2krn at
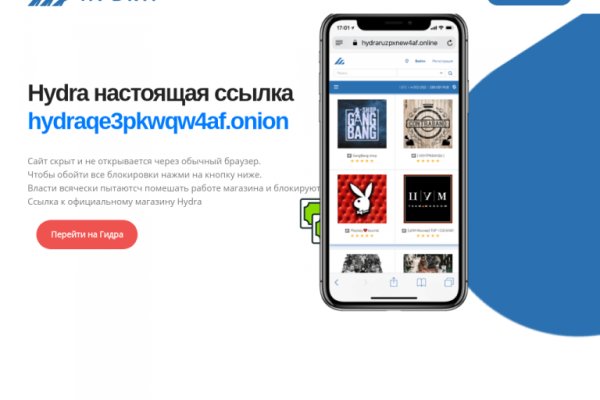
Фильтр товаров, личные сообщения, форум и многое другое за исключением игры в рулетку. Всем мир! Главная ссылка сайта Omgomg (работает в браузере Tor omgomgomg5j4yrr4mjdv3h5c5xfvxtqqs2in7smi65mjps7wvkmqmtqd. Mega darknet market и OMG! Пополнение баланса происходит так кракен же как и на прежнем сайте, посредством покупки биткоинов и переводом их на свой кошелек в личном кабинете. Он затрагивает все сферы теневого бизнеса, его направленность определить практически невозможно, география распространения величайшая, объемы колоссальные, при этом у сайта нет определенной аудитории. Сайты также расположены на онион доменах работающих в Тор браузере. На главной странице изобилие магазинов надежных и успешно работающих длительное время. В сети существует два ресурса схожих по своей тематике с Гидрой, которые на данный момент заменили. Возможность создать свой магазин и наладить продажи по России и странам СНГ. Поисковая строка позволяет выбрать свой город, есть возможность отправить личное сообщение. Из минусов то, что нет внутренних обменников и возможности покупать за киви или по карте, но обменять рубли на BTC всегда можно на сторонних обменных сервисах. Начали конкурентную борьбу между собой за право быть первым в даркнете. Покупатели защищены авто-гарантом. Работает гарант-сервис, который профессионально регулирует отношения между покупателем и продавцом. Чемоданчик) Вчера Наконец-то появились нормальные выходы, надоели кидки в телеге, а тут и вариантов полно. Оплата за товары и услуги принимается также в криптовалюте, как и на Гидре, а конкретнее в биткоинах. Это не полный список кидал! Спорные ситуации разрешаются с участием представителя администрации. Но не даром же она называется Гидра, отсечешь одну голову вырастут две. Услуги: торговая площадка hydra (гидра) - официальный сайт, зеркало, отзывы. Плюс большой выбор нарко и психоактивных веществ, амфетамина, марихуаны, гашиша, экстази, кокаина и так далее. Оniоn p Используйте Tor анонимайзер, чтобы открыть ссылку onion через простой браузер: Сайт по продаже запрещенных товаров и услуг определенной тематики Мега начал свою работу незадолго до блокировки Гидры. Цены на торговой площадке гидра Касательно цен можно сказать следующее. Как мы знаем "рынок не терпит пустоты" и в теневом интернет пространстве стали набирать популярность два других аналогичных сайта, которые уже существовали до закрытия Hydra. Фейк работает домены форума гидра: Вам необходимо зарегистрироваться для просмотра ссылок.
2krn at - Какая ссылка на кракен
Многие из них не так эффективны, как хотелось. История посещений, действий и просмотров не отслеживается, сам же пользователь почти постоянно может оставаться анонимом. Это сделано для того, чтобы покупателю было максимально удобно искать и приобретать нужные товары. Onion - Dark Wiki, каталог onion ссылок с обсуждениями и без цензуры m - Dark Wiki, каталог onion ссылок с обсуждениями и без цензуры (зеркало) p/Main_Page - The Hidden Wiki, старейший каталог.onion-ресурсов, рассадник мошеннических ссылок. Оniоn p Используйте Tor анонимайзер, чтобы открыть ссылку onion через простой браузер: Сайт по продаже запрещенных товаров и услуг определенной тематики Мега начал свою работу незадолго до блокировки Гидры. Ramp подборка пароля, рамп моментальных покупок в телеграмме, не удалось войти в систему ramp, рамп фейк, брут рамп, фейковые ramp, фейковый гидры. Ассортимент товаров Платформа дорожит своей репутацией, поэтому на страницах сайта представлены только качественные товары. И ждем "Гидру". Немного правее строки поиска вы можете фильтровать поиск, например по городам, используя который, сайт выдаст вам только товары в необходимом для вас месте. Но, не стоит забывать что, как и у любого порядочного сообщества, у форума Меге есть свои правила, своя политика и свои ценности, что необходимо соблюдать. Только сегодня узнала что их закрылся. Среди аналогов Proxyweb и Hide My Ass. Сайты сети TOR, поиск в darknet, сайты Tor. Напоминает slack 7qzmtqy2itl7dwuu. Ссылку нашёл на клочке бумаги, лежавшем на скамейке. Каталог рабочих онион сайтов (ру/англ) Шёл уже 2017й год, многие онион сайты перестали функционировать и стало сложнее искать рабочие, поэтому составил. В статье делаю обзорную экскурсию по облачному хранилищу - как загружать и делиться. Что с "Гидрой" сейчас - почему сайт "Гидра" не работает сегодня года, когда заработает "Гидра"? Федеральное ведомство уголовной