Кракен нарко
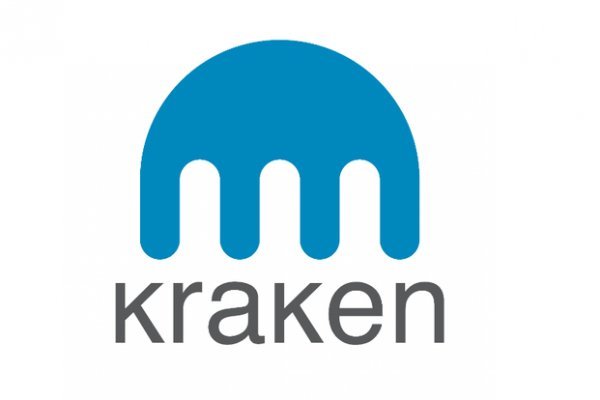
Интернету. Это не значит, что злоумышленников даркнете невозможно вычислить. В Tor есть пути обхода подобных блокировок, однако задача властей состоит в том, чтобы усложнить использование браузера и вызвать проблемы у пользователей, рассказывал ранее руководитель глобальной штаб-квартиры Group-IB в Сингапуре Сергей Никитин. Наша. Onion - Lelantos секурный и платный email сервис с поддержкой SMTorP tt3j2x4k5ycaa5zt. Русскоязычный маркетплейс, на котором можно было купить наркотики и некоторые виды поддельных документов, работал с 2015 года. Пытаюсь перейти на поисковики(Torch, not Evil) через TOR, и на любые другие onion сайты, получаю это: Invalid Onionsite Address The provided onionsite address is invalid. Кроме русского в топ-5 языков даркнета присутствуют английский, португальский, испанский и арабский. В теневом интернете свободно продается оружие, а также нелегальные услуги самого разного рода: например, там можно взять в аренду сетевых ботов или заказать кибератаку у профессиональных хакеров. Кстати, через легко устанавливаемый браузер Tor можно выходить не только в даркнет, но и в обычный интернет, сохраняя при этом анонимность. . Kraken.com не используйте ссылки, предлагаемые в строке. Затем тор следует найти целевую беспроводную сеть (для нашего практического примера был использован маршрутизатор «Null Byte. Гидра является онлайн -магазином, предлагающим товары с узкой направленностью. Здесь вы узнаете о том, как зайти на Гидру с телефона,. Source: A video screenshot, Reuters Напомним, Гидра торговая площадка является сайтом, где любой желающий может покупать и продавать товары «серого рынка». Прокси-сервер Следующая технология подобна VPN и подразумевает подмену местоположения благодаря подключению через сторонний компьютер, расположенный в любой точке мира. Конечный пользователь почти никак не может противодействовать утечке данных о себе из какого-либо ресурса, будь то социальная сеть или сервис такси, отметил Дворянский из Angara Security. Чтобы зайти на Гидру используйте Тор-браузер или ВПН. Это если TOR подключён к браузеру как socks-прокси. C уважением Администрация. В ВТБ Би-би-си ответили, что используют "все имеющиеся возможности по противодействию киберугрозам, в том числе изучение информации из различных источников". Даркнет - это еще и нелегальный рынок персональных данных, источником утечек часто становятся банки. Про связь с СБУ заговорили, только когда официальная пресса назвала наркокартель частью гибридной войны против России. Если ты заметил какую-либо неработающую ссылку, то напиши мне об этом Или это частная как перевести деньги на гидру закрытая сеть, доступ к которой имеют лишь ее создатели и те кому нужно. Биржа Kraken принадлежит компании Payward Inc. "Tor обеспечил бесцензурный доступ в интернет почти 36 миллионам человек во всем мире, позволяя им контролировать свою конфиденциальность и анонимность отмечается в обосновании к присуждения премии. Внутри даркнета не действуют законы каких-либо стран. Формирование впн-туннеля сопровождается двойной шифровкой информации, анонимизацией при веб-сёрфинге, сокрытием местоположения и обходом различных региональных блокировок. "Большая часть закрытых площадок требует внедрения в организованную преступность, поэтому мы уделяем внимание по большей части открытым или серым зонам даркнета, - продолжает Колошенко. Материал по теме Можно ли заблокировать даркнет Регуляторы пытаются ограничить доступ к сети Tor, но адресно заблокировать конкретный сайт в даркнете технически невозможно, рассуждает директор центра противодействия кибератакам Solar jsoc компании «Ростелеком-Солар» Владимир Дрюков. Услуги вне интернета сводятся к операциям по обналичиванию похищенных денежных средств и распространению наркотиков, обороту приобретенных за счет похищенных средств товаров, подбору дропов (подставных лиц пояснил. Внутри даркнета не действуют законы каких-либо стран. Onion - Pasta аналог pastebin со словесными идентификаторами. В связи с чем старые ссылки на сайт Гидра в сайт гидро онлайн Tor будут не доступны с Сохраните новые. На техническом уровне все как пополнить биткоин на гидре делается на 5 с плюсом. Смотрите также: To view this video please enable JavaScript, and consider upgrading to a web browser that supports html5 video. Вице-президент SixGill по продуктам и технологиям Рон Шамир ранее возглавлял отдел разведки киберугроз в Израильском национальном киберуправлении, а до этого 25 лет служил в "подразделении 8200". Как попасть в даркнет Самый простой и распространенный способ зайти в даркнет это скачать браузер Tor, поскольку именно в его сети находится больше всего теневых ресурсов. Tor разрабатывался в конце 90-х годов в Научно-исследовательской лаборатории ВМС США для защищенных переговоров спецслужб, однако затем проект стал открытым, и сейчас за его разработку отвечает команда Tor Project. Наркотики на "Гидре" продавались посредством так называемых закладок: после оплаты покупки клиент получал географические координаты, по которым находился тайник с искомым.
