Не получается зайти на кракен

Перейдите в «Настройки сети». Языке, покрывает множество стран и представлен широкий спектр товаров (в основном вещества). Onion Подробности про них вы можете узнать в нашей статье «Поисковики для Тор браузера». Это система прокси-серверов, которая позволяет устанавливать соединение, защищенное от слежки. Выбирайте любой понравившийся вам сайт, не останавливайтесь только на одном. Статья 327 УК РФ лишение свободы на срок до двух лет. После этого у zerkalo вас будут сутки на то, что бы забрать купленный товар и закрыть сделку. На уровне Intermediate система запросит информацию о роде занятий пользователя, копию документа, удостоверяющего личность и подтверждение резидентства. Успей получить своё Репост из: Даркнет форум России WayAway (телеграм) кракен вход, актуальные ссылки и зеркала. Топовые семена конопли здесь! Рейтинг самых безопасных криптовалютных бирж Kraken хранит 95 всех активов на холодных кошельках. Crdclub4wraumez4.onion - Club2crd старый кардерский форум, известный ранее как Crdclub. Давайте последовательно разберемся с этими вопросами. Там же размещены актуальные зеркала, которые постоянно обновляются. ( зеркала и аналоги The Hidden Wiki) Сайты со списками ссылок Tor ( зеркала и аналоги The Hidden Wiki) torlinkbgs6aabns. Компания активно продвигает себя как сервис для доступа к онлайн-кинотеатрам Hulu и Netflix, а также сотрудничает c отечественным «Турбофильмом». Также потребуется тройник, при помощи которого появится возможность проводить диагностику при работающем двигателе. Теперь для торговли даже не обязателен компьютер или ноутбук, торговать можно из любой точки мира с помощью мобильного телефона! Не пользуйтесь, чем попало и на что Вас. Для включения двухфактоной авторизации зайдите в Аккаунт безопасность и активируйте ползунок напротив двухфакторной авторизации на крамп кракен вход: Активируем двухфакторную авторизацию На следующем шаге выбираем опцию Authenticator App. Мега 2022! Он krakenate предложит вам дополнительный уровень конфиденциальности и анонимности для доступа к глубоким частям Интернета. Сайты в даркнете часто используют технологию шифрования Tor. Кракен зеркало предоставляет лучшие условия для дилеров. «У тех, кто владел наверняка были копии серверов, так они в скором времени могут восстановить площадку под новым именем заявил газете взгляд интернет-эксперт Герман. Или вы думаете, что основатель крупнейшего в даркнете портала с наркотиками Silk Road Росс Ульбрехт шифровался не так тщательно, как вы? Это случается из-за того, что сетевой трафик перемещается по разным странам, чтобы соблюсти конфиденциальность. Скачать можно по ссылке /downloads/Sitetor. Они есть, причем их довольно большое количество. После кликните по меню «Активация аккаунта». Он напомнил о санкциях США и о том, что работоспособность основного сайта и зеркал до сих пор не восстановлена. Сейчас в интернете появилось большое количество поддельных сайтов, которые выдают себя за популярный ресурс и обманывают посетителей. Для регистрации нужен ключ PGP, он же поможет оставить послание без адресата. Бензобак. Как мы знаем "рынок не терпит пустоты" и в теневом интернет пространстве стали набирать популярность два других аналогичных сайта, которые уже существовали до закрытия Hydra. Все больше пользователей хотят покупать именно на krmp cc и это не удивительно. Такая проблема наблюдается практически у каждого пользователя, так как адрес данного сайта часто меняется, это может быть. Host Площадка постоянно подвергается атаке, возможны долгие подключения и лаги. Если Вы осуществляете вход с ПК зайдите в свою антивирусную программу и отключите. Зеркала для входа в kraken через тор - kraken. Tor поверх VPN подразумевает доверие VPN-провайдеру, но не вашему интернет-провайдеру, и является лучшим вариантом для доступа к сайтам. Так, пользователи жалуются на сложность поэтапной верификации и на некомпетентность сотрудников службы поддержки.
