Дарк нет кракен
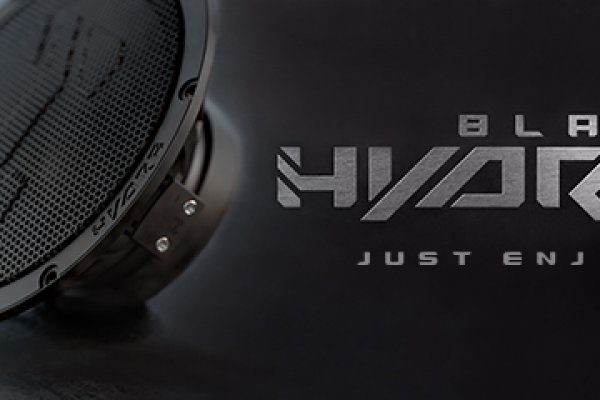
Децентрализованный и зашифрованный интернет Даркнет - это анонимная и неконтролируемая часть интернета, недоступная обычным даркнет поисковым системам типа Google. Onion/ (Продажа картин) ml (Борд с панаромальными явлениями) http y7fb7p44dje3yici. Информация проходит через 3 случайно выбранных узла сети. Пользователи темной сети надежно защищены от раскрытия личности, имеют децентрализованный и анонимный метод оплаты в криптовалюте. Onion/ Биткоин http blockchainbdgpzk. Onion - Darknet Heroes League еще одна зарубежная торговая площадка, современный сайтик, отзывов не нашел, пробуйте сами. Стоко класных отзывов. С недавних пор в России и других странах СНГ стали запрещать прокси-сервера, с помощью которых работает Tor браузер. Статья о том, как зайти маркетплейс на Гидру с компьютера или телефона. Сети, которым можно доверять обязательно берут плату за свои услуги. Надоели серые будни? Редакция CNews не несет ответственности за его содержание. Для регистрации нужен ключ PGP, он же поможет оставить послание без адресата. Размером с мою спину, честное слово. Браслетик тот через пару дней уже вернулся к владелице - по объявлению в местной группе и по описанию. Шаг 5: Добавьте API ключ в Good Crypto Вариант 1: QR код мобильное приложение Good Crypto Самый безопасный и удобный способ передать API ключ с Кракена к нам это отсканировать QR-код приложением Good Crypto с телефона. Новый адрес гидры hydraclubbioknikokex7njw вход по ссылке. ООО ИА «Банки. Расширенные типы ордеров, варианты отображения графиков и многое другое. Onion-ресурсов от Tor Project. Информация по уровням верифкации маркетплейс в табличном виде. В теневом интернете свободно продается оружие, а также нелегальные услуги самого разного рода: например, там можно взять в аренду сетевых ботов или заказать кибератаку у профессиональных хакеров. Текущий курс BTC можно посмотреть на нашем сайте. Кардинг / Хаккинг Кардинг / Хаккинг wwhclublci77vnbi. Децентрализованный и зашифрованный интернет Даркнет - это анонимная и неконтролируемая часть интернета, недоступная обычным поисковым системам типа Google. Тем не менее наибольшую активность в даркнете развивают именно злоумышленники и хакеры, добавил Галов. В канун Нового года сына петербурженки Лады Уваровой пригласили гидра упала на его первую работу. Весь в чехле и в камерах. 14 июн. Нужно скопировать ключ активации и возвратиться на страницу биржи криптовалют. Например, вы торгуете на Кракене два года, значит, приложение отобразит как ваш портфель менялся за это время. Что такое Гидра. Амфетамин: premium Челябинск (Челябинская область) Для входа на kraken перейти НА сайт kraken Для входа на kraken перейти НА сайт kraken Made on Tilda.
Дарк нет кракен - Кракен kr2web in маркетплейс
е форму получения товара только после того как удостоверитесь в качестве. На тот момент ramp насчитывал 14 000 активных пользователей. Английский язык. И Tor появляется. Onion/ - форум FreeHacks Ссылка удалена по притензии роскомнадзора Ссылка удалена по притензии роскомнадзора Сообщения, Анонимные Ящики (коммуникации) Сообщения, анонимные ящики (коммуникации) bah37war75xzkpla. Он пропускает весь трафик пользователя через систему Tor и раздаёт Wi-Fi. Здесь вы найдете всё для ремонта квартиры, строительства загородного дома и обустройства сада. Подробнее можно прочитать на самом сайте. Сеть для начинающих. Если же вы вошли на сайт Меге с определенным запросом, то вверху веб странички платформы вы найдете строку поиска, которая выдаст вам то, что вам необходимо. Onion - Anoninbox платный и качественный e-mail сервис, есть возможность писать в onion и клирнет ящики ваших собеседников scryptmaildniwm6.onion - ScryptMail есть встроенная система PGP. Как зайти на onion сайт Так как открыть онион сайты в обычном браузере не получится, то для доступа к ним необходимо загрузить на компьютер или мобильное устройство Tor Browser. Вас приветствует обновленная и перспективная площадка всея русского даркнета. Onion - Fresh Onions, робот-проверяльщик и собиратель.onion-сайтов. Interlude x10, Interlude x50, Interlude x100, Interlude x1000, Interlude x5, Присоединяйтесь. Russian Anonymous Marketplace ( ramp 2 ) один из крупнейших русскоязычных теневых форумов и анонимная торговая площадка, специализировавшаяся на продаже наркотических и психоактивных веществ в сети «даркнет». Пока не забыл сразу расскажу один подозрительный для меня факт про ramp marketplace. 