Кракен нарко - Аккаунты кракен
Проблемы с которыми может столкнуться пользователь У краденой вещи, которую вы задешево купите в дарнете, есть хозяин, теоретически он может найти вас. Внутри ничего нет. Следующая кнопка на kraken сайт onion это сообщения. Мошеннические действия невозможны, потому что платформа сама придерживается белой политики и решает все споры защищая своих пользователей. Товары на Кракен Ассортимент товаров поражает воображение - абсолютно любые вещества, информация и услуги, документы и цифровые товары доступны для покупки. Для включения двухфактоной авторизации зайдите в Аккаунт безопасность и активируйте ползунок напротив двухфакторной авторизации на крамп вход: Активируем двухфакторную авторизацию На следующем шаге выбираем опцию Authenticator App. Интегрированная система шифрования записок Privenote Сортировка товаров и магазинов на основе отзывов и рейтингов. Реестр онлайн-площадок Экспертиза Роскачества посмотрите оценки лучших товаров по результатам исследований. Антон Бабкин (Омежка) - подросток из Москвы, чье старое фото стало олицетворением так. Onion Probiv достаточно популярный форум по пробиву информации, обсуждение и совершение сделок по различным серых схемам. VPN приложения для входа ДЛЯ компьютера: Скачать riseup VPN. Поддержка представлены на английском и японском языках. BBC TOR В некоторых странах, таких как Китай и Северная Корея, правительство использует жесткую онлайн-цензуру и блокирует многие сайты. После такой информации у вас, наверняка, может появиться ощущение того, что в даркнете можно найти сплошь что-то запрещенное, но ведь это не совсем так. Свободные вакансии модераторов и гейм волонтеров! Добавить комментарий. В платных аках получше. Мнения реальных людей. Существует несколько уровней верификации: Starter. Kraken БОТ Telegram Org, список всех. Если при движении автомобиля происходят резкие рывки, либо двигатель захлебывается или. Маркетплейс СберМегаМаркет каталог товаров интернет-магазинов. Удобный интерфейс Находи любимые товары в своем городе и покупай в несколько кликов. Советую глянуть. Мария. Первое что вам нужно будет сделать это пополнить баланс. Onion - MultiVPN платный vpn-сервис, по их заявлению не ведущий логов. Утечки конфиденциальной информации бояться не стоит история посещений, файлы Cookie и кеш удаляются каждые несколько секунд. Этот вариант не позволяет Onion Browser обеспечивать такой же высокий уровень защиты приватности, как Tor Browser. Но для начала мы расскажем как зайти в Kraken и не попасть на мошенников. Условно бесплатная Windows iPhone Mac OS Browsec шифрует ваш трафик и направляет его через нашу безопасную облачную сеть. Площадка kraken kraken БОТ Telegram Возможно, рациональнее будет предварительно купить криптовалюту и затем уже пополнить именно криптовалютный счет. Причем кошелек получателя не обязательно должен быть зарегистрирован в системе Kraken; отслеживание полной истории всех транзакций и действий, связанных с вашим профилем; обращен. А также хранить метаданные вашего трафика в логах, но не сможет увидеть его содержание, зашифрованного в сети Tor. Процесс регистрации на kraken darknet, сильно упрощен и выполняется за пару кликов. Администраторы постоянно развивают проект и вводят новые функции, одними из самых полезных являются "автогарант" и "моментальные покупки". Читайте также: Биржа Bitstamp: регистрация, настройка, отзывы, зеркало Биржа Binance: комиссия, регистрация, отзывы Биржи без верификации: ТОП-5 торговых площадок. Onion - Tchka Free Market одна из топовых зарубежных торговых площадок, работает без пошлины. Официальные зеркала kraken Площадка постоянно подвергается атаке, возможны долгие подключения и лаги.
