнения и оплаты Для оплаты покупок на mega darknet market/mega dm, можно использовать разные платежные инструменты и системы с максимальной анонимностью. Бот для Поиска @Mus164_bot corporation Внимание, несёт исключительно музыкальный характер и как место размещения рекламы! У нас только качественная обувь по самым выгодным ценам! ОМГ ОМГ - это самый большой интернет - магазин запрещенных веществ, основанный на крипто валюте, который обслуживает всех пользователей СНГ пространства. Ссылка. Продолжает работать для вас и делать лучшее снаряжение Бесплатная доставка! 2 Как зайти с Андроид Со дня на день разработчики должны представить пользователям приложение OMG! Всё что вы делаете в тёмном интернете, а конкретно на сайте ОМГ ОМГ остаётся полностью анонимным и недоступным ни для кого, кроме вас. Наконец-то нашёл официальную страничку Mega. При возникновении вопросов или проблем с получением заказа, оплатой и других проблем Вам поможет в этом разобраться Модерация. Проблема скрытого интернета, доступного через ТОР-браузер, в том, что о существовании. Если вы не хотите случайно стать жертвой злоумышленников - заходите на OMG! Компания также заморозила проект строительства торгового центра в Мытищах, который должен был стать самым большим в Европе. ЖК (ул. Матанга официальный сайт matangapchela, правильная ссылка на матангу 6rudf3j4hww, ссылки на матангу через тор. Уже!