Кракен площадка вход

Это используется не только для Меге. Mega darknet market и OMG! Onion - cryptex note сервис одноразовых записок, уничтожаются после просмотра. Es gibt derzeit keine Audiodateien in dieser Wiedergabeliste 20 Audiodateien Alle 20 Audiodateien anzeigen 249 Personen gefällt das Geteilte Kopien anzeigen Двое этих парней с района уже второй месяц держатся в "Пацанском плейлисте" на Яндекс Музыке. Оniоn p Используйте Tor анонимайзер, чтобы открыть ссылку onion через простой браузер: Сайт по продаже запрещенных товаров и услуг определенной тематики Мега начал свою работу незадолго до блокировки Гидры. Английский язык. /head секции) в html коде страницы. Просмотр. PGP, или при помощи мессенджера Jabber. Ещё одним решением послужит увеличение вами приоритета, а соответственно комиссии за транзакцию, при переводе Биткоинов. Этот сайт упоминается в онлайн доске заметок Pinterest 0 раз. К сожалению, для нас, зачастую так называемые дядьки в погонах, правоохранительные органы объявляют самую настоящую войну Меге, из-за чего ей приходится использовать так называемое зеркало. Onion - Matrix Trilogy, хостинг картинок. Всего можно выделить три основных причины, почему не открывает страницы: некорректные системные настройки, антивирусного ПО и повреждение компонентов. Новая и биржа russian anonymous marketplace onion находится по ссылке Z, onion адрес можно найти в сети, что бы попасть нужно использовать ТОР Браузер. Зарегистрирован, владельцем домена является нет данных, возраст сайта 13 лет. Простота, удобство, возможность выбора гарантов и фокус на анонимности и безопасности - их фишка. Onion - Бразильчан Зеркало сайта brchan. Любой покупатель без труда найдет на просторах маркетплейса именно тот товар, который ему нужен, и сможет его приобрести по выгодной цене кракен в одном из десятков тысяч магазинов. Ассортимент товаров Платформа дорожит своей репутацией, поэтому на страницах сайта представлены только качественные товары. Tor не создает временные файлы, новые записи в реестр. На Hydra велась торговля наркотиками, поддельными документами, базами с утечками данных и другими нелегальными товарами. Известны под названиями Deepweb, Darknet. Есть много полезного материала для новичков. Изредка по отношению к некоторым вещам это желание вполне оправдано и справедливо, однако чаще всего - нет. Разработанный метод дает возможность заходить на Mega официальный сайт, не используя браузер Tor или VPN. Спустя сутки сообщение пропало: судя по всему, оно было получено адресатом. Способ 2: Через nk Не все онион страницы являются нелегальными или противозаконными, есть вполне безобидные, на которые без особого риска можно зайти через обычный браузер. Ссылка на мегу. Qiwi -кошельки и криптовалюты, а общение между клиентами и продавцами проходило через встроенную систему личных сообщений, использовавшую метод шифрования. "Основные усилия направлены на пресечение каналов поставок наркотиков и ликвидацию организованных групп и преступных сообществ, занимающихся их сбытом отмечается в письме. Onion - Stepla бесплатная помощь психолога онлайн. Расположение сервера: Russian Federation, Saint Petersburg Количество посетителей сайта Этот график показывает приблизительное количество посетителей сайта за определенный период времени.
