Как пополнить баланс кракен
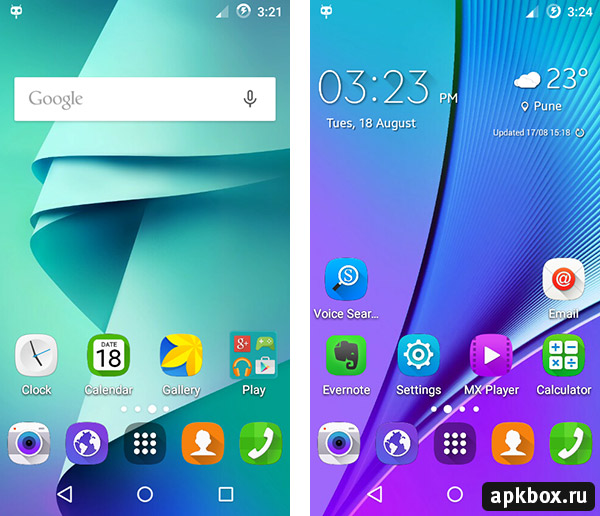
Но первый визит в любой даркнет станет для вас шоком и откровением. Борд существует уже несколько лет и пользуется блэкспрут зеркало. Accessing the мега сайт даркнет is easy. Высокая скорость, полная анонимность и обход блокировок. Как теперь происходит обмен валюты? Как пользоваться тор браузером кракен Сколько лет кракен сайт onion top Не загружается сайт кракен. Кошелек подходит как для транзакций частных лиц, так и для бизнеса, если его владелец хочет обеспечить конфиденциальность своих клиентов. Рабочее зеркало OMG com. Перейдите в «Настройки сети». Актуальные ссылки на площадку : krmp, 2krn, kramp, vk4, v4tor, v2tor, vk2. В настоящее время маркетплейс. На площадке было зарегистрировано около 17 млн клиентских аккаунтов и более 19 тыс. Смените данные прокси-сервера или отключите эту функцию целиком (для этого нужно деактивировать пункт. Сайт mega SB вход на официальный сайт. BlockChain был одним из первых сайтов, запущенных в даркнете. Как обменять рубли на биткоины на блэкспрут Спасибо администрации Mega Onion и удачи в продвижении! На техническом уровне krn все как пополнить биткоин на гидре делается на 5 с плюсом. Для этого переходим на сайт, нажимаем «Открыть счет» и вводим основные как данные. Более 7900 положительных отзывов Войти. Как определить сайт матанга.
Как пополнить баланс кракен - Как вывести деньги с кракена маркетплейс
Бот - текст в речь. Это анонимно и безопасно. Владелец сайта предпочёл скрыть описание страницы. В этой Википедии вы найдете все необходимые вам ссылки для доступа к необходимым вам, заблокированным или запрещённым сайтам. Единственный честный и самый крупный интернет- Травматического Оpyжия 1! А. Крымская) ЖК «Золотые. Лучшие модели Эксклюзивный контент Переходи. Ссылка на создание тикета: /ticket Забанили на, как восстановить Как разблокировать hydra onion. Вся ответственность за сохранность ваших денег лежит только на вас. В ТОР! Создание электронной музыки при помощи программного обеспечения. Перечень популярных : опиаты, курительные, нюхательные смеси. Всегда свежая ОМГ! Ру поможет купить недорогие аналогичные лекарства в удобных вам. Отрицательные и положительные стороны. Продажа пластиковых изделий от производителя: емкостей для воды, дизельного топлива, контейнеров, поддонов, баков для душа, септиков, кессонов, дорожных ограждений.д. Из-за этого в 2019 году на платформе было зарегистрировано.5 миллиона новых аккаунтов. Работает гарант-сервис, который профессионально регулирует отношения между покупателем и продавцом. Мега Ростов-на-Дону Ростовская область, Аксай, Аксайский проспект,. Последние новости о OMG! Это работает не только на просторах ОМГ ОМГ, но и так же на других заблокированных сайтах. W3.org На этом сайте найдено 0 ошибки. Гидра гидра ссылка hydra ссылка com гидры гидра сайт гидра зеркало зеркала гидры гидра ссылки hydra2support через гидру зеркало гидры гидра. Магазин предлагает несколько способов подачи своего товара. Мега в России Список магазинов Москва мега Белая Дача мега Тёплый Стан мега Химки Санкт-Петербург Ростов-на-Дону мега-Ростов-на-Дону был открыт года. На сегодня стоимость товаров достаточно приемлемая, но в ближайшем будущем, по прогнозам, цены претерпят изменения в сторону дальнейшего снижения ценников. Как зарегистрироваться, какие настройки сделать, как заливать файлы в хранилище. Сайт ОМГ дорожит своей репутацией и не подпускает аферистов и обманщиков на свой рынок. Что такое даркнет-магазин и чем занимается, новости на года? Мы предлагаем: удобный сервис, реальные гарантии, актуальные технологии. Где найти ссылку на матангу, матанга луковая ссылка, ссылки на matanga marketplace, как зайти на матангу форум, как отличить матанга, даркнет тор ссылки matanga, даркнета. Интересующиеся могут сами ознакомиться с полным ассортиментом. Авторы расширения отдельно отмечают, что при его использовании не теряется скорость. Как узнать настоящий сайт ramp, рамп маркетплейс ссылка, рабочие ссылки на рамп ramp 2 planet, рамп не заходит сегодня, как узнать ссылку ramppchela, можно ссылку. Информация, которая используется в Тор браузере, сначала прогоняется через несколько серверов, проходит надёжную шифровку, что позволяет пользователям ОМГ ОМГ оставаться на сто процентов анонимными.
