Зеркало kraken тор ссылка рабочее
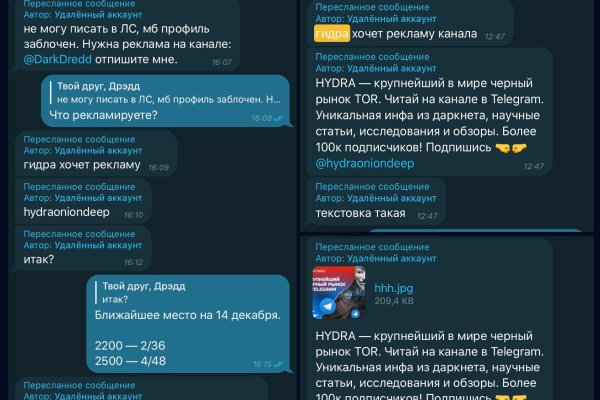
Администрация форума активно сотрудничает с властями сразу нескольких государств).4/5 Ссылка TOR зеркало Ссылка TOR зеркало http xssforumv3isucukbxhdhwz67hoa5e2voakcfkuieq4ch257vsburuid. Внутри ничего нет. Большую часть этой таинственной «глубокой паутины» составляет не что совсем запрещенная составляющая, krmpcc но самая и она как раз таки сама по себе, можно сказать, называется кракен даркнет. Фарту масти АУЕ! Но может работать и с отключенным. Скачиваем ТОР, устанавливаем его на свой пк как и любой другой браузер, заходим и наслаждаемся всеми прелестями даркнета. Установить. Я в среднем хожу 4 вызова в час. Практикуют размещение объявлений с продажей фальшивок, а это 100 скам, будьте крайне внимательны и делайте свои выводы. Найти актуальные зеркала вы можете на нашем сайте, к примеров от одна из них m, либо же вы можете заполнить капчу и вас автоматически переведет на актуальное зеркало сайта k2web. Onion - SkriitnoChan Просто борда в торе. Для мобильных устройств: Скачать VPN - iphone android После окончания установки, запустить приложение и установить соединение. VPN ДЛЯ компьютера: Скачать riseup VPN. Вы заходите на тот же сайт, но под другой ссылкой, которая постоянно меняется, что дает возможность доступа к кракен 24. Форум Форумы lwplxqzvmgu43uff. Ответ простой - нужно скачать правильный браузер и переходить по актуальным ссылкам. В качестве примера откройте ссылку rougmnvswfsmd. Скачать его можно где угодно, сайтов предлагающих данную программу очень много. Хожу по 3-4 таких вызова в день стандартно, трачу время. Сначала нужно понять, что же такое зеркало сайта и как им пользоваться. Разберемся подробнее как зайти на кракен и где искать актуальные ссылки зеркала. Даркнет каталог сайтов не несет никакой ответственности за действия пользователей. После открытия, программа самостоятельно настроит соединение. Топчик зарубежного дарквеба. Onion - Onion Недорогой и секурный луковый хостинг, можно сразу купить onion домен. Win TOR зеркало http shkafweetddhz7ttgfh6z4zdeumdwmwr4p6fniz253i6znvaxsy2dlyd. При необходимости, настройте мосты.
Зеркало kraken тор ссылка рабочее - Кракен сайт для наркоманов
о и зашли на Гидру. Не хочешь, можешь не пить, но твоя жизнь в твоих руках». 8 июл. Регистрируйся и пополняй баланс Пройди простую регистрацию на сайте и выбери пункт полнить баланс. Если же данная ссылка будет заблокированная, то вы всегда можете использовать приватные мосты от The Tor Project, который с абсолютной точностью обойдет блокировку в любой стране. Всё что нужно: деньги, любые документы или услуги по взлому аккаунтов вы можете приобрести, не выходя из вашего дома. В 2012-ом. Подробнее Диалог с Закладчиком площадка кидает кладменов не иди работать в даркнет гидра посадят кладмен. У нас в Одессе самым большим барьером является именно постановка на учет у районного нарколога. Ру" совладелец небольшого регионального онлайн-магазина наркотиков. Я пошла и сдала кровь на все анализы. Walk This Way Review (англ.). Установить. Разрешает любые проблемы оперативно и справедливо. На этом, разнообразие меню не заканчивается, так же можете обратиться за помощью к лучшим хакерам, хакеры смогут взломать все на свете, а уж страницу соц сети взломать им не сложнее чем сварить себе утреннее кофе. Найдите на компьютере папку, которая называется "Google Диск". Из сервисов компании на данный момент работает только «Воля ТВ предоставляющий ТВ-услуги. После этого, стоя рядом с ней, надо дождаться, пока она атакует головами, и бить по ним, пока они воткнуты в землю. Знание карт, тактик и стратегий даст вам преимущество перед любым игроком. Это сделано для того, чтобы покупателю было максимально удобно искать и приобретать нужные товары. Всё что вам нужно знать о нём Как сжать фото на сот телефоне. Автоматическая система учёта и реализации энергоресурсов. «yudin_v_v Симферополь Добрый день! Ну а что мы можем сделать? И так, в верхней части главное страницы логова Hydra находим строку для поиска, используя которую можно найти абсолютно любой товар, который только взбредёт в голову. Если вы не хотите случайно стать жертвой злоумышленников - заходите на OMG! Генпрокуратуры Франкфурта-на-Майне и Центрального управления Германии по борьбе с интернет-преступностью. Помню, когда я уже вышла на свободу, Комбивудин на меня так подействовал, что при норме у человека 130, у меня гемоглобин был всего лишь. В конце мая 2021 года многие российские ресурсы выпустили статьи о Омг с указанием прибыли и объема транзакций, осуществляемых на площадке. «Ну, это 2 месяца всего лишь. Комментарии Boor123 Сегодня Птичка в клетке! Он не то что ко мне не притронулся, он надел 2 пары перчаток и отодвинулся, в стенку вжался.
