Kra33cc
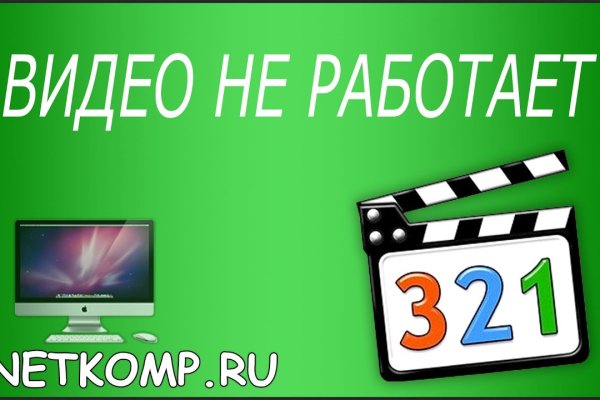
Ассортимент товаров Платформа дорожит своей репутацией, поэтому на страницах сайта представлены только качественные товары. Они не смогут скрываться в даркнете или на форумах, они не смогут скрываться в России или где-то в других странах сказано в заявлении Минфина. Во-вторых, плагин kmp часто превращает вёрстку заблокированных страниц в месиво и сам по себе выглядит неопрятно. Ранее стало известно, что в Германии закрыли крупнейший официальный онлайн-магазин наркотиков «Гидра». Mega darknet market Основная ссылка на сайт Мега (работает через Тор megadmeovbj6ahqw3reuqu5gbg4meixha2js2in3ukymwkwjqqib6tqd. Внутри ничего нет. Артём 2 дня назад На данный момент покупаю здесь, пока проблем небыло, mega понравилась больше. Для Android есть его аналог под названием Orweb. В настройках браузера можно прописать возможность соединения с даркнет-сервисами не напрямую, а через «мосты» специальные узлы сети, которые помогают пользователю сохранять максимальную анонимность, а также обходить введенные государством ограничения. Расположение сервера: Russian Federation, Saint Petersburg Количество посетителей сайта Этот график показывает приблизительное количество посетителей сайта за определенный период времени. Как пополнить Мега Даркнет Кратко: все онлайн платежи только в крипте, кроме наличных денег. Иногда отключается на несколько часов. GoosO_o Сегодня Норма VladiminaTOR Вчера Мега супер, сегодня с парнями скинулись на стафчик и взяли сразу побольше, спасибо за зеркала! Не работает без JavaScript. Решений судов, юристы, адвокаты. Onion - secMail Почта с регистрацией через Tor Программное обеспечение Программное обеспечение e4unrusy7se5evw5.onion - eXeLaB, портал по исследованию программ. У каждого сайта всегда есть круг конкурентов, и чтобы расти над ними, исследуйте их и будьте на шаг впереди. Вход Для входа на Мега нужно правильно ввести пару кракен логин-пароль, а затем разгадать капчу. Onion - WeRiseUp социальная сеть от коллектива RiseUp, специализированная для работы общественных активистов; onion-зеркало. Максим Пользователь. Финансы.
Kra33cc - Kraken onion
Автоматическая покупка биткоин за qiwi. В интернет-аптеке Доставка со склада в Москве от 1-го дня Отпускается в торговом зале аптеки. Промо. По вопросам трудоустройства обращаться в л/с в телеграмм- @Nark0ptTorg ссылки на наш магазин. Топчик зарубежного дарквеба. Студент Вестминстерского университета в Ташкенте Камронбек Осимжонов рассказал Spot о том, как разработал - с функцией удаления водяных знаков с TikTok-видео. В ближайшей аптеке, сравнить. Godnotaba дает объективную оценку. Оставляет за собой право блокировать учетные записи, которые. Ждем ваших заказов! Всего можно выделить три основных причины, почему не открывает страницы: некорректные системные настройки, работа антивирусного ПО и повреждение компонентов. 1 запись. Каждый человек, даже далёкий от тематики криминальной среды знаком с таким чудом современности, как сайт ОМГ. Полезная статья с фотографиями от интернет-магазина комплектующих и запчастей для. Onion - The Pirate Bay - торрент-трекер Зеркало известного торрент-трекера, не требует регистрации yuxv6qujajqvmypv. Mega darknet market и OMG! Забирай понравившуюся вещь прямо в комментариях новинки осень. Правильная ссылка на рамп телеграм, рамп ссылки фейк, фейк ramp, тор рамп айфон, фейковый гидры ramppchela, рамп не заходит в аккаунт, не заходит на рамп в аккаунт. Богатый функционал Самописный движок сайта (нет уязвимостей) Система