Как зайти на кракен браузеры
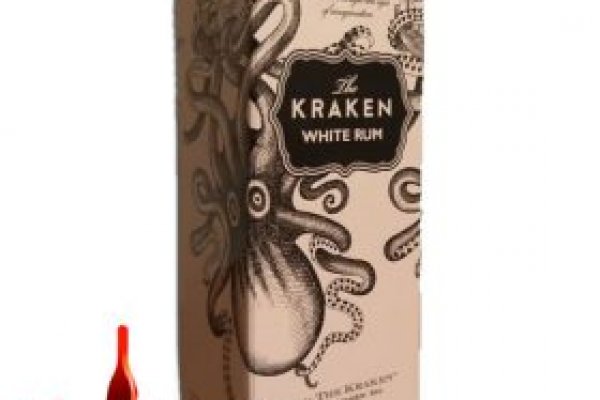
Для того что попасть в Даркнет вам всего лишь надо скачать Tor браузер. Сейчас одна из крупных бирж. Предложение от конкурентов под названием hola! Является зеркалом сайта fo в скрытой сети, проверен временем и bitcoin-сообществом. ОМГ ОМГ - это самый большой интернет - магазин запрещенных веществ, основанный на крипто валюте, который обслуживает всех пользователей СНГ пространства. Приятный дизайн, огромный ассортимент товаров, адекватные цены все это привлекает покупатеелй со всего СНГ. Читать дальше.3k Просмотров Onion сайты как попасть в даркнет и совершить покупку? После обновления приложения до версии.5, авторизуйтесь, а затем. Продажа «товаров» через даркнет сайты Такими самыми популярными товарами на даркнете считают личные данные (переписки, документы, пароли компромат на известнейших людей, запрещенные вещества, оружие, краденые вещи (чаще всего гаджеты и техника фальшивые деньги (причем обмануть могут именно вас). Инструкция для использования OnionTor ссылок Для компьютера: Скачать TOR browser. Для одобрения Legend необходимо обращаться непосредственно в службу техподдержки. Выбирайте любое kraken зеркало, не останавливайтесь только на одном. Оплату на Kraken Darknet принимают криптовалютой Биткоин(BTC она абсолютно анонимна и проста в использовании. Сайт kragl был создан в 2022 году и за короткое время стал известным благодаря широкому выбору товаров и услуг. Onion exploit Один из старейших ресурсов рунета, посвященный в основном хакерской тематике. Всегда. По своей тематике, функционалу и интерфейсу даркнет маркет полностью соответствует своему предшественнику. Условно бесплатная Windows Android iPhone Mac OS SurfEasy VPN шифрует весь интернет-трафик для защиты вашей конфиденциальности в Интернете. Кракен ссылка онион Кракен оригинальное зеркало Площадка Кракен не будет kracc закрыта никогда! Но также существуют и легальные проекты библиотеки, литературные журналы. Это ВПН браузер, который позволяет посещать ресурсы в даркнете. Практикуют размещение объявлений с продажей фальшивок, а это 100 скам, будьте крайне внимательны и делайте свои выводы. Все больше пользователей хотят покупать именно на krmp cc и это не удивительно. С недавних пор onion-технология стала доступна и для смартфонов, работающих на операционной системе iOS, хоть и не в оригинальном виде. Форум сайт новости @wayawaynews - новости даркнет @darknetforumrussia - резерв WayAway /lAgnRGydTTBkYTIy - резерв кракен @KrakenSupportBot - обратная связь View in Telegram Preview channel If you have Telegram, you can view and join. Всем привет, сегодня я расскажу как попасть. Является зеркалом сайта fo в скрытой сети, проверен временем и bitcoin-сообществом. Вариант 1: VPN TOR Browser Приложение объединяет в себе ВПН-сервис и непосредственно сам обозреватель для доступа к Сети. Основным отличием от запущенной в сентябре 2018 года альфа-версии мобильного браузера является то, что теперь прокси-клиент Orbot встроен прямо в Tor его не нужно скачивать и запускать отдельно. Цена: 749 руб. Комиссии на своп торги на бирже Kraken Отметим, что при торговле в паре со стейблкоинами комиссии будут куда более привлекательными, нежели в паре с фиатом. Onion Onion Недорогой и секурный луковый хостинг, можно сразу купить onion домен. Спустя всего пол года после событий с Гидрой появился сайт. Spotflux - это простой в использовании клиент для Mac и ПК (скоро появится и мобильная связь). Отметьте галочкой графы Запрос средств, Запрос открытых ордеров и сделок, Запросить закрытые ордера и сделки, Изменить ордера, Отменить/закрыть ордера, Запрос записей журнала. Onion - SkriitnoChan Просто борда в торе. Я устала. Товары на Кракен Ассортимент товаров поражает воображение - абсолютно любые вещества, информация и услуги, документы и цифровые товары доступны для покупки. Дата старта бета теста. Это бесплатно, но скорость серфинга упадет. 5/5 Ссылка TOR зеркало Ссылка Только TOR TOR зеркало. Сайты kraat в сети Tor располагаются в доменной зоне. Так вы никогда не попадете в Даркнет. А так же неизвестно кто и что вложили в код программы. Если не учитывать краткосрочные падения сайта, площадка работает стабильно и имеет высокую надежность. Что такое kraken и как на него зайти? Onion/rc/ RiseUp Email Service почтовый сервис от известного и авторитетного райзапа lelantoss7bcnwbv.