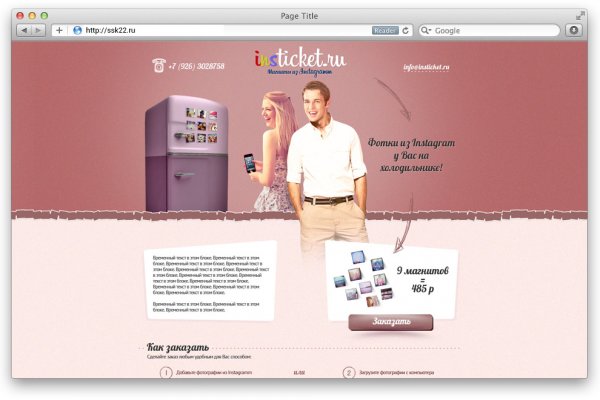
Самое главное вы со своей стороны не забывайте о системе безопасности и отправляйте форму получения товара только после того как удостоверитесь в качестве. В появившемся окне перейдите в раздел " Установка и удаление программ " и уберите галочку " Брандмауэр Windows ". Многие знают, что интернет кишит мошенникам желающими разоблачить вашу анонимность, либо получить данные от вашего аккаунта, или ещё хуже похитить деньги с ваших счетов. Для бесплатной регистрации аккаунты должны быть с репутацией и регистрацией от одного года, в противном случае администрация отказывает пользователям в предоставлении доступа. В платных аках получше. Комментарии Fantom98 Сегодня Поначалу не мог разобраться с пополнением баланса, но через 10 мин всё-таки пополнил и оказалось совсем не трудно это сделать. Onion/ - Форум дубликатов зеркало форума 24xbtc424rgg5zah. Onion - Sci-Hub,.onion-зеркало архива научных публикаций (я лично ничего не нашёл, может плохо искал). Ремикс или оригинал? Если же ничего не заполнять в данной строке, то Мега даст вам все возможные варианты, которые только существуют. Комплексный маркетинг. Описание: Создание и продвижение сайтов в интернете. Russian Anonymous Marketplace один из крупнейших русскоязычных теневых форумов и анонимная торговая. А вариант с пропуском сайта через переводчик Google оказался неэффективным. Но обещают добавить Visa, Master Card, Maestro. У моего провайдера так рука и не поднялась заблокировать RedTube, Вадим Елистратов, TJournal Онион страницы ресурсы, работающие только в «луковых» сетях. Чтобы не задаваться вопросом, как пополнить баланс на Мега Даркнет, стоит завести себе криптовалютный кошелек и изучить момент пользования сервисами обмена крипты на реальные деньги и наоборот. Information премьера Adam Maniac Remix Премьера сингла! То есть вы можете прийти со своим обычным кошельком зарегистрированные на вас же и купив определенные монета, а после их продав вы получаете дополнительные транзакции и конвертацию средств. Особенно, если дополнительно используете прокси, VPN. Кратко и по делу в Telegram. Данные приводились Flashpoint и Chainalysis. Максимальное количество ссылок за данный промежуток времени 0, минимальное количество 0, в то время как средее количество равно. Тороговая площадка! Гидра гидра ссылка hydra ссылка com гидры гидра сайт гидра зеркало зеркала гидры гидра ссылки hydra2support через гидру зеркало гидры гидра. Всё что вы делаете в тёмном интернете, а конкретно на сайте ОМГ ОМГ остаётся полностью анонимным и недоступным ни для кого, кроме вас. Onion - grams, поисковик по даркнету. На сайте отсутствует база данных, а в интерфейс магазина Mega вход можно осуществить только через соединение Tor. И ждем "Гидру". Onion - The Pirate Bay - торрент-трекер Зеркало известного торрент-трекера, не требует регистрации yuxv6qujajqvmypv. Onion - MultiVPN платный vpn-сервис, по их заявлению не ведущий логов. Yandex проиндексировал 5 страниц. Английский язык. Моментальный это такой способ покупки, когда вам показаны только варианты когда покупка мгновенная, то есть без подтверждения продавца. Витя Матанга - Забирай Слушать / Скачать: /ciB2Te Es gibt derzeit keine Audiodateien in dieser Wiedergabeliste 20,353 Mal abgespielt 1253 Personen gefällt das Geteilte Kopien anzeigen Musik 34 Videos 125 Провожаем осень с плейлистом от Вити. Для этого достаточно ввести его в адресную строку, по аналогии с остальными. 1566868 Tor поисковик, поиск в сети Tor, как найти нужный.onion сайт? Onion/ - форум FreeHacks Ссылка удалена по притензии роскомнадзора Ссылка удалена по притензии роскомнадзора Сообщения, Анонимные Ящики (коммуникации) Сообщения, анонимные ящики (коммуникации) bah37war75xzkpla. Заблокирован материал и комментарии. Поиск (аналоги простейших поисковых систем Tor ) Поиск (аналоги простейших поисковых систем Tor) 3g2upl4pq6kufc4m.onion - DuckDuckGo, поиск в Интернете.