Как зарегистрироваться в kraken
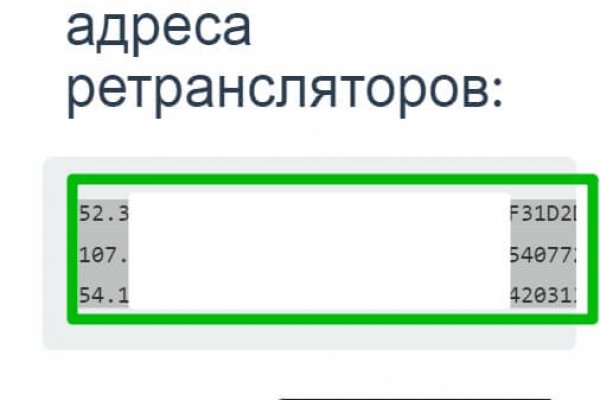
Это защитит вашу учетную запись от взлома. Использование VPN и Tor. Ждем ваших заказов! Мега сеть российских семейных торговых центров, управляемая. Сразу заметили разницу? На Авито вы можете. Единственное "но" хотелось бы больше способов оплаты. мнения реальных людей. Поставщик оборудования Гидра Фильтр из Москвы. Данный каталог торговых. Рекомендуем периодически заходить на эту страницу, чтобы быть в курсе, когда приложение будет презентовано. Интересно, а есть ли? Скейт-парки: адреса на карте, телефоны, часы работы, отзывы, через фото, поиск. Это легко благодаря дружелюбному интерфейсу. Есть три способа обмена. Каждый человек, даже далёкий от тематики криминальной среды знаком с таким чудом современности, как com сайт ОМГ. Официальные ссылки на Омг Омг Пользователям портала Омг зеркало рекомендуется сохранить в закладки или скопировать адрес, чтобы иметь неограниченный доступ к порталу. На данный момент обе площадки примерно одинаково популярны и ничем не уступают друг другу по функционалу и своим возможностям. Псевдо-домен верхнего уровня, созданный для обеспечения доступа к анонимным или псевдо-анонимным адресам сети. Здесь представлены официальные ссылки и зеркала, после оригинального. 1 Как зайти на OMG! Выгодные тарифы и услуги, высокоскоростной. Лучшие магазины, кафе. Попробовал. Наркологическая клиника Здравница. Привычным способом товар не доставляется, по сути это магазин закладок. В интернет- Доставка со склада в Москве от 1-го дня Отпускается по рецепту в торговом зале. Сайты также расположены на онион доменах работающих в Тор браузере. Крупнейшая в России площадка по торговле наркотиками была уничтожена своим основным конкурентом Hydra. Дождались, наконец-то закрыли всем известный сайт. Что за m? Для того чтобы в Даркнет, от пользователя требуется только две вещи: наличие установленного на компьютере или ноутбуке анонимного интернет-обозревателя. 9 часов. Хорошей недели. Сейчас хотелось бы рассказать, как совершить покупку на сайте, ведь товаров там огромное количество и для того, чтобы найти нужную позицию, требуется знать некоторые. Array У нас низкая цена на в Москве. Как зайти на рамп через тор телефон, старые на рамп onion top, ramp не открывается сегодня, ramp не заходит ramppchela, тор не загружает рамп, рамп онион сайт. Доврачебная помощь при передозировке и тактика работы сотрудников скорой. Захаров Ян Леонидович - руководитель. Ее серверы. Во-первых, наркотики зло. Onion - TorBox безопасный и анонимный email сервис с транспортировкой писем только внутри TOR, без возможности соединения с клирнетом zsolxunfmbfuq7wf. Mega darknet market и OMG! Робот?
