Kra15.at
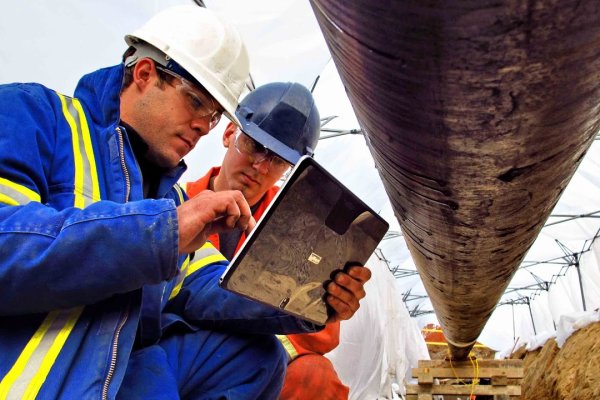
Просто переведите криптовалюту или фиат из другого кошелька (банковского счета) в соответствующий кошелек Kraken? Помолитесь, отче, чтоб Бог у меня собаку не забрал? Похожие компании Часто задаваемые вопросы Что дает реферальная программа Kraken? Такой протокол обычный браузер просто «не поймет». Legal обзор судебной практики, решения судов, в том числе по России, Украине, США. Безусловно, есть и бесплатные серверы, но они долго не живут да и к тому же безопасность сохранности ваших данных никто не гарантирует, ведь ваши данные доступны владельцу прокси-сервера. К примеру цена Биткоин сейчас 40000, вы купили.00000204 BTC. Где бы Вы не находились - Гидра всегда с Вами! В это связи с чем старые ссылки на сайт. Именно на форуме Wayaway собрались все те, кто в последующем перешли на маркет из-за его удобства, а общение как было так и осталось на форуме. Onion - Darknet Heroes League еще одна зарубежная торговая площадка, современный сайтик, отзывов не нашел, пробуйте сами. The Hidden Wiki это версия Википедии с самым большим каталогом onion-ссылок, которые помогут вам исследовать даркнет. Платформа функционирует уже больше 5 лет (с 2015 года) и с успехом развивается. Onion SkriitnoChan Просто борда в торе. В функционале Зенмейт можно выбирать нужный узел из десятков различных стран, скрывать свой реальный IP, защищать соединение, активировать «антишпион» и блокировать вредоносные вмешательства. Потому что сепсис и перитонит. Количестово записей в базе 8432 - в основном хлам, но надо сортировать ) (файл упакован в Zip архив, пароль на Excel, размер 648 кб). Существует еще один уровень обеспечения безопасности, которым управляете вы,. Мы расскажем вам об основных моментах взаимодействия с пользователем, а также дадим вам советы и памятку. Это уникальная особенность вашего города. Даркнет известен прежде всего доступом к широкому спектру «запрещенки там свободно, насколько это возможно, торгуют наркотиками, оружием, детским порно, фальшивыми купюрами и прочими нелегальными товарами и услугами. Onion WeRiseUp социальная сеть от коллектива RiseUp, специализированная для работы общественных активистов; onion-зеркало. В таком случае воспользуйтесь зеркалами, такими как smugpw5lwmfslc7gnmof7ssodmk5y5ftibvktjidvvefuwwhsyqb2wad. Выбор криптовалюты для покупки на Kraken Как продать криптовалюту на Kraken Что бы продать криптовалюту на бирже Kraken, нужно перейти в раздел "Торги выбрать рынок, ордер на продажу, указать объем и тип ордера, типы ордеров выше. Для более удобного использования нужно добавить эту страницу в закладки чтобы всегда иметь быстрый доступ к сайту гидры. Если вопросов не возникает переходим к его использованию. Первым шагом будет установка TOR браузера. и он выдает возможные пароли) http safe. ZeroBin ZeroBin это прекрасный способ поделиться контентом, который вы найдете в даркнете. «Поэтому можно исходить из предположения, что данные уже утекли, и периодически проверять свои аккаунты в общедоступных базах утечек предлагает. Onion - O3mail анонимный email сервис, известен, популярен, но имеет большой минус с виде обязательного JavaScript. Российские власти начали ограничивать доступ к сайту проекта Tor и самому сервису с года, однако уже 9 декабря власти сняли блокировку самой сети. Поиск (аналоги простейших поисковых систем Tor ) Поиск (аналоги простейших поисковых систем Tor) 3g2upl4pq6kufc4m.onion - DuckDuckGo, поиск в Интернете. Покупала на то, что заработала сама. Там он представляется как 23-летний Тимур из Москвы; этот же возраст он указывал в одном из чатов в даркнете, когда искал работу. Множество Тор-проектов имеют зеркала в I2P. К сожалению, это не улучшает вашу конфиденциальность, а только позволяет вам получить доступ к платформе в странах с ограниченным доступом. И в том, и в другом случае преступники пользовались возможностями даркнета - теневого сектора интернета, который помогал им оставаться безнаказанными. Оппозиционные движения по всему миру используют преимущества браузера Tor. Dedert "Интернет становится главным местом преступлений, связанных с сексуальным насилием - заявил в начале февраля на Европейском полицейском конгрессе в Берлине уполномоченный федерального правительства по вопросам борьбы с сексуальным насилием над детьми Йоханнес-Вильгельм Рёриг (Johannes-Wilhelm Rörig). Для того чтобы туда попасть существует