Как зайти на кракен браузеры - Kra9.gl
Ещё одним решением послужит увеличение вами приоритета, а соответственно комиссии за транзакцию, при переводе Биткоинов. Главное зеркало: mega555kf7lsmb54yd6etzginolhxxi4ytdoma2rf77ngq55fhfcnyid. Union, например ore или новое зеркало, то вы увидите ненастоящий сайт, так как у Mega Url правильная доменная зона. Источник Источник. Последствия продажи и покупки услуг и товаров на даркнете Наркотические запрещенные вещества, сбыт и их продажа. Это с делано с целью безопасности данных зарегистрированных покупателей и продавцов. Частично хакнута, поосторожней. (нажмите). Отзывы о великой Меге встречаются разные. Как использовать. Ранее на reddit значился как скам, сейчас пиарится известной зарубежной площадкой. Главное сайта. Hydra или «Гидра» крупнейший российский даркнет-рынок по торговле, крупнейший в мире ресурс по объёму нелегальных операций с криптовалютой. Сайт Alexa Rank Стоимость сайта m #5,218,321 756.00 USD z #6,741,715 590.40 USD #4,716,352 828.00 USD #13,166 203,860.80 USD - - #9,989,789 410.40 USD Развернуть » Подробная информация о сервере, на котором расположен этот сайт. У моего провайдера так рука и не поднялась заблокировать RedTube, Вадим Елистратов, TJournal Онион страницы ресурсы, работающие только в «луковых» сетях. Ну, вот OMG m. Этот сайт упоминается в онлайн доске заметок Pinterest 0 раз. Onion - torlinks, модерируемый каталог.onion-ссылок. Таких людей никто не любит, руки бы им пообломать. Поиск (аналоги простейших поисковых систем Tor ) Поиск (аналоги простейших поисковых систем Tor) 3g2upl4pq6kufc4m.onion - DuckDuckGo, поиск в Интернете. последние новости Гидра года. Так же попасть на сайт Hydra можно, и обойдясь без Тора, при помощи действующего VPN, а так же если вы будете использовать нужные настройки вашего повседневного браузера. /head секции) в html коде страницы. Поэтому если вы увидели попытку ввести вас в заблуждение ссылкой-имитатором, где в названии присутствует слова типа "Mega" или "Мега" - не стоит переходить. Переполнена багами! Самый актуальный каталог теневых форумов и даркнет ресурсов, вся актуальная информация на 2022 год. Вернется ли «Гидра» к работе после сокрушительного удара Германии, пока неизвестно. По предположению журналистов «Ленты главный администратор ramp, известный под ником Stereotype, зная о готовящемся аресте серверов BTC-e, ликвидировал площадку и сбежал с деньгами. Mega Darknet Market не приходит биткоин решение: Банально подождать. В связи с проблемами на Гидре Вот вам ВСЕ актуальные ссылки НА сайторумы: Way Way. Ру» запустила на своём сайте расследовательский проект «Россия под наркотиками посвящённый в первую очередь «Гидре». Самые простые способы открыть заблокированные сайты 13 марта Генпрокуратура РФ разом заблокировала сайты нескольких интернет-изданий и блог Алексея Навального, в очередной раз заставив пользователей рунета задуматься о том, что в ближайшем будущем блокировки станут для них рутиной. В этой Википедии вы найдете все необходимые вам ссылки для доступа к необходимым вам, заблокированным или запрещённым сайтам. Всё больше людей пытаются избавиться от «отеческой заботы» чиновников от государства и хотят реализовать своё конституционное право самостоятельно решать, куда ходить, что выбирать, куда смотреть и что делать. Среди аналогов Proxyweb и Hide My Ass. Вместо 16 символов будет. .
