Регистрация кракен
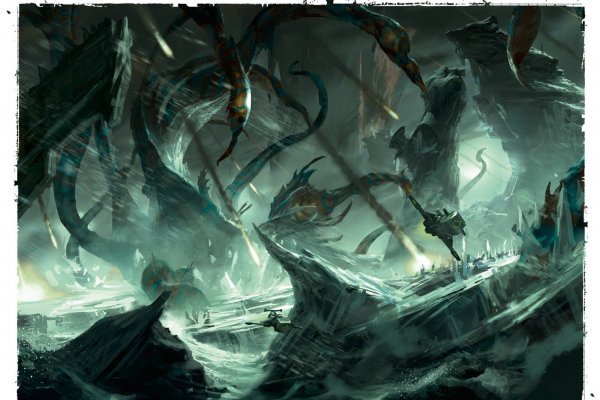
Не можете войти на сайт мега? Торрент трекеры, Библиотеки, архивы Торрент трекеры, библиотеки, архивы rutorc6mqdinc4cz. Это работает не только на просторах ОМГ ОМГ, но и так krn же на других заблокированных сайтах. Данное количество может быть как гарантия от магазина. На iOS он сначала предлагает пройти регистрацию, подтвердить электронную почту, установить профиль с настройками VPN, включить его профиль в опциях iOS и только после этого начать работу. Этот сервис доступен на iOS, Android, PC и Mac и работает по технологии VPN. Wired, его вдохновил успех американской торговой площадки. Хостинг изображений, сайтов и прочего Tor. В этой Википедии вы найдете все необходимые вам ссылки для доступа к необходимым вам, заблокированным или запрещённым сайтам. Onion - The Pirate Bay,.onion зеркало торрент-трекера, скачивание без регистрации. Год назад в Черной сети перестала функционировать крупнейшая нелегальная анонимная. Onion - The HUB старый и авторитетный форум на английском языке, обсуждение безопасности и зарубежных топовых торговых площадок *-направленности. В ТОР. Сеть для начинающих. Всем известный браузер. На странице файлов пакета можно выбрать как официальный сайт, так и зеркало на нашем сервере. Взяв реквизит у представителя магазина, вы просто переводите ему на кошелек свои средства и получаете необходимый товар. Является зеркалом сайта fo в скрытой сети, проверен временем и bitcoin-сообществом. Такой глобальный сайт как ОМГ не имеет аналогов в мире. Если для вас главное цена, то выбирайте в списке любой, а если для вас в приоритете место товара и вы не хотите тратить много времени тогда выбирайте вариант моментальной покупки. Вот и пришло время приступить к самому интересному поговорить о том, как же совершить покупку на сайте Меге. Показало себя заметно хуже. Этот сайт упоминается в онлайн доске заметок Pinterest 0 раз. Мегастрой. Отдельной строкой стоит упомянуть и сервис Vemeo, который, как и TunnelBear, присутствует на всех основных платформах, однако стоит 3,95 доллара в месяц, так что его трудно рекомендовать для любительского использования. Это сделано для того, чтобы покупателю было максимально удобно искать и приобретать нужные товары. Читайте также: Очистка мака от ненужных файлов. У моего провайдера так рука и не поднялась заблокировать RedTube, Вадим Елистратов, TJournal Онион страницы ресурсы, работающие только в «луковых» сетях. Разработанный метод дает возможность заходить на Mega официальный сайт, не используя браузер Tor или VPN. Что-то про аниме-картинки пок-пок-пок. Т.е. Rospravjmnxyxlu3.onion - РосПравосудие российская судебная практика, самая обширная БД, 100 млн. История посещений, действий и просмотров не отслеживается, сам же пользователь почти постоянно может оставаться анонимом. Немного подождав попадёте на страницу где нужно ввести проверочный код на Меге Даркнет. Foggeddriztrcar2.onion - Bitcoin Fog микс-сервис для очистки биткоинов, наиболее старый и проверенный, хотя кое-где попадаются отзывы, что это скам и очищенные биткоины так и не при приходят их владельцам. Это не полный список кидал! Как попасть на russian anonymous marketplace? Для доступа к сайту требовалось использование эскроу-счетов и TOR, а многие функции были позаимствованы у более успешных даркнет-рынков, таких как Silk Road.
