Тор для кракена
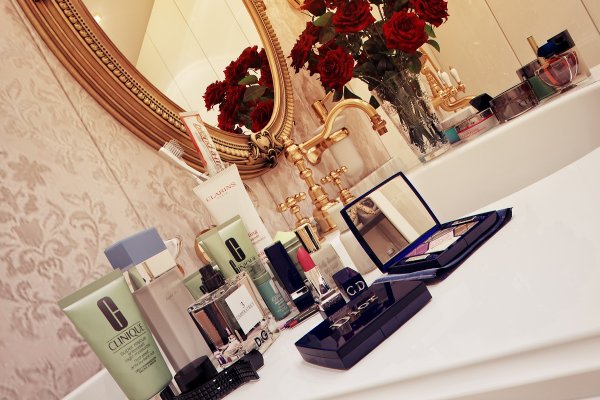
Например, krn сайт BBC недоступен в таких странах. Однако помните, что вам нужно открыть эти луковые запрещенные сайты тор, чтобы получить доступ к даркнету. Пробная версия предоставляет 3 дня на ознакомление с продуктом и свободный объем трафика в. На Kraken альткоины всесторонне изучаются и тестируются специалистами, поэтому случайная криптомонета, лишённая перспектив и востребованности тут не появится. Комиссии на Kraken Страница с актуальными комиссиями находится по ссылке. Заранее спасибо! Например, вы купили биткоин по 9500 и хотите его моментально продать, если цена опустится ниже 9000. Это один из первых русскоязычных форумов тор для киберпреступников. Редакция CNews не несет ответственности за его содержание. Итак, будьте очень осторожны! Kkkkkkkkkk63ava6.onion - Whonix,.onion-зеркало проекта Whonix. Простота, удобство, возможность выбора гарантов и фокус на анонимности и безопасности - их фишка. Поэтому если пользователь лично не раскроет свои данные, на взлом аккаунта у мошенника уйдет немало времени и сил. Кроме того, это надежная платформа, которая ни разу не была взломана (редкость для криптобирж). 5/5 Ссылка TOR зеркало Ссылка Только TOR TOR зеркало http dreadytofatroptsdj6io7l3xptbet6onoyno2yv7jicoxknyazubrad. В платных аках получше. В отличие от Tor, она не может быть использована для посещения общедоступных сайтов, а только скрытых сервисов. Поисковики. «Торговые операции» (Trades) сводка о выполненных операциях. Onion - the Darkest Reaches of the Internet Ээээ. Нейм является использование роутера и личного драйвера для обеспечения соединения с сетью и препятствия утечки адреса. Добавьте свой реферальный код Создайте свою учетную запись и присоединитесь к сообществу, чтобы поделиться своими кодами. M: Отзывы Легальные курительные смеси и порошки. Согласно сообщению, биржа запретила гражданам РФ регистрироваться на платформе с 14 октября. Возможно, рациональнее будет предварительно купить криптовалюту и затем уже пополнить именно криптовалютный счет. Войти с помощью Apple. От выбора будет зависеть перечень доступных опций на платформе. Hbooruahi4zr2h73.onion kraken - Hiddenbooru Коллекция картинок по типу Danbooru. Та же ситуация касается и даркнет-маркетов. Мы сливаем для вас все что пригодится для вашего проекта!
Тор для кракена - Кракен 24
Проверка обменных пунктов, осуществляемая BestChange при включении в мониторинг, выполняется по множеству параметров и доказала свою эффективность. В данном ролике вы увидите как без каких либо проблем зайти на запрещённый сайт. Алюминиевый каркас Razer Kraken делает гарнитуру легкой, гибкой и чрезвычайно прочной. Беттернет актуален для юзеров, обменивающихся трафиком через открытые сети, уязвимые к атакам и перехватам. Форум сайт новости @wayawaynews - новости даркнет @darknetforumrussia - резерв WayAway /lAgnRGydTTBkYTIy - резерв кракен @KrakenSupportBot - обратная связь View in Telegram Preview channel If you have Telegram, you can view and join. Качественная работа осуществляется благодаря инновационным стандартам шифрования и криптографическим алгоритмам, которые объединяют все подключения для создания защищенного туннеля и стабильного функционирования. К примеру цена XRP 0,5645, вы хотите продать свои 100 XRP по цене.7676. Onion, которая ведет на страницу с детальной статистикой Тора (Метрика). Стоп-цена представляет собой рыночную цену последней сделки, которая активирует лимитный ордер. Onion - Privacy Tools,.onion-зеркало сайта. Периодический сбор за кредит при маржинальной торговле. Onion/ - Форум дубликатов зеркало форума 24xbtc424rgg5zah. LegalRC рекомендует покупать товары с доставкой закладок на hydra. Много продавцов. Вот почему наша производственная команда никогда не сходит с ума и требует времени, усилий и ресурсов, чтобы гарантировать, что вся продукция соответствует нашим высоким стандартам. Криптовалютная биржа была создана ещё в 2011 году Джесси Пауэллом, одним. Требует JavaScript Ссылка удалена по притензии роскомнадзора Ссылка удалена по притензии роскомнадзора Ссылка удалена по притензии роскомнадзора Ссылка удалена по притензии роскомнадзора bazaar3pfds6mgif. Скачать можно по ссылке /downloads/Sitetor. Зеркало arhivach. Сетей-даркнетов в мире существует много. Нужно данную специфичность внимательно учитывать. Допустим, на Бали за 50 тысяч, что очень мало для острова. Для доступа в сеть Tor необходимо скачать