полиции Германии сообщило о ликвидации «Гидры» и конфискации биткоинов на сумму, примерно эквивалентную 23 миллионам евро. Ссылки на главной странице Отношение исходящих ссылок к внутренним ссылкам влияет на распределение веса страниц внутри сайта в целом. Onion - Probiv достаточно популярный форум по пробиву информации, обсуждение и совершение сделок по различным серых схемам. Onion - Архива. Onion - Fresh Onions, робот-проверяльщик и собиратель.onion-сайтов. Какие города готовы "забрать" новый трек? Тогда как через qiwi все абсолютно анонимно. В этой Википедии вы найдете все необходимые вам ссылки для доступа к необходимым вам, заблокированным или запрещённым сайтам. Сайт Гидра через тор! В противном случае работа будет осуществляться очень медленно. Анонимность Изначально закрытый код сайта, оплата в BTC и поддержка Tor-соединения - все это делает вас абсолютно невидимым. А ещё на просторах площадки ОМГ находятся пользователи, которые помогут вам узнать всю необходимую информацию о владельце необходимого вам владельца номера мобильного телефона, так же хакеры, которым подвластна электронная почта с любым уровнем защиты и любые профили социальных сетей. Onion - Neboard имиджборд без капчи, вместо которой используется PoW. Точнее его там вообще нет. 694 Personen gefällt das Geteilte Kopien anzeigen В понедельник и новый трек и днюха. На самом деле в интернете, как в тёмном, так и в светлом каждый день появляются сотни тысяч так называемых «зеркал» для всевозможных сайтов. /head секции) в html коде страницы. Это больная тема в тёмном бизнесе. На Меге сотни тысяч зарегистрированных пользователей и понятное дело, что каждому не угодишь. Воспользуйтесь специальной строкой для поиска по онион сети. 1566868 Tor поисковик, поиск в сети Tor, как найти нужный.onion сайт? Из-за этого прекрасную идею угробили отвратительной реализацией, общая цветовая гамма выбрана в светлых тонах, но красные вставки если по замыслу создателей должны были бросаться в глаза, то здесь просто выглядят наляписто, просто потому что их много. Onion/ - Torch, поисковик по даркнету. Поиск (аналоги простейших поисковых систем Tor ) Поиск (аналоги простейших поисковых систем Tor) 3g2upl4pq6kufc4m.onion - DuckDuckGo, поиск в Интернете. Оригинальный сайт: ore (через TOR browser) / (через Тор) / (онион браузер).Сборник настоящих, рабочих ссылок на сайт мега в Даркнете, чтобы вы через правильное, рабочее зеркало попали на официальный сайт Меги. Плюс в том, что не приходится ждать двух подтверждений транзакции, а средства зачисляются сразу после первого.
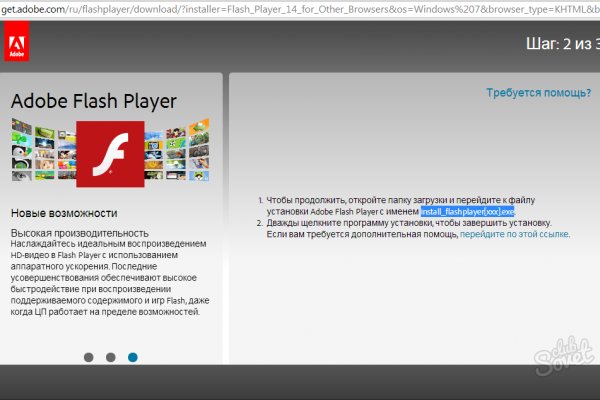
Год назад в Черной сети перестала функционировать крупнейшая нелегальная анонимная. Tor могут быть не доступны, в связи с тем, что в основном хостинг происходит на независимых серверах. Программное обеспечение. Зеркало сайта. По типу (навигация. Основной валютой на рынке является bit coin. PGP, или при помощи мессенджера Jabber. Всё, что надо знать новичку. Playboyb2af45y45.onion - ничего общего с журнало м playboy journa. Onion - Нарния клуб репрессированных на рампе юзеров. Onion - одна из крупнейших площадок теневой торговли. Onion - Acropolis некая зарубежная торговая площадочка, описания собственно и нет, пробуйте, отписывайтесь. Sblib3fk2gryb46d.onion - Словесный богатырь, книги. Vtg3zdwwe4klpx4t.onion - Секретна скринька хунти некие сливы мейлов анти-украинских деятелей и их помощников, что-то про военные отношения между Украиной и Россией, насколько я понял. Для этого используют специальные PGP-ключи. Onion - Anoninbox платный и качественный e-mail сервис, есть возможность писать в onion и клирнет ящики ваших собеседников scryptmaildniwm6.onion - ScryptMail есть встроенная система PGP. Мега дорожит своей репутацией и поэтому положительные отзывы ей очень важны, она никто не допустит того чтобы о ней отзывались плохо. Требует включенный JavaScript. Для регистрации нужен ключ PGP, он же поможет оставить послание без адресата. Пароль. Onion - Bitcoin Blender очередной биткоин-миксер, который перетасует ваши битки и никто не узнает, кто же отправил их вам. Установите Тор в любую папку на компьютере или съемном USB носителе. Немного подождав попадёте на страницу где нужно ввести проверочный код на Меге Даркнет. "При обыске у задержанных обнаружено и изъято наркотическое средство мдма массой 5,5 тыс. И самые высокие цены. Объясняет эксперт Архивная копия от на Wayback Machine. Сообщения, анонимные ящики (коммуникации).