Kra21gl
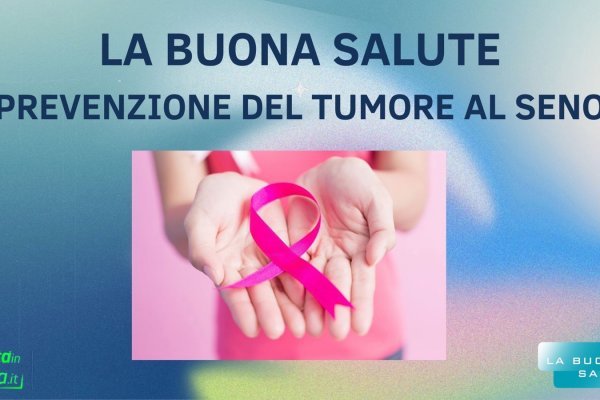
Особенностью «ширки является то, что она может быть употреблена только путем инъекций и ее распространение между потребителями осуществляется в жидком виде. Зависимость от препаратов конопли обычно не сопровождается повышением толерантности и синдром отмены так же выражен слабо. Многие исследователи указывают (и это, зачастую, подтверждается историей что запрет привёл не к снижению, а к увеличению потребления (см.: сухой закон ) вышеозначенных препаратов из-за сверхприбылей незаконного оборота. Таблица. В подпольных лабораториях на юге Франции вырабатывали из полуфабриката героин и везли его в США, оптовым покупателям из «Коза Ностра кубинской и негритянской мафии. Как пишет в своей статье. . Пантелеевой Консультант Плюс. оборот которых ограничен и контролируется; Ограниченные к обороту психотропные вещества ( декстрометорфан, тарен. Из них 184 государства являлись сторонами Конвенции 1961 года с поправками, внесёнными в неё в соответствии с Протоколом 1972 года. Золотой треугольник. Считается, что термин «ναρκωτικός» (наркотик) впервые был употреблён греческим целителем Гиппократом, в частности, для описания kracc веществ, вызывающих потерю чувствительности или паралич. Относительно редко встречающимся наркосодержащим растением является кока (. В колумбийцы, которые раньше ограничивались ролью посредников, вытеснили кубинцев и захватили в свои руки львиную долю (до 80) американского кокаинового рынка. Синдром отмены Симптомы отмены, вызванные уменьшением количества никотина в организме, могут проявляться от нескольких дней до нескольких недель 60 Основная статья: Абстинентный синдром Аляется. В целом все наркотические вещества опасны для психики и здоровья человека. Также синдром приобретенного иммунодефицита (спид). Явления толерантности и синдрома отмены особенно характерны для опиатной зависимости, зависимости от алкоголя и снотворных. Он входил во многие аптечные успокоительные и снотворные средства. Весь «производственный цикл» наркобизнеса сильно напоминает деятельность транснациональных корпораций как по денежным оборотам, так и по методам организации. Медельинский наркокартель допустил две серьезные ошибки: бросил политический вызов властям, объявив войну правительству, и одновременно наращивал производство и экспорт кокаина. 6, Bulletin on Narcotics: A Century of International Drug Control United Nations Publications, 2010; isbn, isbn Том LIX, стр. Во-вторых, начался очередной сдвиг в географии производства. К началу 2000-х в Андском треугольнике сложилась парадоксальная ситуация: почти все мало-мальски крупные наркоторговцы сидели в тюрьмах или лежали в гробах, но поток кокаина почти не пересыхал, посевы наркокультур также существенно не сокращались. "О признании алкоголя ядом и наркотиком". Архивировано года. Еще одна особенность этой группы наркотиков сильнейшая ломка или абстинентный синдром. Наркология. Если экономическая история героинового рынка демонстрирует провал борьбы с наркобизнесом из-за его перемещения из одного региона в другой, то на кокаиновом «фронте» такая миграция невозможна, что, казалось бы, должно было принести успех силам правопорядка. Одновременно силовые ведомства (ФБР, Бюро по борьбе с наркотиками и другие) проводят политику суровых репрессий против наркоторговцев не только в самой Америке, но и в других странах (особенно, в Латинской Америке). Безопасные Безопасных наркотиков нет! Также Примечания Комментарии По мнению известного британского врача-нарколога Дэвида Натта, из наиболее распространенных наркотиков наибольший вред здоровью потребителя наносят (по убывающей) героин, крэк и метамфетамин. Исторический аспект Основная статья: История наркотиков Возраст исторических свидетельств об изготовлении и употреблении психоактивных веществ насчитывает более семи тысяч лет. Эти препараты обладают выраженным седативным эффектом, при превышении дозировки вызывают эйфорию у наркомана. Многие наркотические препараты свободно продавались в аптеках как болеутоляющие или снотворные лекарства. Специальная сессия Генеральной Ассамблеи, посвященная совместной борьбе с мировой проблемой наркотиков (Нью-Йорк, 8 года) / m Юрий Латов.