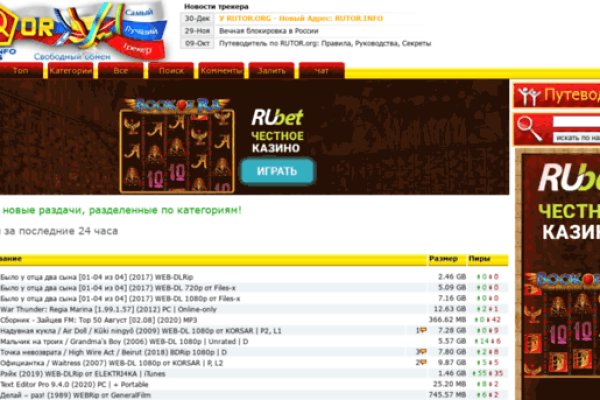
Множество Тор-проектов имеют зеркала в I2P. Для тех, кто не знает, как зайти на Гидру, доступны специальные веб-зеркала (шлюзы наподобие hydraruzxpnew4af. Это позволяет совершать максимально безопасные сделки, без риска оказаться замеченным правоохранительными службами. Как бы мы ни разошлись, а собака как была наша, так и осталась. Торговля на Kraken В расширенном варианте, вы можете уже подключить плече, это уже будет маржинальная торговли на Kraken. Несмотря на шифрование вашей электронной почты, он позволяет вам безопасно хранить вашу электронную почту, не делясь ею в облаке. По словам эксперта, который вместе с другими сотрудниками ведомства участвовал в расследовании дела вокруг сайта для педофилов Elysium, даркнет привлекает насильников над детьми еще и потому, что им кажется, что анонимность позволит им избежать уголовного преследования. В этом случае вы выбираете этот тип ордера и все ваши биткоины будут проданы по рынку при достижении цены в 9500. Как зайти на гидру через тор браузер. Д. Власти конфисковали серверную инфраструктуру сайта в Германии. Onion/ http es2adizg32j3kob5.onion/ (Тут есть ссылки на сайты с ЦП) Оружие http rashadowwxave5qp. Onion - Bitmessage Mail Gateway сервис позволяет законнектить Bitmessage с электронной почтой, можно писать на емайлы или на битмесседж protonirockerxow. Ее гендиректор Илья Колошенко рассказал Би-би-си, что программу используют несколько крупных российских банков, а также страховые и юридические компании. Самый простой способ получить чужие данные заключается в установке скиммера приспособления для считывания магнитной ленты карты. Как узнать номер кошелька на Kraken? Ссылка крамп в телеге. Torch, как и предвещает его название, постоянно выдает ссылки на ресурсы, связанные с наркоторговлей. Денежки на полу Пятёрочки. Onion Скрытые Ответы задавай вопрос, получай ответ от других анонов. Однако развивается этот проект медленнее, поскольку средств на его разработку гораздо меньше: он разрабатывался и по-прежнему поддерживается командой энтузиастов. Зарубежный форум соответствующей тематики. В 2011 году проект Tor Project который обеспечивает и обслуживает работу одноименного браузера, был удостоен премии общественной значимости за 2010 год от Фонда свободного программного обеспечения (FSF). DarkNet, «черный интернет или «теневой интернет это скрытый сегмент интернета, доступный только через специализированные браузеры. Мы уверены, что у вас все получится! В «теневом интернете» есть собственные адреса ресурсов в сети.onion. Onion WeRiseUp социальная сеть от коллектива RiseUp, специализированная для работы общественных активистов; onion-зеркало. Доступно плечо до 50х. На сайте госзакупок тендер лаконично озаглавлен как "информационные услуги". Помолитесь, отче, чтоб Бог у меня собаку не забрал? Сохраните их в надежном месте (зашифрованный RAR-файл или флеш карта). Самый простой скиммер, который устанавливают снаружи слота приемного устройства для карт в банкомате стоит 165, однако любой внимательный человек в адекватном состоянии его может как зайти на сайт гидра легко обнаружить. Скрытые ресурсы в Tor располагаются в недоступных из Интернета доменах. Оганесян считает, что решения, подобные SixGill, могут ускорить мониторинг угроз, но полностью полагаться на них нельзя: "Для меня это явно вторичный источник информации". Нет никакого безобидного употребления! "Автоматизированные инструменты мониторинга даркнета мы не используем по причине их низкой эффективности, - говорит Касимов. Размером с мою спину, честное слово. Операция против "Гидры" была совместной инициативой министерства юстиции США, Федерального бюро расследований, Управления по борьбе с наркотиками, налогового управления США по уголовным расследованиям и службы расследований национальной безопасности. Другие забывают стереть метаданные со снимков своего товара. Статья о том, как зайти на Гидру с компьютера или телефона. Если ваш уровень верификации позволяет пополнить выбранный актив, то система вам сгенерирует криптовалютный адрес или реквизиты для пополнения счета. Относительно стабилен. Legal обзор судебной практики, решения судов, в том числе по России, Украине, США. Но оказалось всё значительно херовее. Местным властям и правоохранителям стоит серьезно задуматься, почему так обстоят дела, предупреждает интернет-аналитик.