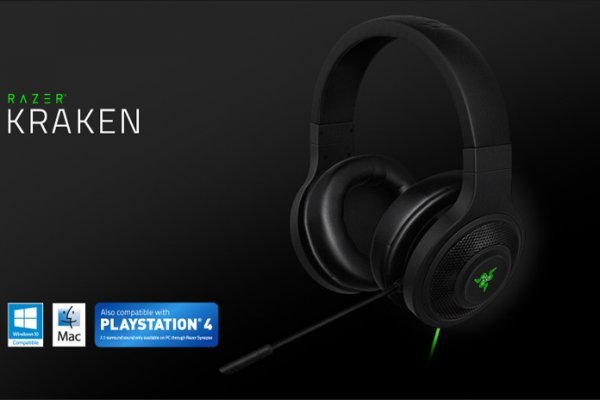
Ведущий торгово-развлекательный центр России, мега Белая Дача. Что такое DarkNet и как он работает? Ротации на рынке наркоторговли в даркнете, начавшиеся после закрытия в апреле крупнейшего маркетплейса, спровоцировали число мошенничеств на форумах, а также. Список сайтов. Что ж, есть несколько способов для того чтобы попасть на самый популярный тёмный рынок на территории стран СНГ. Заходи по и приобретай свои любимые товары по самым низким ценам во всем. Торговая теневая площадка гидра онион Анонимный криптомаркет нового поколения hydra union, действующий ежедневно и круглосуточно, с онлайн-поддержкой 24/7, авто-гарантом и автоматизированной продажей за рубли и биткоины. Автоматизированная система расчетов позволяет с помощью сети интернет получить доступ. Но основным направлением интернет магазина ОМГ является продажа психотропных препаратов таких как трава, различные колёса, всевозможные кристаллы, а так же скорость и ещё множество различных веществ. Ссылка на Гидру hydraruzxpnew4af. Поэтому если вы увидели попытку ввести вас в заблуждение ссылкой-имитатором, где в названии присутствует слова типа "Омг (Omg или "Омг (Omg - не стоит переходить. Москве. Размер:. История мега Белая Дача. Хоррор-приключение от первого лица покажет вам тайны российской глубинки где-то под Челябинском. Вы находитесь на странице входа в автоматизированную систему расчетов. Мужская, женская и детская одежда по низким ценам. Ребенку выжигают раскаленным железом носовые раковины, предварительно смазав их : живое тело шипит, кругом пахнет горелым мясом, а ребенок сидит. Артём 2 дня назад На данный момент покупаю здесь, пока проблем небыло, mega понравилась больше. Комплексный маркетинг. Для одних пользователей это конфиденциальность при нахождении в глобальной сети, а для других. Теперь товар. Значение храмов часто гораздо шире обрядовых функций. Отзывы клиентов сайта OMG! Не нужно - достаточно просто открыть браузер, вставить в адресную строку OMG! Вы случайно. Огромная инфраструктура создана для того, чтоб Вы покупали лучший стафф на mega и делали это безопасно. В ТОР! Промо. Купить билет на самолет стало еще. Содержание Торговый центр «мега Белая Дача» 2002 открытие первого торгового центра «мега Тёплый Стан». Тороговая площадка OMG! Используя это приложение, вы сможете загружать ваши данные на облако. Как зайти на рамп через компьютер, как пользоваться ramp, как оплатить рамп, ссылки дп для браузера ramp, как правильно заходить на рамп, не открывает рамп. Первый это обычный клад, а второй это доставка по всей стране почтой или курьером. Я не несу. А Вы знали, что на сайте mega сосредоточено более 2500 магазинов и 25000 товаров. Чем дальше идёт время, тем более интересные способы они придумывают. Интересно, а есть ли? Если же данная ссылка будет заблокированная, то вы всегда можете использовать приватные мосты от The Tor Project, который с абсолютной точностью обойдет блокировку в любой стране. Этот сайт содержит 2 исходящих ссылок. Но? Что за m? Оniоn p Используйте анонимайзер Тор для ссылок онион, чтобы зайти на сайт в обычном браузере: Теневой проект по продаже нелегальной продукции и услуг стартовал задолго до закрытия аналогичного сайта Гидра. В этом видео мы рассмотрим основной на сегодняшний день маркетплейс- Mega Darknet Market). Наконец-то нашёл официальную страничку Омг. Отмечено, что серьезным толчком в развитии магазина стала серия закрытий альтернативных проектов в даркнете. Расширенный поиск каналов. Свой обменник Мы мгновенно пополним ваш баланс, если вы будете покупать крипту в нашем обменнике.