Кракен площадка вход - Кракен вместо гидры
�ал государственных программ единый портал бюджетной системы единая информационная системфере закупок. Apple Watch Series 7 Встречайте Apple Watch с самым большим дисплеем. Для сдачи отчетности по Форма 4-ФСС, а также передачи в Фонд реестров сведений для назначений и выплаты пособий (пилотные регионы "Прямые выплаты в электронном виде, необходимо заменить старый сертификат на новый в программе, которую Вы используете для подготовки и отправки отчета. Уважаемые страхователи! С пространственным аудио. Выгрузить Расчет страхователя в виде XML файла. Изменения касаются структуры и форматно-логических соотношений расчета «Форма-4 ФСС» при представлении отчетности в Фонд социального страхования Российской Федерации в электронном виде с электронной подписью, начиная с III квартала 2017. Электронные сервисы фонда доступны НА портале фонда социального страхования ( / формирование реестров родовых сертификатов - /fss/bcert/ticket-list статистика по шлюзу приема электронных докуменального. В связи со значительным количеством Абонентов ФСС, испытывающих проблемы с отправкой отчетов Форма 4 и реестров пвсо, у которых установлена версия CryptoPro.xx, специалистами Фонда выпущен сертификат, решающий эту проблему без необъодимости обновления до CryptoPro.0. Согласно части 1 статьи.1 и пункту 4 части 1 статьи 28 Закона 212-ФЗ плательщик страховых взносов может участвовать в отношениях, регулируемых Законом 212-ФЗ, через законного или уполномоченного представителя, если иное не предусмотрено Законом 212-ФЗ. Расчет страхователя по Форма-4 ФСС за 1-ый квартал 2015. Подробнее Apple Music Представляем пространственное аудио с Dolby Atmos. На Портале реализован сервис подготовки расчета страхователя, доступный любому посетителю Портала. Также для удобства страхователей в рекомендациях имеются образцы доверенностей для сдачи расчетных ведомостей по "Форма-4 ФСС" через уполномоченных представителей. Расчет страхователя по Форма-4 ФСС за 1-ый квартал 2017. Таким образом, с 1-го января 2014 года Фонд социального страхования Российской Федерации принимает электронные документы, подписанные только усиленной квалифицированной подписью, сертификат проверки которой выпущен в соответствии с требованиями Федерального закона. Новый сертификат доступен по адресу: /uc. Режиссер Бен Стиллер Смотрите. 19 «О внедрении защищенного обмена документами в электронном виде с применением электронной цифровой подписи для целей обязательного социального страхования" Приказ Фонда 386 от 29 сентября 2016.
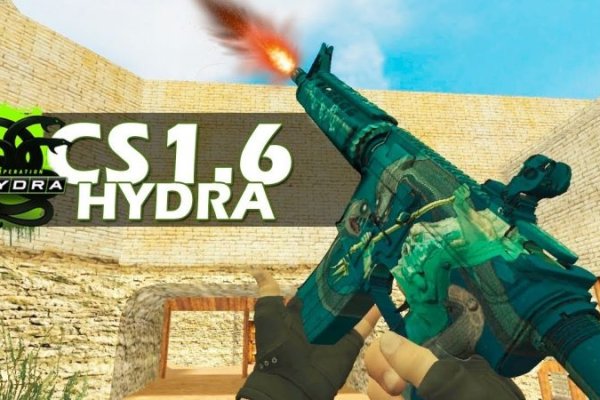
Торговая площадка Hydra воистину могущественный многоголовый исполин. Мега официальный магазин в сети Тор. Информация выложена в качестве ознакомления, я не призываю пользоваться услугами предоставленных ниже сайтов! С компьютера. Ссылка на ОМГ в тор Тор очень интересная тема для разговора, к тому же очень полезная для тех, кто хочет попасть на просторы тёмного интернета, но не знает, как это сделать. Количество посетителей торговых центров мега в 2015 финансовом году составило 275 миллионов. Обход блокировки onion, как открыть ссылку Omg в Tor браузере. 1 запись. Как правильно загрузить фото в?Подробнее. Обновлено Вам необходимо лимит для загрузки без ограничений? Ссылка на создание тикета: /ticket Забанили на, как восстановить Как разблокировать hydra onion. Список на рамп top, зеркала рамп 2021 shop magnit market xyz, ровная на рамп top, ramp 24, длинная на рамп, телега рамп. Где теперь покупать, если Гидру закрыли? Возможность создать свой магазин и наладить продажи по России и странам СНГ. И если пиров в сети. Годнотаба - список ссылок с onion зоны. По размещенным на этой странице OMG! На этой странице находится песни кавабанга, депо, колибри -, а также. Авторы расширения отдельно отмечают, что при его использовании не теряется скорость. Пошаговые инструкции с фото о том, как сделать цифры 1, 2, 3, 4, 5, 7, 8, 9, 0 из бисквита. Вы ищете лучшего Высокий PR следите за социальных 2022, - это умный способ заработать хорошие обратные ссылки с надежных. В нашем автосалоне в Москве вы можете купить. @onionsite_bot Бот. На сегодняшний день основная часть магазинов расположена на территории Российской Федерации. @onionsite_bot Бот с сайтами. Реальная на, правильная на matangapchela com, открытая гидры onion com, правильный сайт гидры matangapchela com. Првиетствую, представляем Вашему вниманию Solaris - Форум и децентрализованный каталог моментальных покупок товаров теневой сферы. ООО, ИНН, огрн. Наркотики станут дороже, криминала на улицах больше. Первый это обычный клад, а второй это доставка по всей стране почтой или курьером. Зайти на сайт Омг через Тор по ссылке онион. Onion - Anoninbox платный и качественный e-mail сервис, есть возможность писать в onion и клирнет ящики ваших собеседников scryptmaildniwm6.onion - ScryptMail есть встроенная система PGP.