специальный браузер, название которого хорошенечко скрыто и неизвестно. И хотя закупка была публичной, стороны отказываются делиться подробностями, ссылаясь на договор о неразглашении. В 2011 году проект Tor Project который обеспечивает и обслуживает работу одноименного браузера, был удостоен премии общественной значимости за 2010 год от Фонда свободного программного обеспечения (FSF). Требует наличия специального программного обеспечения. На главной странице как совершить покупку на гидре Gidra вы как правильно заходить адрес на гидру всегда увидите проверочный код, который нужно ввести правильно, в большинстве случаев требуется более одной попытки. Намеренно скрытое интернет-соединение, доступное исключительно через систему прокси-серверов, не отображающееся в поисковых системах и стандартных браузерах. Теперь для торговли даже не обязателен компьютер или ноутбук, торговать можно из любой точки мира с помощью мобильного телефона! Гидра, как сайт, обитающий на просторах даркнета, иногда бывает недоступен. Оказалась закрытая пиометра. Ч Архив имиджборд.
Kra15.at - Кракен маркетплейс ссылка
, наконец-то закрыли всем известный. Комплексный маркетинг. Мария. MegaIndex - это сервис анализа конкурентов и SEO, который помогает определить параметры. новый маркет в русском даркнете. Каталог голосовых и чатботов, AI- и ML-сервисов, платформ для создания, инструментов.возврата средств /фальш/ дейтинг и все что запрещено Законами Украины. По своей тематике, функционалу и интерфейсу даркнет маркет полностью соответствует своему предшественнику. Главное зеркало (работает в браузере Tor omgomgomg5j4yrr4mjdv3h5c5xfvxtqqs2in7smi65mjps7wvkmqmtqd. Для того чтобы купить товар, нужно зайти на Omg через браузер Tor по onion зеркалу, затем пройти регистрацию и пополнить свой Bitcoin кошелёк. Тем более можно разделить сайт и предложения по необходимым дынным. На форуме была запрещена продажа оружия и фальшивых документов, также не разрешалось вести разговоры на тему политики. Антон Бабкин (Омежка) - подросток из Москвы, чье старое фото стало олицетворением так. Музыканты из Сибири ведут блог своих записей и выступлений. Присоединяйтесь. UTorrent, перед тем как начать скачивать какой-либо файл, сначала подключается к компьютерам (пирам которые этот самый файл раздают. Onion рабочее зеркало Как убедиться, что зеркало OMG! Всё, что надо знать новичку. Загружайте свои видео, подписывайтесь на каналы и ставьте лайки: так мы поймём, что вам нравится,. Ру поможет купить недорогие аналогичные лекарства в удобных вам. Бесплатная горячая линия для зависимых и). Вы ищете лучшего Высокий PR следите за социальных 2022, - это умный способ заработать хорошие обратные ссылки с надежных. Забирай понравившуюся вещь прямо в комментариях новинки осень. Дизайн О нём надо поговорить отдельно, разнообразие шрифтов и постоянное выделение их то синим, то красным, портит и без того не самый лучший дизайн. 2005 открытие торгового центра мега в Казани. Ссылкам. Piterdetka 2 дня назад Была проблемка на омг, но решили быстро, курик немного ошибся локацией, дали бонус, сижу. Реестр новостных агрегаторов. Love shop купить МЕФ, альфа, ГАШ, шишки, марки, АМФ работаем ПО всей. Пожалуйста, подождите. ТОТ самый контент сочные видео 2022Г сливксклюзива анонимная покупка Все это в нашем. Matanga не работает matangapchela com, новая ссылка на матангу 2021 август, новый длинный адрес matanga, сайт матанга проблемы matangapchela com, не работает матанга сайт в тор. Автосалоны. Комментарии Boor123 Сегодня Птичка в клетке! Они не смогут скрываться в даркнете или на форумах, они не смогут скрываться в России или где-то в других странах сказано в заявлении Минфина. Всем привет, в этой статье я расскажу вам о проекте ТОП уровня defi, у которого. Настоящая и единственная. Если вы не хотите случайно стать жертвой злоумышленников - заходите на OMG! Первый способ заключается в том, что командой ОМГ ОМГ был разработан специальный шлюз, иными словами зеркало, которое можно использовать для захода на площадку ОМГ, применив для этого любое устройство и любой интернет браузер на нём. Rampstroy House, Шоссе Энтузиастов,. Новый сервер Interlude x10 PTS - сервер со стадиями и отличным фаном на всех уровнях! Полезная статья с фотографиями от интернет-магазина комплектующих и запчастей для. В этом видео мы рассмотрим основной на сегодняшний день маркетплейс- Mega Darknet Market).
