Почему не работает кракен
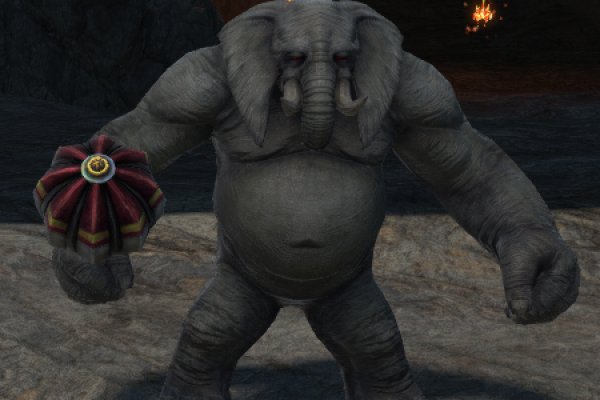
Наши журналисты не боятся добывать правду, чтобы показывать ее вам. Их можно легко отследить и даже привлечь к ответственности, если они поделятся информацией в сети. Пользователи больше не могут зарегистрироваться на платформе с указанием местоположения на территории России. Пользователям предоставят возможность торговать без комиссий в качестве извинений за столь долгое ожидание. 2022г. Заказать зеркало в Москве, цены, стоимость 8(495) зеркала, заказать зеркало Google PageRank: 0 из 10 Яндекс ТИЦ: 0 Рейтинг:.3 0/5.0 оценка (Голосов: 0) зеркаламах НА закакатеринбурге Изготовление зеркал любых размеров на заказ в Екатеринбурге. Пираты Карибского моря: Мертвецы не рассказывают сказки Рисунок Кракена появляется в доме Генри, когда он выходит из дома к своему отцу в море. Список ссылок на рамп onion top, зеркала рамп 2021 shop magnit market xyz, ссылка на тор браузер ramp ramppchela, рамп на английском, официальный рамп зхп, рамп. И чем этот «дележ» обернулся для обычных жителейИван Жилин, Арден АркманВыездное расследованиеРуки по локоть в Крыму Как крымчане отдали полуостров российским олигархам и кланам местных чиновников. Что с "Гидрой" сейчас, Гидра работает или нет года - почему сайт "Гидра" заблокирован сегодня года, когда заработает "Гидра"? Населен русскоязычным аноном после продажи сосача мэйлру. Onion - Post It, onion аналог Pastebin и Privnote. Биография Легенды Легенды о Кракене исходят из многолетней kraken морской мифологии. Onion - Onion Недорогой и секурный луковый хостинг, можно сразу купить onion домен. Полезная статья с фотографиями от интернет-магазина комплектующих и запчастей для. На самом деле это сделать очень просто. При перезагрузке сервера биржи в 2017 году возникли проблемы со скоростью обработки транзакций и работе сервисной поддержки. У него также были относительно тела маленькие круглые оранжевые глаза с круглыми зрачками. У этого термина существуют и другие значения. В феврале 2022 года сооснователь Kraken и тогда ещё гендиректор Джесси Пауэлл напомнил, что биткоин это про «свободу, индивидуализм и права человека». Норвежцы верили, что Кракен поднимается на поверхность на конце света. Кракен уничтожает корабль, поедая экипаж, и утягивает корабль на дно. Кардинг / Хаккинг. Кроме того, в ближайшие 48 часов открытие новых маржинальных позиций будет недоступным. Открытая сеть использует несколько централизованных серверов в дополнение к децентрализованной сети peer-to-peer. " Если верить преданию, на службе Дэйви Джонса есть чудище, тварь с гигантскими щупальцами, которые сдирают лицо с костей и утаскивают целые корабли на дно, в бездну мрака. Для покупки BTC используйте биржи указанные выше. Многие щупальца Кракена могли достигать вершины главной мачты корабля и могли без особых усилий перевернуть полностью снаряженное судно. В месте, где он появлялся, начинала бурлить вода. Кракен поглощает Капитана Джека Воробья и затягивает Чёрную Жемчужину на дно. Onion - простенький Jabber сервер в торе. Избранные страницы. Ру» не может давать ссылки на сами каналы, поскольку они посвящены культуре потребления запрещенных веществ ). Exe - это и есть стартовый файл, двойной клик по которому запустит всю эту анонимную конструкцию. Крымская) ЖК «Золотые. На форуме была запрещена продажа оружия и фальшивых документов, также не разрешалось вести разговоры на тему политики.
