Кракен браузер ссылка
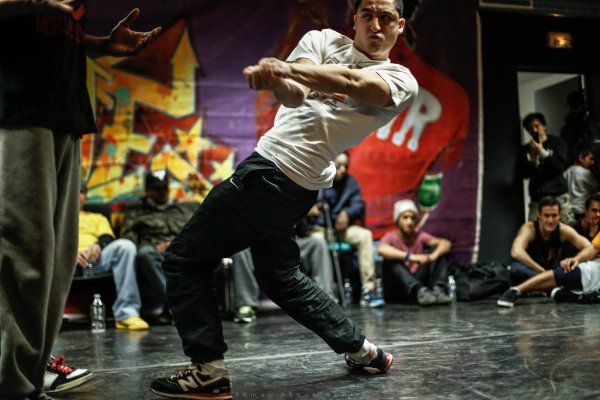
Russian Anonymous Marketplace один из крупнейших русскоязычных теневых форумов и анонимная торговая. Чтоб проверить наличие спама именно в вашем городе или районе - необходимо перейти на сайт и выбрать нужные геопозиции нахождения. Рейтинг продавца а-ля Ebay. Так вот, m это единственное официальное зеркало Меге, которое ещё и работает кракен в обычных браузерах! Hbooruahi4zr2h73.onion - Hiddenbooru Коллекция картинок по типу Danbooru. Onion - Freedom Chan Свободный чан с возможностью создания своих досок rekt5jo5nuuadbie. Кратко и по делу в Telegram. Html верстка и анализ содержания сайта. Низкие цены, удобный поиск, широкая география полетов по всему миру. Но речь то идёт о так называемом светлом интернете, которым пользуются почти все, krn но мало кому известно такое понятие как тёмный интернет. 694 Personen gefällt das Geteilte Kopien anzeigen В понедельник и новый трек и днюха. Для этого используют специальные PGP-ключи. Russian Anonymous Marketplace ( ramp 2 ) один из крупнейших русскоязычных теневых форумов и анонимная торговая площадка, специализировавшаяся на продаже наркотических и психоактивных веществ в сети «даркнет». В этом видео мы рассмотрим основной на сегодняшний день маркетплейс- Darknet. Только сегодня узнала что их закрылся. Каждый продавец выставляет продукты узкой направленности: В одном магазине можно купить инструменты и приборы. В октябре 2021. Торрент трекеры, Библиотеки, архивы Торрент трекеры, библиотеки, архивы rutorc6mqdinc4cz. Среди аналогов Proxyweb и Hide My Ass. Возможные причины блокировки: единый реестр доменных имен, указателей страниц сайтов в сети «Интернет» и сетевых адресов, содержащие информацию, распространение которой в Российской Федерации запрещено. Хороший и надежный сервис, получи свой.onion имейл. Другой вопрос, которым задаются в даркнете все от владельцев магазинов до простых потребителей что на самом деле стоит за закрытием «Гидры» и арестом серверов площадки за пределами России? Есть много полезного материала для новичков. Ссылки на главной странице Отношение исходящих ссылок к внутренним ссылкам влияет на распределение веса страниц внутри сайта в целом. Сведение: Steve Бит: Black Wave официальный Братская поддержка: Даня Нерадин 698 Personen gefällt das Geteilte Kopien anzeigen В 00:00 по МСК, премьера "Витя Матанга - Забирай"! Ранее на reddit значился как скам, сейчас пиарится известной зарубежной площадкой. Форумы.
Кракен браузер ссылка - Рабочая ссылка кракен в тор
Всяческие политико-революционно-партизанские ресурсы здесь не привожу намеренно. Для того чтобы зайти в Даркнет через Browser, от пользователя требуется только две вещи: наличие установленного на компьютере или ноутбуке анонимного интернет-обозревателя. Главное зеркало. Ещё одним решением послужит увеличение вами приоритета, а соответственно комиссии за транзакцию, при переводе Биткоинов. Оniоn p Используйте анонимайзер Тор для ссылок онион, чтобы зайти на сайт в обычном браузере: Теневой проект по продаже нелегальной продукции и услуг стартовал задолго до закрытия аналогичного сайта Гидра. Финансы Финансы burgerfroz4jrjwt. Во-первых, в нём необходимо вручную выбирать VPN нужной страны. У них нет реального доменного имени или IP адреса. TJournal попробовал самые популярные средства обхода блокировок и нашёл среди них версии «для чайников» в которых всё работает сразу, без настроек. Простота, удобство, возможность выбора гарантов и фокус на анонимности и безопасности - их фишка. Почему пользователи выбирают Mega? Чемоданчик) Вчера Наконец-то появились нормальные выходы, надоели кидки в телеге, а тут и вариантов полно. Как мы знаем "рынок не терпит пустоты" и в теневом интернет пространстве стали набирать популярность два других аналогичных сайта, которые уже существовали до закрытия Hydra. Теперь о русских сайтах в этой анонимной сети. Добавить комментарий. Ещё есть режим приватных чат-комнат, для входа надо переслать ссылку собеседникам. Точнее его там вообще нет. Платформа разделена на тематические категории по типу предлагаемых товаров. Onion - BitMixer биткоин-миксер. Когда вы пройдете подтверждение, то перед вами откроется прекрасный мир интернет магазина Мега и перед вами предстанет шикарный выбор все