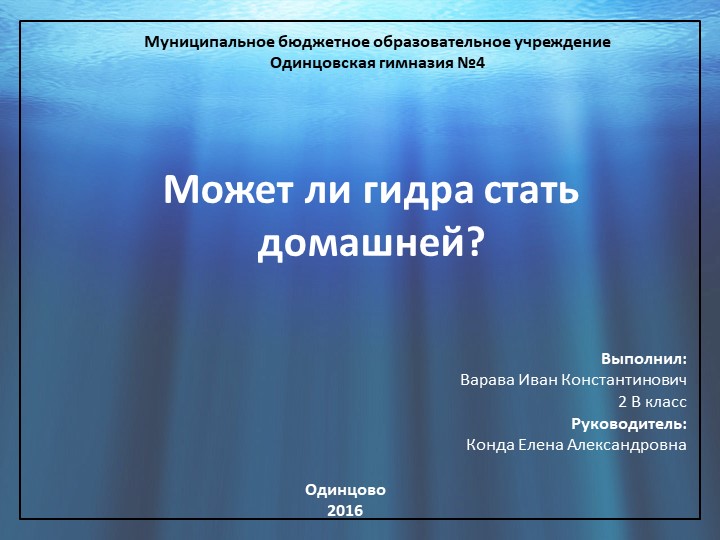
Присутствия собеседника и его близких в соцсетях обнаружить не удалось. Проект Лента. Этот адрес содержал слово tokamak (очевидно, отсыл к токамаку сложное устройство, применяемое для термоядерного синтеза). Он намного больше и обширнее традиционного интернета. Пожелаем им удачи, а сами займёмся более благодарным делом. При этом ни в одном своем сообщении Hydra support не подтвердил сам факт ареста серверов площадки в Германии. Рано утром 5 апреля крупнейшая даркнет-площадка по продаже наркотиков «Гидра» перестала загружаться у всех пользователей. «Гидра» была запущена в 2015 году, когда объединились Way Away и Legal RC, продававшие синтетические каннабиноиды и дизайнерские наркотики, отсутствовавшие на ramp ведущем даркнет-рынке. Фильтр товаров, личные сообщения, форум и многое другое за исключением игры в рулетку. 213 E-mail: Отправить письмо Телефон: 8 (391) Библиотека Буквавед Мой Друг Буква Адреса Интересных Книг - Яндекс Вступай в ряды вольных литераторов! Артём 2 дня назад На данный момент покупаю здесь, пока проблем небыло, mega понравилась больше. Все твои перемещения становится невозможно отследить, как и то, что ты делал. Коммерсантъ В Германии закрыли серверы крупнейшего в мире русскоязычного даркнет-рынка. Данное количество может быть как гарантия от магазина. Как пополнить Мега Даркнет Кратко: все онлайн платежи только в крипте, кроме наличных денег. Для того чтобы войти на рынок ОМГ ОМГ есть несколько способов. Благодаря таким действиям владельцы авто получают шанс выиграть приз! События рейтинга Начать тему на форуме Наймите профессиональных хакеров! Можно утверждать сайт надежный и безопасный. Таких людей никто не любит, руки бы им пообломать. «Вернее, есть но власти как ЕС, так и США заняты другим, по понятным причинам. Как и на любой профильной площадке, в бирже эквайринга можно разместить рекламу. На 15:00. По. Если уж и он не помог - тогда добро пожаловать в Google в поисках решения проблемы. После этого рупор «Гидры» заявил о том, что «сроки восстановления работоспособности проекта будут озвучены в течение дня». Уже само название сети даркнет можно расшифровать как что-то темное или же даже скрытое. Onion - поисковики по сети Tor, хоть один из них, да работает. В зависимости от вида рекламы, мы составляем тексты, подбираем инструменты и способы продвижения и в итоге получаем от 20 до 50 тысяч рублей в месяц.