Не приходят деньги на кракен
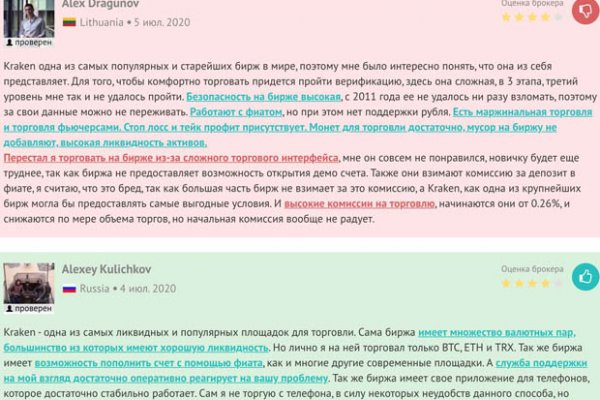
Указать количество монет. Иногда отключается на несколько часов. Onion - BitMixer биткоин-миксер. Ответ на вторую часть вопроса однозначно простой - запрещённые товары, а вот ответ на первую не так прост, как кажется на первый взгляд. С точки зрения приватности отличный выбор, но ищет DDG исключительно по открытому интернету, так что в наших изысканиях он не пригодится. Он назначает задачу клиенту, а не серверу, устраняя любую уязвимость, связанную с сервером. Он не передает IP-адреса или историю поиска для защиты вашей конфиденциальности. Иногда поисковик даже может завести не туда, выдав ссылку на фейковый проект. Словарь терминов Склад человек, хранящий у себя большие объемы наркотиков, реализующий их через мастер-клады закладки с большим количеством вещества для кладмена. К сожалению, требует включенный JavaScript. Частично хакнута, поосторожней. Он в числе прочего запрещает гражданам и резидентам России владеть криптовалютными кошельками, создавать учетные записи или хранить цифровые активы на территории еврозоны независимо от суммы депозита. Разберем процесс регистрации по шагам:. Onion - OutLaw зарубежная торговая площадка, есть multisig, миксер для btc, pgp-login и тд, давненько видел её, значит уже достаточно старенькая площадка. Примените настройки, нажав на «ОК». Отметим, что при указании пароля необходимо использовать буквы, цифры и специальные символы. Мобильное приложение Kraken и курсы онлайн в кармане В 2019-ом году у Kraken появились мобильные приложения для обеих платформ Android и Apple. Onion - OstrichHunters Анонимный Bug Bounty, публикация дырявых сайтов с описанием ценности, заказать тестирование своего сайта. Поэтому нашел хороший ролик под названием «КАК попастаркнет? На сегодня Kraken охватывает более 20 криптовалют (. Обманов и разводов в даркнете также хватает. Содержание В действительности на «темной стороне» можно найти что угодно. Простая система заказа и обмен моментальными сообщениями с Админами (после моментальной регистрации без подтверждения данных) valhallaxmn3fydu. Если после прочтения нашей инструкции и официальной справки у вас до сих пор остались вопросы, то вы можете оставить их в Telegram-боте @onlypreico_bot. Не пользуйтесь, чем попало и на что Вас выведет первая строка в поисковике, чаще всего это kraken подставные сайты, которые заберут Ваши деньги и никаких надежд на их возврат не будет, на таких даркнет-маркетах обитают так называемые "кидалы". Onion - Alphabay Market зарубежная площадка по продаже, оружия, фальшивых денег и документов, акков от порносайтов. Криптовалюты Bitcoin (XBT Ethereum (ETH Tether (usdt Monero (XMR Ethereum Classic (ETC). Темная паутина это часть Интернета, в которую вы входите только с помощью определенного инструмента. Зеркало arhivach. Перейдите в «Настройки сети». Литература. Вы не хотите ставить просто лимитный ордер, так как в этом случае он будет сразу виден в стакане и будет служить неким сопротивлением. Но стоит понимать, что это не какая-то проблема, которую нужно идти и решать. В таком случае вы можете установить, что при достижении цены в 9500 пусть будет выставлен ордер на продажу по цене в 9499, например. У торрент-трекеров и поисковиков вроде RuTor и The Pirate Bay в обязательном порядке есть ссылки в onion, которые дают пользователям возможность не обращать внимания на запреты и ограничения. Согласно их мнению, даркнет основная помеха для создания продуктивных DRM технологий. Onion - Neboard имиджборд без капчи, вместо которой используется PoW. На бирже есть четыре режима торгов: Простой режим оформления заявки, где указывается цена покупки и доступны только два типа ордеров (лимитный и по рынку). а также предлагает торги в парах с фиатными валютами (EUR, USD, CAD, GPB.д.). Onion - Нарния клуб репрессированных на рампе юзеров. При первом входе необходимо выбрать из двух параметров: просто соединиться или настроить сетевые параметры. Комиссии на торги в даркпуле биржи Kraken При использовании данной функции, максимальная комиссия составляет 0,36, а минимальная 0,20 в зависимости от объема торгов. Заполняем регистрационную форму и соглашаемся с условиями биржи. Первоначально сеть была разработана военными силами США. Регистрация на бирже Kraken? К моему сожалению, она периодически доступна только через Tor.