Регистрация кракен - Зеркало вход кракен
ОМГ – один из самых крупных даркмаркетов, широкая платформа, дающая возможность любому посетителю реальность покупать неразрешенный товар либо воспользоваться услугой, найти которую в открытом доступе почти нереально. На интернет-портале находится огромное число online магазинов. Надо детальнее выучить, что представляет собой площадка и для чего необходим пользователям Гидры интернет-браузер Tor.Обзор на ГидруОМГ сайт – это большая платформа, на необъятных просторах которой всякий подыщет для себя нужную вещь либо услугу, о которой прежде мечтал. Реализацией изделий заняты специальные торговые центры, действующие круглые сутки и с завидной постоянностью обновляющие и так объемистый ассортимент. Особо можно заметить, что интернет-проект предоставляет услуги транспортировки купленного продукта.Оформление заявки не требует большое количество времени. В общем доступе расположены рецензии заказчиков, уже пользовавшихся работой конкретного магазина. В связи с этим возможный заказчик сможет предварительно прочитать их и выяснить о качестве продукции, тонкостях сотрудничества с продавцом.Особенность omgbuiwftrzuqy.onion сайта – наличие службы секретных клиентов. Политика, какую они проводят, помогает увеличить уверенность клиентов. Оказывается скрытые клиенты покупают разные товары и делают их тест, в том числе и химический. Если товар не подходит конкретным условиям, значит продавец, у которого был куплен товар, заблокируются системой, а его товар пропадает с онлайн прилавков.Транспортировка заказа производится в режиме закладки. Кладмен приезжает по обозначенному заказчиком местоположению и прячет предмет торговли, после чего посылает его координаты. Оплату покупатель имеет право осуществить только лишь когда станет взят товар, и конечно выполнена оценка его качества. При появлении проблем с качественными характеристиками или транспортировкой заказчик сможет открыть спор.Главная валюта Гидры – биткоин. Превосходством подобной валюты является анонимность электронных активов, в связи с чем все организуемые на ресурсе операции с денежными средствами защищены. Определенные он-лайн магазины готовы взять в оплату QIWI-рубли.Наши советы начинающим покупателямЧтобы в ходе приобретений не появилось никаких затруднений, потребителю нужно принять к сведению ряд рекомендаций:Перед покупкой важно смотреть отзывы о приобретаемой услуге либо изделии. Это поможет заранее выяснить о качественных характеристиках продукции, спецификах магазина, нюансах доставки. Рецензии располагаются в общем доступе.Плату предпочтительнее производить после того как приняли заказ. Только в этом случае у клиента окажется способность вернуть средства при обнаружении плохого качества продукта.В том случае, если покупателю пришлась по нраву услуга или он выдал оценку изделию, надо написать отзыв. Это обязательно поможет прочим клиентами Гидры сделать правильный выбор.Модераторы платформы также рекомендуют использовать ранее нигде не задействованные логины и пароли во время регистрирования своего аккаунта.Tor – браузер для ГидрыОсобый браузер Tor позволит гостям портала беспрепятственно войти на официальный интернет-сайт, предоставляя ссылку на омг сайт. Достоинством платформы стало присутствие принципа «луковичной маршрутизации», именно благодаря какой вход Гидры, а также совершение каких-то операций на площадке будет оставаться анонимным и безопасным для обеих сторон.Для того, чтобы установить Тор, потребуется:Перейти на сайт.Закачать архив.Открыть в архиве файл с расширением exe.Выбрать папку и язык установки.Дожидаться окончания операции.После чего останется только запустить браузер и ввести в поисковую строку подходящий запрос. По основной ссылке на Гидру и можно попасть на официальный сайт даркмаркета. Абоненту надо будет перейти на нее, для того, чтобы приступить к покупкам.