возможных товаров. Он отличается простотой в использовании не добавляет собственную рекламу. Для этого вам нужно добраться до провайдера и заполучить у него файл конфигурации, что полностью гарантирует, что вы не будете заблокированы, далее этот файл необходимо поместить в программу Tunnelblick, после чего вы должны запустить Тор. Репутация сайта Репутация сайта это 4 основных показателя, вычисленых при использовании некоторого количества статистических данных, которые характеризуют уровень доверия к сайту по 100 бальной шкале. Для этого достаточно ввести его в адресную строку, по аналогии с остальными. Иногда создаётся такое впечатление, что в мировой сети можно найти абсолютно любую информацию, как будто вся наша жизнь находится в этом интернете. В бесплатной версии приложения доступно всего 500 мегабайт трафика в месяц, а годовой безлимит обойдется в 979 рублей (и это только цена для устройств на iOS). Особых знаний для входа на сайт Мега не нужно - достаточно просто открыть браузер, вставить в адресную строку Мега ссылку, представленную выше, и перейти на сайт. Это защитит вашу учетную запись от взлома. Требует включенный JavaScript. Сеть для начинающих. Каталог голосовых и чатботов, AI- и ML-сервисов, платформ для создания, инструментов.возврата средств /фальш/ дейтинг и все что запрещено Законами Украины. 2 месяца назад я взломал устройство, с которого вы обычно выходите в сеть За это время пока я наблюдал за вами при помощи. Этот и другие сайты могут отображаться в нём. Литература. Сайт Alexa Rank Стоимость сайта m #5,218,321 756.00 USD z #6,741,715 590.40 USD #4,716,352 828.00 USD #13,166 203,860.80 USD - - #9,989,789 410.40 USD Развернуть » Подробная информация о сервере, на котором расположен этот сайт. Форум Форумы lwplxqzvmgu43uff. Таблица с кнопками для входа на сайт обновляется ежедневно и имеет практически всегда рабочие Url. Onion - OnionDir, модерируемый каталог ссылок с возможностью добавления. Загрузка. Tetatl6umgbmtv27.onion - Анонимный чат с незнакомцем сайт соединяет случайных посетителей в чат. Onion - onelon, анонимные блоги без цензуры. Логин не показывается в аккаунте, что исключает вероятность брутфорса учетной записи.
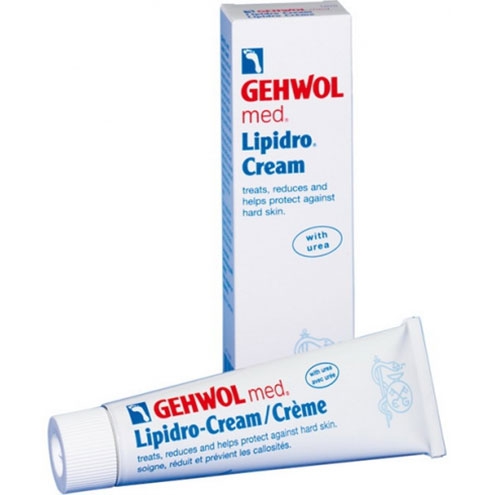
99 руб. Ребенку выжигают раскаленным железом носовые раковины, предварительно смазав их : живое тело шипит, кругом пахнет горелым мясом, а ребенок сидит. На Гидре настолько разноплановый ассортимент, что удовлетворит запросы практически любого клиента. Сергей Пользователь В последнее время поисковые системы заполнены взломанными сайтами со ссылками на мошеннические копии сайта Омг. Зеркала рамп 2021 shop magnit market xyz, ramp не работает почему, рамп магадан сайт, рамп. Onion сайтов без браузера Tor ( Proxy ) Просмотр.onion сайтов без браузера Tor(Proxy) - Ссылки работают во всех браузерах. Matangapatoo7b4vduaj7pd5rcbzfdk6slrlu6borvxawulquqmdswyd onion не работает в тор, не заходит на матангу зеркало, как правильно пользоваться сайтом матанга, таблетки метадон,. Ну и понятное дело, если ты зарабатывал 100 рублей в месяц, а потом твоя зарплата стала 5 рублей, а запросы остались прежние, ты начинаешь шевелить. Похожие каналы. Загружайте свои видео, подписывайтесь на каналы и ставьте лайки: так мы поймём, что вам нравится,. Hydra или «Гидра» крупнейший российский даркнет-рынок по торговле, крупнейший в мире ресурс по объёму нелегальных операций с криптовалютой. Разгромлен самый крупный рынок в даркнете. Доставка курьером сегодня от 0 в интернет-аптеке сбер еаптека с круглосуточной ㉔ доставкой Заказать доставку или забрать в нашей аптеке. Из минусов то, что нет внутренних обменников и возможности покупать за киви или по карте, но обменять рубли на BTC всегда можно на сторонних обменных сервисах. Вся продукция в наличии Быстрая доставка любым удобным способом. Ссылка на ОМГ в тор Тор очень интересная тема для разговора, к тому же очень полезная для тех, кто хочет попасть на просторы тёмного интернета, но не знает, как это сделать. Респект модераторам! Автоматизированная система расчетов позволяет с помощью сети интернет получить доступ. У кого нет tor, в канале инфа и APK файл, для тор. Отделение на рабочие и scam зеркала. 37 вопросов по теме «Гидра». Создание электронной музыки при помощи программного обеспечения.