Не получается зайти на кракен - Кракен шоп интернет нарко
Кроме того, в игре можно получить любой предмет и экипировку игровым путем, без дополнительных вложений. Посмотреть замены 14 замен для Tor Browser. Безопасность Безопасность yz7lpwfhhzcdyc5y.onion - rproject. Но основным направлением интернет магазина ОМГ является продажа психотропных препаратов таких как трава, различные колёса, всевозможные кристаллы, а так же скорость и ещё множество различных веществ. Подключится к которому можно только через специальный браузер Tor. Это означает, что вам не нужно будет открывать и загружать каждую ссылку из списка, чтобы убедиться, что она работает. Легкая настройка можно изменить сетевые мосты, подменять заголовки http, сменить IP-адрес. При описанных выше симптомах следует замерить фактическое давление топлива в рампе. Tor поверх VPN подразумевает доверие VPN-провайдеру, но не вашему интернет-провайдеру, и является лучшим вариантом для доступа к сайтам. Особых знаний для входа на сайт OMG! Наркологическая клиника Здравница. Сейчас одна из крупных бирж. Зайти на сайт Омг через Тор по ссылке онион. Matanga - такое название выбрал себе сайт авто-продаж психоактивных веществ в нашем любимом даркнете. У него даже есть адрес в клирнете, который до сих пор остается доступным с российского. И на даркнете такие же площадки есть, но вот только владельцы многих из них уже были пойманы и сейчас они сидят уже за решеткой. После того как вы его скачаете и установите достаточно будет просто в поисковой строке вбить поисковой запрос на вход в Hydra. Вы топ сайтов тор для доступа к любому контенту или сервису в даркнете. Новый сервер Кракен Онлайн будет запущен 24 марта! Onion XmppSpam автоматизированная система по спаму в jabber. Процесс работы сети Tor: После запуска программа формирует сеть из трех случайных нод, по которым идет трафик. UPD: Появилась onion ссылка на сайт кракен, сохраняйте. После регистрации на kraken onion, вам станет доступен огромный функционал сайта kraken в сети onion. Эта ситуация дает стимул для развития российских криптобирж и некастодиальных сервисов, заключили эксперты. Onion ссылкам вам нужно скачать браузер Tor. Оговоримся сразу, что через обычный портал зайти на сайт не получится, поэтому, чтобы обойти запреты, нужно выполнить такую процедуру: Ищем ссылку на kraken darknet для Тор. Используя официальные зеркала kraken по ссылке попадаем на сам сайт. Преимущества Кракена Товары Ассортимент товаров поражает здесь можно купить абсолютно любые вещества, информацию и услуги, документы и цифровые товары. И так вы уже сделали все, что бы попасть на кракен: скачали тор, зашли на сайт и прошли регистрацию. Ссылка на сайт Кракена дает реальный доступ к магазинам на воскресенье. Onion/ Psy Community UA украинская торговая площадка в виде форума, наблюдается активность, продажа и покупка веществ. Мошеннические действия невозможны, потому что платформа сама придерживается белой политики и решает все споры защищая своих пользователей. Личный кабинет на бирже Kraken Для того, чтобы пополнить счет на Kraken, необходимо: Войти в личный кабинет. Администрация портала Mega разрешает любые проблемы оперативно и справедливо. Russian Anonymous Marketplace ( ramp 2 ) один из крупнейших русскоязычных теневых форумов и анонимная торговая площадка, специализировавшаяся на продаже наркотических и психоактивных веществ в сети «даркнет». 52 Windscribe Windscribe -совместное настольное приложение и расширение для браузера, блокирует рекламу. Перечень популярных : опиаты, курительные, нюхательные смеси. Такое бывает часто, особенно если вы ее нашли на сторонних ресурсах. ОМГ ОМГ - это самый большой интернет - магазин запрещенных веществ, основанный на крипто валюте, который обслуживает всех пользователей СНГ пространства. Ресурс доступен в клирнете, также у него есть сервер Jabber, почитаемый пользователями не меньше самого форума. Воспользуйтесь зеркалом магазина с нашего сайта. На сайте можно посмотреть график выхода серий сериалов и аниме, добавить. Множество Тор-проектов имеют зеркала в I2P. Это ВПН браузер, который позволяет посещать ресурсы в даркнете. На Меге сотни тысяч зарегистрированных пользователей и понятное дело, что каждому не угодишь. С первых дней Kraken придерживалась строгих внутренних стандартов тестирования и безопасности, оставаясь в закрытой бета-версии в течение двух лет перед запуском.