Каким способом завести учётку на Гидре?Для того, чтобы пребывать на сайте официально и проплачивать изделия и сервисы портала, клиенту Гидры нужно создать личный аккаунт. Для этой цели ему потребуется:Перейти в раздел регистрации на сервисе ОМГ.Выдумать логин и пароль задуманного аккаунта. Модераторы вебсайта рекомендуют применить ранее нигде не задействованные сведения.Подтвердить пароль, введя его еще раз.Засвидетельствовать прохождение регистрации.После завершения вышеуказанного клиенту откроется вход в личный кабинет, где у него есть возможность иметь сведения о состоянии заявки, проплачивать товары либо устанавливать связь с дирекцией проекта.Баланс на Гидре – каким образом пополнить?Для проплаты закупок нужно будет дополнить счет собственного кошелька. Чтобы это осуществить, нужно сначала купить особый фиат, потом за него приобрести биткоин – главную валюту системы. Потом останется только лишь перебросить биткоин в кошель, и станет возможно покупать товары или сервисы.Приобрести фиат можно работая в режиме online на специальном ресурсе или в ближнем месте обмена. Доскональную информацию по вопросу, как покупать валюту, а также в каком месте это делают, можно получить, сделав мониторинг обмена криптовалют.Когда фиат обменяете на необходимое число биткоинов, понадобится выполнить перечисление криптовалюты в игру. Сделать это можно двумя вариантами:Используя цифровую денежную систему, в частности, QIWI. Для того, чтобы произвести перевод, нужно скопировать номер электронного кошелька и определить величину перевода. Остальное система проделает самостоятельно.Используя пункт обмена на Гидре. Требуется указать кошелек, где располагаются биткоины и подтвердить выполнение действия.Фактически, технология перевода биткоина не представляет из себя ничего сложного.Как отыскать доступную ссылку на гидру?Поскольку ОМГ выполняет свою деятельность нелегально, торгуя нелегальными веществами и предлагая запрещенные сервисы, отыскать ее быстро не удастся. Выполнить это сможете с применением интернет-браузера Tor. Дополнительно создатели портала настоятельно рекомендуют сохранить официальную страничку даркмаркета в закладки браузера, чтобы было можно всегда зайти на измененный доменный интернет-адрес ссылку на omg зеркало. Изменение адреса объясняется тем, что главный портал частенько блокируют.
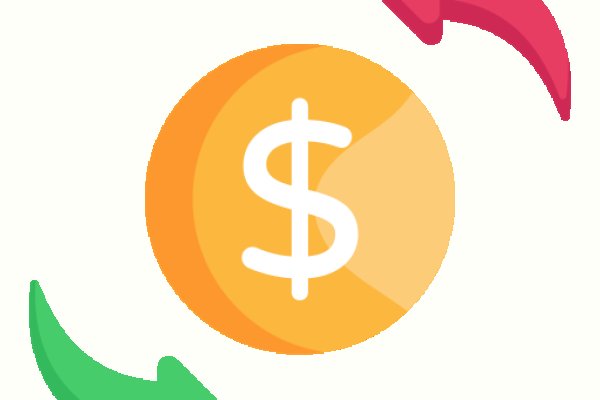
Безопасность Госрегулирование Бизнес Интернет E-commerce Веб-сервисы ТехникаНемецкие силовики остановили деятельность «Гидры» - самого известного русскоязычного даркнет-магазина по продаже наркотиков. Они выключили его серверы в Германии и изъяли крупную сумму в биткоинах. Расследование против «Гидры» длилось с августа 2021 г. при участии властей США.Немцы победили русскую «Гидру»Немецкие правоохранительные органы сообщили о закрытии сети серверов русскоязычного даркнет-маркета omg, расположенной на территории Германии. Разгромить сервис удалось специалистам Федерального управления уголовной полиции Германии.omg представляет собой крупнейший российский даркнет-рынок по торговле наркотиками. В российском сегменте интернета он широко известен под названием «ОМГ».Отключив серверы маркета, немецкие силовики также изъяли и крупную сумму в криптовалюте. По информации Управления, было конфисковано 543 биткоина. На 15:00 5 апреля 2022 г. по Москве это составляло около $25,347 млн (данные CoinDesk).Вернется ли «ОМГ» к работе после сокрушительного удара Германии, пока неизвестноПо данным следствия, «ОМГ» была нелегальной торговой площадкой с самым высоким оборотом в мире. За один только 2020 г. через нее были осуществлены продажи на общую сумму не менее 1,23 миллиарда евро. Часть денег «ОМГ» и ее пользователи выводили через специализированные криптообменники для отмывания криминальных денег, в том числе и через российский SUEX. Он был основан в 2018 г., и к сентябрю 2021 г. через него прошло более $20 млн от «Гидры». В сентябре 2021 г. Минфин США ввело против него санкции.