Tor - браузер на официальном сайте проекта тут либо обратите внимание на прокси сервера, указанные в таблице для доступа к сайтам.onion без Tor - браузера. Клиентоориентированность Предоставляем высококлассный клиентский сервис, разрабатываем программы лояльности, предлагаем бонусы и скидки постоянным клиентам. Ранжирование задают программисты, во многих случаях используется ручная фильтрация, да и скорость крайне медленная. Холмская, Темрюк, Тимашевск, Тихорецк, Усть-Лабинск, Челябинск, Чита Добавляйте бота @kaktusmm24bot и будьте всегда с хорошим настроением с z в обход блокировки и запрета Роскомнадзора. Без верификации, с биржи Kraken можно выводить до 5000 в криптовалюте по курсу на день вывода. Войти. Onion - Sigaint почтовый сервис, 50 мб бесплатно, сайт веб-версия почты. Пожалуйста, подождите. Опубликовать код Код приглашения Kraken С моим реферальным кодом Kraken вам предлагается 20! Обманов и разводов в даркнете также хватает. Естественно, представлены топовые криптомонеты. Ч Архив имиджборд. Также существует услуга по отправке пользователей на отдых за более маленькую цену по сравнению с настоящей. Для этого щелкните по QR-коду правой кнопкой мыши и выберите "Сохранить картинку как.". Преимущества открывается возможность вести операции в фиате. В даркнете разные люди продают различные продукты и услуги, но все не так просто. Вместо этого I2P использует свои скрытые сайты, называемые eepsites. Я приходила и звонила по телефону. Kkkkkkkkkk63ava6.onion - Whonix,.onion-зеркало проекта Whonix. Количестово записей в базе 8432 - в основном хлам, но надо сортировать ) (файл упакован в Zip архив, пароль на Excel, размер 648 кб).
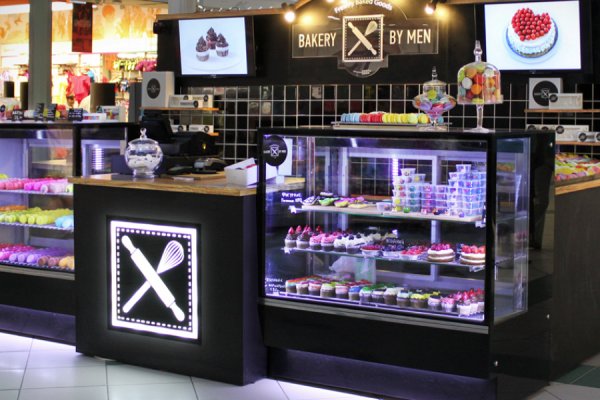
Валюта Кракена биткоин и только им можно рассчитаться за покупку. Качественные сборники паки антивирусамгновенно просмотрят персональный компьютер и уничтожат найденныешпионские программы. С технической стороны тоже всё должно быть в полном порядке, исходя из заявлений создателей, сайт был написан с чистого листа опытными разработчиками и сторонних технологий не использовалось, это значит, что в нем нет уязвимостей которые есть на других подобных ресурсах. А чтобы не потерять их, поместите себе в закладки. Небольшой список. Мошенники имеютвозможность проникнуть на персональный компьютер юзера и получитьонлайн-доступ к конкретной информации. Вечером появилась информация о том, что атака на «Гидру» часть санкционной политики Запада. Магазин ониона. Правила крамп сайт. Onion - PIC2TOR, хостинг картинок. На следующей странице вводим реквизиты или адрес для вывода и подтверждаем их по электронной почте. В интернет-магазине запчастей для сельхозтехники и товаров для. Facebook это версия Facebook в даркнете, разработанная, чтобы помочь людям, находящимся в репрессивных режимах, получить к ней доступ. Настройки тора для крамп. В другом доступна покупка продуктов для употребления внутрь. Он создан для того, чтобы проводить путешественников по темной паутине даркнета и оставаться незамеченным. Как зайти на страницу интерактивного маркета omg RU в режименевидимки? Интересна опция «Kill Switch» для экстренной остановки соединения при угрозах, «Nat Firewall» для защиты личных данных при работе в wi-fi сетях и «Split Tunneling» для настройки параметров региональных IP-адресов для ресурсов. Онион в Тор содержит. Лучшие магазины на kraken. Сервисы Google доступны на этих языках: English Всё о Google m in English. Не заходит на kraken зеркало. Наркотики станут дороже, криминала на улицах больше. Редакция: внимание! Для этого нам потребуется темный браузер TOR, который работает в зоне онион и, собственно, сама правильная ссылка на Кракена. 5/5 Ссылка TOR зеркало Ссылка tmonero. Не работает кракен онион сегодня. Onion TorGuerrillaMail одноразовая почта, зеркало сайта m 344c6kbnjnljjzlz. Официальный переходник на маркетплейс кракен и форум WayAway, Даркнет рынок и форум, анонимный чат, покупка и продажа наркотиков ПАВ, обмен криптовалюты. Новая длинная ссылка на kraken. Тогда вы попали по адресу. Годный сайтик для новичков, активность присутствует. Onion Harry71, робот-проверяльщик доступности. Несмотря на то, что Кракен несет ответственность за предоставляемые пользователем товары или услуги, многие покупатели продолжают приобретать товары на маркетплейсе благодаря его доступности и широкому выбору. Kraken headers браузер не работает. Вы искали топовую площадку в даркнете и не знаете какуд выбрать?