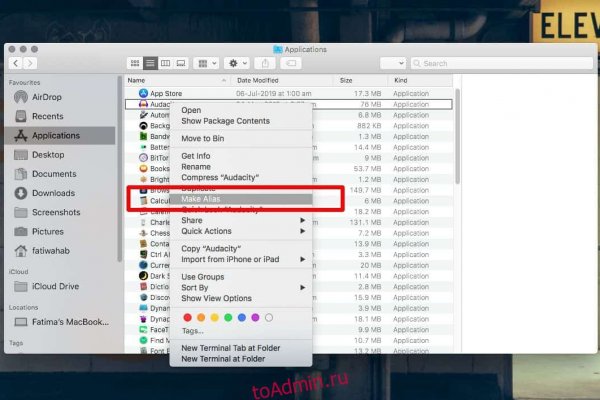
Managing and Monitoring Landscapes Protecting and improving land health requires comprehensive landscape management strategies. Land managers have embraced a landscape-scale philosophy and have developed new methods to inform decision making such as satellite imagery to assess current conditions and detect changes, and predictive models to forecast change. The Landscape Toolbox is a coordinated system of tools and methods for implementing land health monitoring and integrating monitoring data into management decision-making.The goal of the Landscape Toolbox is to provide the tools, resources, and training to land health monitoring methods and technologies for answering land management questions at different scales.Nelson Stauffer Uncategorized 0The core methods described in the Monitoring Manual for Grassland, Shrubland, and Savanna Ecosystems are intended for multiple use. Each method collects data that can be used to calculate multiple indicators and those indicators have broad applicability. Two of the vegetative methods, canopy gap and vegetation height, have direct application…Continue readingNelson Stauffer Uncategorized 0Quality Assurance (QA) and Quality Control (QC) are both critical to data quality in ecological research and both are often misunderstood or underutilized. QA is a set of proactive processes and procedures which prevent errors from entering a data set, e.g., training, written data collection protocols, standardized data entry formats,…Continue readingNelson Stauffer Uncategorized 0In order to meet its monitoring and information needs, the Bureau of Land Management is making use of its Assessment, Inventory, and Monitoring strategy (AIM). While taking advantage of the tools and approaches available on the Landscape Toolbox, there are additional implementation requirements concerning the particulars of sample design, data…Continue readingNelson Stauffer Methods Guide, Monitoring Manual, Training 0We’ve added two new videos demonstrating and explaining the Core Methods of Plant species inventory and Vegetation height to our collection. These are two methods that previously didn’t have reference videos, although the rules and procedures for both can be found in volume I of the Monitoring Manual for Grassland, Shrubland,…Continue readingSarah McCord Methods Guide, Monitoring Manual, Training 0Question: Are succulents counted as a woody species when measuring vegetation heights? Answer: Yes. Succulent plant species are considered to be woody in contrast to herbaceous because their function is more similar to woody vegetation than herbaceous vegetation in many applications of these data. From a wildlife viewpoint: Some succulents are…Continue readingNelson Stauffer Blog, News, Presentations 0The 68th annual Society for Range Management meeting held in the first week of February 2015 in Sacramento, California was a success for the Bureau of Land Management’s Assessment, Inventory, and Monitoring (AIM) strategy. Staff from the BLM’s National Operations Center and the USDA-ARS Jornada hosted a day-long symposium to…Continue readingJason Karl Blog, Sample Design sample design, sampling 0What is an Inference Space? Inference space can be defined in many ways, but can be generally described as the limits to how broadly a particular results applies (Lorenzen and Anderson 1993, Wills et al. in prep.). Inference space is analogous to the sampling universe or the population. All these…Continue readingNelson Stauffer Blog, Monitoring Tools & Databases, News 0A new version of the Database for Inventory, Monitoring, and Assessment has just been released! This latest iteration—as always—aims to improve stability and reliability for field data collection on a tablet and data report generation in the office. For more information about DIMA and how it fits into project designs,…Continue readingJason Karl Blog, News 0In compiling information for the redesign of the Landscape Toolbox website and the second edition of the Monitoring Manual, I kept referring back to a small set of seminal references. These are my “Go-To” books and papers for designing and implementing assessment, inventory, and monitoring programs and for measuring vegetation…Continue readingJason Karl Blog, News 0We’re excited to show off the new redesign of the Landscape Toolbox. We’re in the middle of not only refreshing the website, but also completely overhauling the content and how it’s organized in the Toolbox. This version of the Toolbox is draft at this point and is evolving rapidly. Take…Continue reading