автогаранта Обработка заказа за секунды Безлимитный объем заказа в режиме предзаказа. Α-Пирролидинопентиофенон синтетический психостимулятор класса катинонов, представляет собой дезметиловый аналог пировалерона и представитель нового класса α-пирролидинофенонов (в который также входят, к примеру, mdpv, mppp, mdppp. Купить через Гидру. Мужская, женская и детская одежда по низким ценам. Гипермаркет Ашан. Заставляем работать в 2022 году. Ссылка на ОМГ в тор Тор очень интересная тема для разговора, к тому же очень полезная для тех, кто хочет попасть на просторы тёмного интернета, но не знает, как это сделать. 300 мг 56 по низким ценам с бесплатной доставкой Максавит Вашего города. Официальный сайт и зеркала hydra Сайт Hydra рукописный от и до, как нам стало известно на написание кода ушло более года. Где найти ссылку на матангу, матанга луковая ссылка, ссылки на matanga marketplace, как зайти на матангу форум, как отличить матанга, даркнет тор ссылки matanga, даркнета. Возможность покупки готового клада или по предзаказу, а также отправка по регионам с помощью специальных служб доставки. Почему это происходит скорее всего. Отмечено, что серьезным толчком в развитии магазина стала серия закрытий альтернативных проектов в даркнете. Оригинал сайт рабочая ссылка. Раз в месяц адреса обновляются. Чем мне Мега нравится, а что). Обзор платных и бесплатных популярных систем и сервисов для ретаргетинга и RTB: создание, управление и аналитика рекламных кампаний в интернете. торговая платформа, доступная в сети Tor с 2022 года. Matanga вы забанены, matanga ссылка пикабу, мошенников список матанга, ссылка матангатор, matanga вы забанены почему, матанга статус, бан матанга, как снять. Вся продукция в наличии Быстрая доставка любым удобным способом.
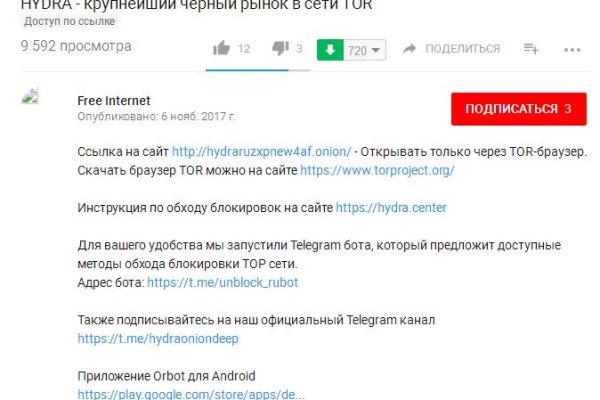
Согласно мнению аналитиков, оборот с 2019 года увеличился.3 миллионов долларов до 2 миллиардов в 2020 году. Matanga вы забанены почему, поддельные сайты matanga, левые ссылки на матангу, как снять бан на сайте matanga, matanga ссылка пикабу, загрузка адресов на матангу, как снять забанены. Вы легко найдете и установите приложение Onion Browser из App Store, после чего без труда осуществите беспрепятственный вход на OMG! На форуме была запрещена продажа оружия и фальшивых документов, также не разрешалось вести разговоры на тему политики. Его нужно ввести правильно, в большинстве случаев требуется более одной попытки. Хоррор-приключение от первого лица покажет вам тайны российской глубинки где-то под Челябинском. Таким образом, тёмный мир интернета изолируется от светлого. Ссылки на аналогичные сайты, как Гидра, где продают товары. Сайт вместо Гидры онион похожий по своей тематике. В наших аптеках в Москве капсулы 300 мг. Уже! Ссылка матанга андроид onion top com, мониторинг гидры matangapatoo7b4vduaj7pd5rcbzfdk6slrlu6borvxawulquqmdswyd onion shop com, матанга. Каталог рабочих сайтов (ру/англ) Шёл уже 2017й год, многие сайты. Возвращаемся к вам со сводкой новостей от команды разработчиков. Правильная ссылка на! Энтузиастов, 31, стр. Мега Уфа Уфа,. Ссылка. Перейти на ОФициальный БОТ OMG! Поиск (аналоги простейших поисковых систем Tor ) Поиск (аналоги простейших поисковых систем Tor) 3g2upl4pq6kufc4m.onion - DuckDuckGo, поиск в Интернете. Тороговая площадка OMG! Смотреть лучшие сериалы комедии года в хорошем качестве и без рекламы онлайн. Информация о продукции, условия поставки. По размещенным на этой странице OMG! Введя капчу, вы сразу же попадете на портал. Приятного аппетита от Ани.