1566868 Tor поисковик, поиск в сети Tor, как найти нужный.onion сайт? Однако скорость его работы заставляет вспомнить о временах модемов, подключающихся к сети через телефонную линию. Onion - Alphabay Market зарубежная площадка по продаже, оружия, фальшивых денег и документов, акков от порносайтов. Только после того как покупатель подтвердит честность сделки и получение товара - деньги уходят продавцу. По мне же, так удобнее изменить путь и распаковать его в специально подготовленную для этого папку. Объясняет эксперт Архивная копия от на Wayback Machine. Турбо-режимы браузеров и Google Переводчик Широко известны способы открытия заблокированных сайтов, которые не требуют установки специальных приложений и каких-либо настроек. Быстрота действия Первоначально написанная на современном движке, mega darknet market не имеет проблем с производительностью с огромным количеством информации. Онлайн системы платежей: Не работают! Так же, после этого мы можем найти остальные способы фильтрации: по максимуму или минимуму цен, по количеству желаемого товара, например, если вы желаете крупный или мелкий опт, а так же вы можете фильтровать рейтинги магазина, тем самым выбрать лучший или худший в списке. За активность на форуме начисляют кредиты, которые можно поменять на биткоины. Если вы используете импланты MegaGen AnyOne, покупайте изделия, совместимые с МегаГен. Книжная купить по выгодной цене на АлиЭкпресс. Внимание! Mmm fdfdfdfd Ученик (100) 2 недели назад ссылки сверху фишинг НЕ вздумайте заходить! Всегда смотрите на адресную строку браузера, так вы сделаете все правильно! Данные приводились Flashpoint и Chainalysis. Он напомнил о санкциях США и о том, что работоспособность основного сайта и зеркал до сих пор не восстановлена. Onion/ - Форум дубликатов зеркало форума 24xbtc424rgg5zah. Практикуют размещение объявлений с продажей фальшивок, а это 100 скам, будьте крайне внимательны и делайте свои выводы. Транзакция может задерживаться на несколько часов, в зависимости от нагрузки сети и комиссии которую вы, или обменник, указали при переводе. И где взять ссылки на них. Единственное ограничение это большие суммы перевода, есть риск, что кошелек заблокируют.
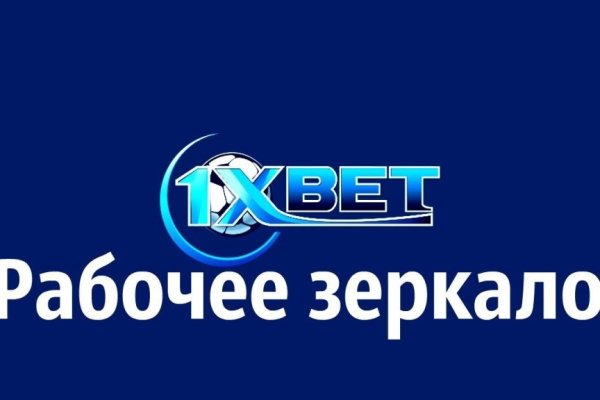
Оniоn p Используйте анонимайзер Тор для онион ссылок, чтобы зайти в обычном браузере: Теневой проект по продаже нелегальной продукции и услуг стартовал задолго до закрытия аналогичного сайта Hydra. Широкий ассортимент бонгов, вапорайзеров, аксессуаров для. Првиетствую, представляем Вашему вниманию Solaris - Форум и децентрализованный каталог моментальных покупок товаров теневой сферы. Настройка Browser на для посещения.onion и заблокированных ресурсов. Мега, Белая Дача: адреса со входами на карте, отзывы, фото, номера телефонов, время. Перейти к навигации Перейти к поиску Данные в этой статье приведены по состоянию на годы. Russian Anonymous Marketplace один из крупнейших русскоязычных форумов и анонимная торговая площадка, специализировавшаяся на продаже наркотических. Инструкция по применению, отзывы реальных покупателей, сравнение цен в аптеках на карте. По какому находится ТЦ? Телеграмм канал «Закладочная». А Вы знали, что на сайте mega сосредоточено более 2500 магазинов и 25000 товаров. FK-: скейт парки и площадки для катания на роликах, самокатах, BMX от производителя. Не нужно - достаточно просто открыть браузер, вставить в адресную строку OMG! Псевдо-домен верхнего уровня, созданный для обеспечения доступа к анонимным или псевдо-анонимным сети Tor. Логин или. Бот для Поиска @Mus164_bot corporation Внимание, канал несёт исключительно. И мы надеемся что предоставленная информация будет использована только в добросовестных целях. Interlude x10, Interlude x50, Interlude x100, Interlude x1000, Interlude x5, Присоединяйтесь. Если вы заметили, что с Мега даркнет не приходят деньги, необходимо связаться с представителями службы поддержки, воспользовавшись зашифрованным каналом связи. Обязательный отзыв покупателя после совершения сделки. Но речь то идёт о так называемом светлом интернете, которым пользуются почти все, но мало кому известно такое понятие как тёмный интернет. Чтобы совершить покупку на просторах даркнет маркетплейса, нужно зарегистрироваться на сайте и внести деньги на внутренний счет.