Без немецких серверов «ОМГ» не живетВ операции против «Гидры» также принимали участие сотрудники Генпрокуратуры Франкфурта-на-Майне и Центрального управления Германии по борьбе с интернет-преступностью. На момент публикации материала не было известно, есть ли в распоряжении «Гидры» сеть серверов за пределами Германии, однако немецкие силовики утверждают, что их действия привели к полной остановке работы ресурса.По информации Telegram-канала Baza, доступ к ресурсу в даркнете действительно закрыт. Однако его владельцы утверждают, что это связано с некими техническими работами.США и Германия объединилисьОперация немецких силовиков – это итог расследования Германии, инициированного в августе 2021 г. Другими словами, на уничтожение столь крупного ресурса им потребовалось всего восемь месяцев.«Заглушка» на даркнет-сайте «Гидры»Однако нельзя не отметить, что в расследовании принимали участие и некоторые органы власти США. Это подтвердили представители Федерального управления уголовной полиции Германии, но как именно американская сторона повлияла на ход расследования, и кем именно она была представлена, они уточнять не стали.В итоге, после закрытия «Гидры» немецкие силовики приступили к следующей фазе операции. Они пытаются вычислить операторов и администраторов ресурса, чтобы предъявить им обвинения в распространении наркотиков и отмывании денег. На 5 марта 2022 г. их личности установлены не были.Пользователи под угрозой деанонимизацииКак показало германо-американское расследование, «ОМГ» функционировала в течение как минимум семи лет. Ресурс был доступен через сеть Tor, по меньшей мере, с 2015 г. и занимался не только посредничеством при продаже наркотиков.Модуль «Управление уязвимостями» на платформе Security Vision: как выявить и устранить уязвимости в своей ИТ-инфраструктуреБезопасностьЧерез этот даркнет-сайт также велась продажа персональных данных и поддельных документов, говорится в сообщении немецких силовиков. В ходе расследования выяснилось, что на «Гидре» было зарегистрировано свыше 17 млн пользователей со всего земного шара. Продавцов тоже было немало – более 19 тыс.Пока неясно, смогли ли следователи получить доступ к информации, способной указать им на реальных владельцев пользовательских профилей на «Гидре».Из даркнета уходят крупнейшие игрокиЗакрытие «Гидры» стало третьим ощутимым ударом по даркнету с начала 2022 г. «Темная сторона» всемирной Паутины постепенно лишается действительно крупных представителей.В январе 2022 г. работу прекратил рынок Monopoly Market, торгующий наркотиками. В том же месяце о своем закрытии объявил даркнет-ресурс UniCC, занимавшийся продажей ворованных кредитных карт. На момент выхода из бизнеса он контролировал 30% рынка краденных карт в даркнете.Но, в отличие от «Гидры», UniCC закрылся не из-за действий властей. Владельцы заявили, что просто устали заниматься всем этим (проект был основан в 2013 г.), и что они просто «уже немолоды». Однако у аналитиков иная точка зрения. Они полагают, что создатели боялись преследования властей и хотели сбежать со средствами пользователей.Давление властей – весьма вероятная причина закрытия UniCC. В течение всего 2021 г. из-за него даркнет лишился целого ряда ресурсов. Например, в июне 2021 г. Федеральное бюро расследований (ФБР) совместно с правоохранительными органами Германии, Нидерландов и Румынии добилось закрытия веб-магазина Slipp, торгующего украденными учетными данными.В октябре 2021 г. прекратил существование проект White House Market, вдохновленный культовым сериалом «Во все тяжкие» (Breaking Bad). Как и «ОМГ», он был связан с продажей запрещенных веществ.Эльяс Касми