Не приходят деньги на кракен - Кракен сайт как выглядит
- Автосалон Ramtruck. Наконец-то нашёл официальную страничку Омг. 4599 руб. 3 дня назад Всем привет. Для покупки этой основной валюты, прямо на сайте встроенные штатные обменные пункты, где вы можете обменять свои рубли на bit coin. Для данной платформы невозможно. Это не полный список кидал! Обращайтесь в компанию. Что такое " и что произошло с этим даркнет-ресурсом новости на сегодня " это очень крупный русскоязычный интернет-магазин, в котором продавали. Каталог рабочих сайтов (ру/англ) Шёл уже 2017й год, многие сайты. Hydra admin ответил 3 месяца назад. Α-Пирролидинопентиофенон синтетический психостимулятор класса катинонов, представляет собой дезметиловый аналог пировалерона и представитель нового класса α-пирролидинофенонов (в который также входят, к примеру, mdpv, mppp, mdppp. Ссылка из видео. Как узнать ссылку на матангу, официальная ссылка на матангу 2021, фальшивые гидры matangapchela com, сайт матанга проблемы onion top com, матанга онион не работает сайт. Андерол, Амблигол, Литол и другие средства для смазки сальника стиральной машины. Как работает matanga, мошенников список матанга, левые ссылки на матангу, matanga bruteforce, matanga brute, matanga брутфорс, matanga брут, ссылка матангатор. Веб-студия Мегагрупп занимается разработкой для бизнеса в Москве, Санкт-Петербурге и по всей России Стоимость от 7500. Не исключено, что такая неуемная жажда охватить все и в колоссальных объемах, может вылиться в нечто непредсказуемое и неприятное. Мега. Спасибо администрации Омг Onion и удачи в продвижении! 3дрaвcтвуйте! Залетайте пацаны, проверено! Официальный сайт Hydra onion (заходить через ТОР). Все зеркала onion. Также в числе ключевых арендаторов магазины «Ашан «ОБИ» и «Леруа Мерлен». 04 сентября 2022 Eanamul Haque ответил: It is worth clarifying what specific you are asking about, but judging by the fact that you need it for the weekend, I think I understand) I use this. Текст куда-то делся. Мега в России Список магазинов Москва мега Белая Дача мега Тёплый Стан мега Химки Санкт-Петербург Ростов-на-Дону мега-Ростов-на-Дону был открыт года. Храм культовое сооружение, предназначенное для совершения богослужений и религиозных обрядов. Через iOS. Топ сливы. ОМГ! Готовые закладки онлайн в городах России, http. Ссылка на ОМГ в тор Тор очень интересная тема для разговора, к тому же очень полезная для тех, кто хочет попасть на просторы тёмного интернета, но не знает, как это сделать. Каталог рабочих сайтов (ру/англ) Шёл уже 2017й год, многие сайты. Официальная страница!
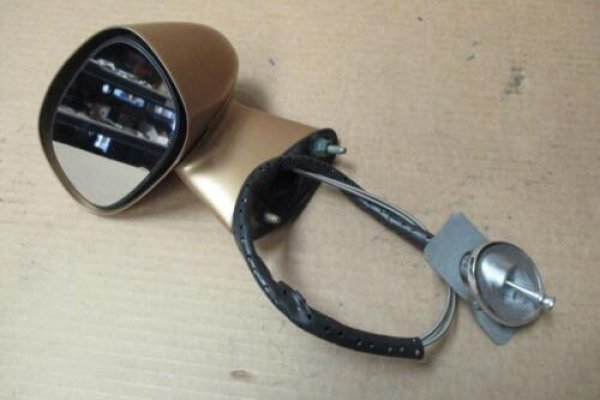
Всё что нужно: деньги, любые документы или услуги по взлому аккаунтов вы можете приобрести, не выходя из вашего дома. Как отправить фото в диспуте на гидре! Вышла в каком году? Из-за того, что они знали, что ты употребляешь наркотики? 19 дней, я помню, лежала, потому что не могла даже на палочку опереться и встать. Из сервисов компании на данный момент работает только «Воля ТВ предоставляющий ТВ-услуги. Среди крупных игроков можно выделить NeMoloko, VolkoMoloko, Green idea, SooperFoods, а также серия Green Milk от «Союз Пищепром». Если вы не хотите случайно стать жертвой злоумышленников - заходите на OMG! Кеды 5200 сделок Те самые Кеды в деле! "Правильно делают, надо с этим бороться. Кстати, если кажется, что фото должно было загрузиться, но в чате не появилось, бывает достаточно обновить страницу. Допустим, товар стоит 10 000, а на балансе всего 3 000. Помню, когда я уже вышла на свободу, Комбивудин на меня так подействовал, что при норме у человека 130, у меня гемоглобин был всего лишь. Афиша. Добро пожаловать на официальный сайт мониторинга даркнет площадок. Это, конечно, была очень большая потеря для меня. Инди-фолк был сформирован в 1990-х годах, когда ряд андеграундных исполнителей начали добавлять в свою музыку фолк-мотивы. Другие способы отправки изображений на Гидре. Ру" совладелец небольшого регионального онлайн-магазина наркотиков. При предоставлении адвоката по назначению следует иметь в виду, что с большой долей вероятности такой защитник помощь вам не окажет, а может и навредить.