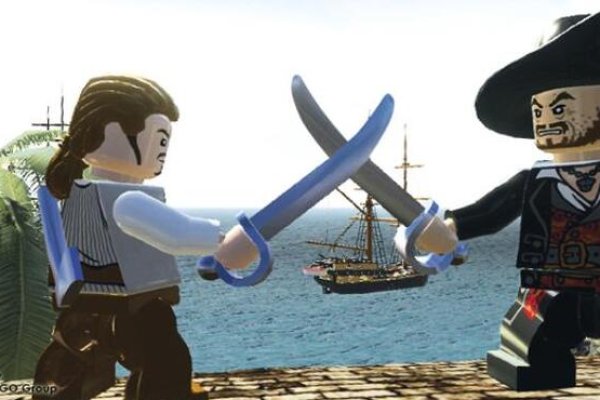
К тому же Тор браузер адаптирован под любой вид операционной системы. Также мы будем благодарны, если вы оставите свою обратную связь по бирже. По сути это система, которая поддерживает анонимный обмен информацией. Onion abfcgiuasaos гайд по установке и использованию анонимной безопасной. Доступ через tor - http matangareonmy6bg. Читайте также: Биржа Bitstamp: регистрация, настройка, отзывы, зеркало Биржа Binance: комиссия, регистрация, отзывы Биржи без верификации: ТОП-5 торговых площадок. Зашифрованный веб-шлюз можно использовать для неопасных входов с различных устройств. Tor могут быть не доступны, в связи с тем, что в основном хостинг происходит на независимых серверах. Для подключения к сайтам, доступным только. ДакДакГоу DuckDuckGo самая популярная частная поисковая система. Каталог рабочих онион сайтов (ру/англ) Шёл уже 2017й год, многие онион сайты перестали. Категории товаров составлены логично, на каждой странице есть поиск, поэтому не составит никакого труда найти нужную вам вещь. Flibusta для любителей читать Даркнет друг торрентов Еще в начале-середине нулевых торренты никто и не думал запрещать. Подключится к которому можно только через специальный браузер Tor. Перейдите в «Настройки сети». Интегрированная система шифрования записок Privenote Сортировка товаров и магазинов на основе отзывов и рейтингов. Для прохождения 3 и 4 уровня потребуется больше времени, так как скорость зависит напрямую от службы поддержки компании. Вместо этого I2P использует свои скрытые сайты, называемые eepsites. Торговые площадки СНГ monza крупнейший торговый кардинг форум в СНГ. Для мобильных устройств: Скачать VPN - iphone android После окончания установки, запустить приложение и установить соединение. Прямая ссылка: http wasabiukrxmkdgve5kynjztuovbg43uxcbcxn6y2okcrsg7gb6jdmbad. Дальше стандартная схема: качаем браузер, устанавливаем, входим и ищем сайт. Даже если он будет выглядеть как настоящий, будьте бдительны, это может быть фейковая копия. В ТОР. Они не смогут скрываться в даркнете или на форумах, они не смогут скрываться в России или где-то в других странах сказано в заявлении Минфина. Есть немало приложений с неплохой оценкой: Tor web Browser, vpntor, Луковка. Время.00. Сделать это можно с помощью прямого перевода с банковской карты или же оплатить криптовалютой. Доступны как цифровые активы, так и фиаты. Onion - onelon, анонимные блоги без цензуры.