Kra21gl - Kra28at
Немаловажно, что mega market onion не имеет java Script, но работает корректно (заблокированная Гидра не давала нормально пользоваться сайтом без установки фильтра). С помощью этого торгового хаба вы сможете покупать не только запрещенные вещества и предметы, которые раньше продавались на Гидре, но и иметь все гарантии собственной анонимности. Екатерина Владимировна. Мега Даркнет Маркет это крупнейшая торговая платформа в Даркнете, которая начала свою деятельность сравнительно недавно и быстро стала популярной. После успешного создания аккаунта, в разделе с кнопками «Войти» или «Зарегистрироваться» вы увидите несколько полезных инструментов: Кнопка слева позволяет поменять тему на темную; Иконка с тележкой супермаркета отображает список заказов; Конверт открывает мессенджер для общения с продавцами/клиентами. В случае с Монеро дела обстоят совершенно иначе, да и переводы стоят дешевле. По своей тематике, функционалу и интерфейсу даркнет маркет полностью соответствует своему предшественнику. Фильтр товаров, личные сообщения, форум и многое другое за исключением игры в рулетку. «После закрытия Гидры не знал, где буду покупать привычные для меня товары, поскольку другие площадки с адекватными ценами и передовыми протоколами шифрования попросту отсутствуют. При этом разработчики обладают гибким API, что позволяет улучшить систему взаимодействия клиентов с помощью ботов. Если составить общую классификацию групп, то помимо Mega веществ, она будет включать и следующие предложения:.Покупка и продажа баз данных;.Предоставление услуг по взлому уформлены. Сайты также расположены на онион доменах работающих в Тор браузере. Что делать если площадка не работает? Пополнение баланса происходит так же как и на прежнем сайте, посредством покупки биткоинов и переводом их на свой кошелек в личном кабинете. Любые мошеннические действия исключены, ведь торговая платформа сама придерживается честной политики и способствует разрешению любых споров. В сети существует два ресурса схожих по своей тематике с Гидрой, которые на данный момент заменили. В связи с этим, мы подготовили несколько актуальных ссылок mega onion link, которые позволят обойти все ограничения: mega555kf7lsmb54yd6etzginolhxxi4ytdoma2rf77ngq55fhfcnyid. Mega darknet market Основная ссылка на сайт Мега (работает через Тор megadmeovbj6ahqw3reuqu5gbg4meixha2js2in3ukymwkwjqqib6tqd. Соответствующая кнопка находится в самой нижней части интерфейса. Всем мир! В первую очередь следует найти ссылку Мега Даркнет Маркет для Тор. Воспользоваться порталом с помощью обычного браузера не удастся, поэтому потребуется выполнить несколько действий по обходу запретов. Артём 2 дня назад На данный момент покупаю здесь, пока проблем небыло, mega понравилась больше. Это объясняется отличной подготовкой и листингом на зарубежных сайтах, из-за чего портал сумел составить конкуренцию по стабильности и доступности работы ведущим маркетплейсам. Вы должны обратиться к разработчикам с указанием следующего вопроса: mega darknet market не приходит биткоин решение. Оплата за товары и услуги принимается также в криптовалюте, как и на Гидре, а конкретнее в биткоинах. Условия взаимодействия клиента с дилером максимально честные и прозрачные, поскольку каждый поставщик проходит многократную проверку». / mega вход Общая информация об маркетплейсе Mega Как известно, легендарная площадка Мега Даркнет была создана примерно в одно время с Гидрой, но из-за влияния «трехглавой» она долго оставалась в тени и не имели столь широкого распространения. Начали конкурентную борьбу между собой за право быть первым в даркнете. Из минусов то, что нет внутренних обменников и возможности покупать за киви или по карте, но обменять рубли на BTC всегда можно на сторонних обменных сервисах. Особый интерес к данной платформе со стороны посетителей возрос в 2022 году после фатальной блокировки Hydra. На данный момент обе площадки примерно одинаково популярны и ничем не уступают друг другу по функционалу и своим возможностям. Что можно купить в маркетплейсе Мега. Раздел для дилеров Мега Даркнет За счет невысокой конкуренции и технически продвинутого интерфейса, mega darknet market и его зеркало предлагает отличные возможности для дилеров. В итоге купил что хотел, я доволен. Функционал и интерфейс подобные, что и на прежней торговой площадке. «Пользуюсь Мегой достаточно долго, даже еще во времена пика популярности трехглавой. Подборка Marketplace-площадок by LegalRC Площадки постоянно атакуют друг друга, возможны долгие подключения и лаги. Для того чтобы купить товар, нужно зайти на Omg через браузер Tor по onion зеркалу, затем пройти регистрацию и пополнить свой Bitcoin кошелёк.