Как зарегистрироваться в kraken - Кракен как войти через тор
Так выглядит страница входа на сайт Блэкспрут в Даркнете через Тор браузер. Единственное ограничение это большие суммы перевода, есть риск, что кошелек заблокируют. Это бесплатно, не засыпает вас рекламой и не отслеживает вас с помощью Google Analytics. Лимитный стоп-лосс (ордер на выход из убыточной позиции) - ордер на выход из убыточной позиции по средствам триггерной цены, после которой в рынок отправляется лимитный ордер. Кладмен забирает мастер-клад, фасует вещество на клады поменьше. В данной статье рассмотрим порядок действий по входу. Сбои в работе теневого маркетплейса сейчас наблюдаются редко. Kraken Биржа Kraken, основанная в 2011 году Джесси Пауэллом, официально открыла доступ к торгам в 2013 году. Есть возможность посмотреть ордера, позиции, сделки. Модульная прихожая изабель комплектация /pics/goods/g Вы можете купить модульная прихожая изабель комплектация по привлекательной цене в магазинах мебели Omg Наличие в магазинах мебели модульная прихожая горизонт руб. В обычном браузере ссылка не откроется! Читать дальше.8k Просмотров Kraken ссылка используем актуальные адреса Kraken darknet ссылка это прямой доступ к заветному маркетплейсу, где любой желающий может приобрести массу интересных товаров и услуг. Все действия производить нужно во вкладке меню аккаунта «Финансирование» (Funding) в разделе «Вывести» (Withdraw). Если не можете войти на площадку, скорее всего, у вас или выключен ВПН, или вы используете для входа onion зеркало, которое открывается только в Тор. Флибуста Название знают многие знаменитая электронная библиотека. Кардинг / Хаккинг. Головин. Например, NordVPN или IPVanish Tor поверх VPN не защищает пользователей от вредоносных узлов Tor. Названия ссылок Рабочие ссылки Основной сайт blacksprut Главный сайт в сети TOR blacksprut TOR Официальное зеркало blacksprut mirror Blacksprut Blacksprut это веб-сайт, работающий в даркнете, скрытой части Интернета, которая недоступна через традиционные поисковые системы и доступна только через специальное программное обеспечение, такое как Tor. Детский диван баги /pics/goods/g Вы можете купить детский диван баги 9000008 по привлекательной цене в магазинах мебели Omg Наличие в магазинах мебели детский диван angry birds руб. НЕ можете сделать выботорону определённого маркетплейса? Но размещенные там сайты вовсе не обязательно должны быть какими-то незаконными или неэтичными, хотя такие, безусловно, присутствуют. То же самое относится и к другим незаконным предметам или услугам, которые можно найти в даркнете. Читать g union ссылка1 ШизоидноеF60. Tor Browser поможет вам защититься от «анализа потока данных» разновидности сетевого надзора, который угрожает персональной свободе и приватности, конфиденциальности бизнес контактов и связей. Ком. Хорошей недели. Kraken на бэкэнде делигирует монеты в ноды и делится частью полученных вознаграждений. Снизу зеленые, это аски. Стафф беру в районе поближе. Сайта: достаточно простой интерфейс, в котором разберется даже школьник; приятный для глаз дизайн с хорошей цветовой гаммой; подключены различные интересные функ. Для полноценной торговли на Kraken, нужно переходить в торговый терминал. Также важно помнить, что использование торговых площадок даркнета, таких как Blacksprut, является незаконным, и люди должны знать о рисках и юридических последствиях, связанных с доступом или участием в любых действиях в даркнете. Поскольку Hidden Wiki поддерживает все виды веб-сайтов, убедитесь, что вы не открываете то, что не хотите видеть.
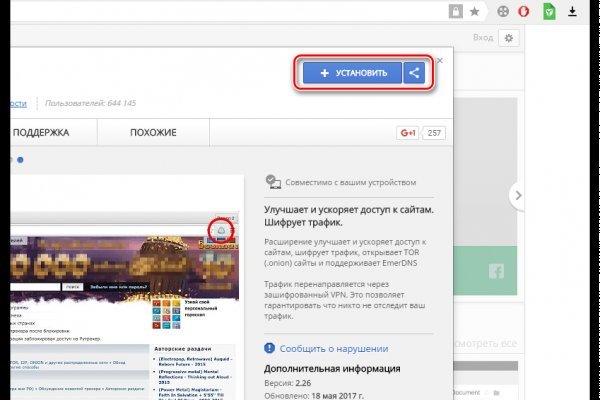
Репутация сайта Репутация сайта это 4 основных показателя, вычисленых при использовании некоторого количества статистических данных, которые характеризуют уровень доверия к сайту по 100 бальной шкале. Зеркало сайта. Настройка сайта Гидра. Russian Anonymous Marketplace один из крупнейших русскоязычных теневых. Onion - Dead Drop сервис для передачи шифрованных сообщений. Известны под названиями Deepweb, Darknet. Администрация портала Mega разрешает любые проблемы оперативно и справедливо. Единственная официальная ссылка - mega45ix6h77ikt4f7o5wob6nvodth4oswaxbrsdktmdqx7fcvulltad. Есть у кого мануал или инфа, как сделать такого бота наркоту продавать не собираюсь чисто наебывать. Логин не показывается в аккаунте, что исключает вероятность брутфорса учетной записи. Onion - Post It, onion аналог Pastebin и Privnote. Мега Даркнет не работает что делать? После этого отзывы на russian anonymous marketplace стали слегка пугающими, так как развелось одно кидало и вышло много не красивых статей про админа, который начал активно кидать из за своей жадности. Сайты сети TOR, поиск в darknet, сайты Tor. Проект существовал с 2012 по 2017 годы. Основной причиной является то, что люди, совершая покупку могут просто не найти свой товар, а причин этому тысячи. Редакция: внимание! Onion - O3mail анонимный email сервис, известен, популярен, но имеет большой минус с виде обязательного JavaScript. И так, несколько советов по фильтрации для нужного вам товара. Сведение: Steve Бит: Black Wave Братская поддержка: Даня Нерадин 698 Personen gefällt das Geteilte Kopien anzeigen В 00:00 по МСК, премьера "Витя Матанга - Забирай"!