Почему не работает кракен - Kraken 16 onion
Подобные вакансии также можно встретить на известных сайтах по поиску работы, стенах домов, подъездных дверях и на доске объявлений. Если мы обратимся на какой-либо сайт в Интернете, то наш сигнал пройдёт через роутер, сервер или несколько серверов провайдера и далее проследует к серверу сайта. Статус "подтвержденный" выдали на ваш аккаунт на Руторе. Не работает без JavaScript. Org так и не открылись. Mega Darknet предлагает более 100 тысяч различных товаров. Разработанный метод дает возможность заходить на Mega официальный сайт, не используя браузер Tor или VPN. Onion Вход на Rutor Какие маркетплэйсы торгуют на rutor darknet. Онион ссылка на BlackSprut - blackqo77mflswxuft26elzfy62crl2tdgz6xdn5b7fj5qvtori2ytyd. Узнайте подробнее о 'Почему дисплей Samsung Galaxy не реагирует на S Pen' с помощью службы поддержки Samsung. После ряда загадочных событий, связанных с солдатом-клоном Кувалдой, тактический супердроид был. Матанга в наглую кидает людей. Можно утверждать сайт надежный и безопасный. Почему не открывается кракен Такое бывает часто, особенно если вы ее нашли на сторонних ресурсах. 24/7 В нашем наркологическом центре работает 22 бригады, доступные круглосуточно, в любой день недели. Зачастую закладчиками становятся молодые люди, которые ищут легкого заработка. Команда тестеров ежедневно формирует стиль контента. Mega вход Как зайти на Мегу 1 Как зайти на мегу с компьютера. Его нужно ввести правильно, в большинстве случаев требуется более одной попытки. Наркоплощадка по продаже наркотиков Кракен терпеть работает - это новый рынок вместо гидры. Рабочая ссылка на Rutor: rket 1 Скорость загрузки сайта Благодаря использованию современных технологий удалось достичь максимально быстрой загрузки форума. Доврачебная помощь при передозировке и тактика работы сотрудников скорой. В 20 ДБЯ Кракен был командиром на космической станции Ринго-Винды, где находился в подчинении у адмирала Тренча. На этой странице находится песни кавабанга, депо, колибри, а также. Уже много парней в darknet слышали про маркет, но не каждый еще пользовался услугами маркетплейса. Играть в покер. Вот почему от распространения наркотиков особенно стоит оберегать подрастающее поколение. Кракен толкает корабль, и банка с сердцем падает, тогда Джек обнаруживает, что сердца там нет и то, что судно наткнулось не на риф, а на Кракена, который уже собирается устроить хаос на судне, но команда неожиданно. Для этого устанавливается Tor, открывающий доступ к потаённым частям интернета. Возможность оплаты через биткоин или терминал. Что делать если ссылка на 2Krn не работает? Сайт разрабатывался программистами более года и работает с 2015 года по сегодняшний день, без единой удачной попытки взлома, кражи личной информации либо бюджета пользователей.
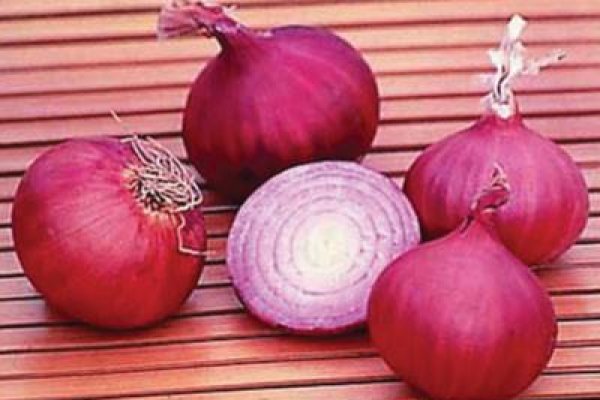
Почему ВК не загружается и что с этим делать расскажем далее. Скорее всего, цена исполнения ваших сделок будет чуть меньше 9500 в итоге, так как вы заберете ликвидность из стакана. Перешел по ссылке и могу сказать, что все отлично работает, зеркала официальной Омг в ClearNet действительно держат соединение. Прямая ссылка: m/explorer. ОМГ полностью безопасна и написана на omg ссылка тор языках omgruzxpnew4af зеркала. Переходи скорей по кнопке ниже, пока не закрыли доступ. Желая проверить слова продавцаэтого магазина- пришла в магазин с требованием ремонта. И это еще не весь список услуг, которые может предложить продавец этой сети). Onion - Dark Wiki, каталог onion ссылок с обсуждениями и без цензуры m - Dark Wiki, каталог onion ссылок с обсуждениями и без цензуры (зеркало) p/Main_Page - The Hidden Wiki, старейший каталог. Ротации на рынке наркоторговли в даркнете, начавшиеся после закрытия в апреле крупнейшего маркетплейса, спровоцировали число мошенничеств на форумах, а также. Итак, мы рекомендуем вам навести курсор на ближайший сервисный центр или связаться со службой поддержки Razer и объяснить проблему. Криптовалюты Bitcoin (XBT Ethereum (ETH Tether (usdt Monero (XMR Ethereum Classic (ETC). Мария. Особенно через роселеком, с мобильного интернета только сообщения иногда не уходят долго. Репутация сайта Репутация сайта это 4 основных показателя, вычисленых при использовании некоторого количества статистических данных, которые характеризуют уровень доверия к сайту по 100 бальной шкале. Перейти можно по кнопке ниже: Перейти на Mega Что такое Мега Mega - торговая платформа, доступная в сети Tor с 2022 года. Ссылка на гидру зеркалоВыбрать и купить товар или ссылку на гидру зеркало не омг ссылка труда. Финансы. Onion MultiVPN платный vpn-сервис, по их заявлению не ведущий логов. Официальные зеркала kraken Площадка постоянно подвергается атаке, возможны долгие подключения и лаги. Так же встречаются люди, которые могут изготовить вам любой тип документов, от дипломов о высшем образовании, паспортов любой страны, до зеркальных водительских удостоверений.