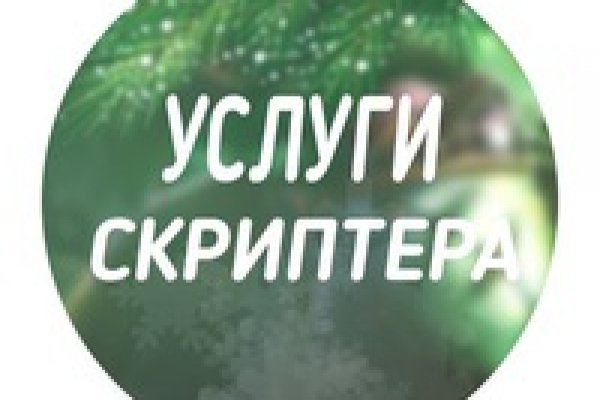
Интуитивное управление Сайт сделан доступным и понятным для каждого пользователя, независимо от его навыков. Такой глобальный сайт как ОМГ не имеет аналогов в мире. Просмотр. Оплата картой или криптой. Если быть точнее это зеркала. Отдельной строкой стоит упомянуть и сервис Vemeo, который, как и TunnelBear, присутствует на всех основных платформах, однако стоит 3,95 доллара в месяц, так что его трудно рекомендовать для любительского использования. Ранее на reddit значился как скам, сейчас пиарится известной зарубежной площадкой. Просмотр.onion сайтов без браузера Tor(Proxy). Основные html элементы которые могут повлиять на ранжирование в поисковых системах. Купить билет на самолет стало еще. Программа распространяется бесплатно и не требует глубоких знаний. Foggeddriztrcar2.onion - Bitcoin Fog микс-сервис для очистки биткоинов, наиболее старый и проверенный, хотя кое-где попадаются отзывы, что это скам и очищенные биткоины так и не при приходят их владельцам. Данное количество может быть как гарантия от магазина. Книжная купить по выгодной цене на АлиЭкпресс. Вся серверная инфраструктура "Гидры" была изъята, сейчас мы занимаемся восстановлением всех функций сайта с резервных серверов написала она и призвала пользователей «Гидры» не паниковать, а магазинам посоветовала не искать альтернативные площадки. Возможность оплаты через биткоин или терминал. Присутствует доставка по миру и перечисленным странам. Кардинг / Хаккинг. Напоминает slack 7qzmtqy2itl7dwuu. Даркмаркет направлен на работу в Российском рынке и рынках стран СНГ. 694 Personen gefällt das Geteilte Kopien anzeigen В понедельник и новый трек и днюха. Без воды. Hansamkt2rr6nfg3.onion - Hansa зарубежная торговая площадка, основной приоритет на multisig escrow, без btc депозита, делают упор на то, что у них невозможно увести биточки, безопасность и всё такое. Кардинг / Хаккинг Кардинг / Хаккинг wwhclublci77vnbi. Стоит помнить внешний вид Мега Шопа, чтобы не попасть на фейки. Топчик зарубежного дарквеба. Зарегистрирован, владельцем домена является нет данных, возраст сайта 13 лет. Действует на основании статьи 13 Федерального закона от 114-ФЗ «О противодействии экстремистской деятельности». Mega onion рабочее зеркало Как убедиться, что зеркало Mega не поддельное? Возможность создать свой магазин и наладить продажи по России и странам СНГ. Для Android есть его аналог под названием Orweb.