Как оплатить заказ в кракене
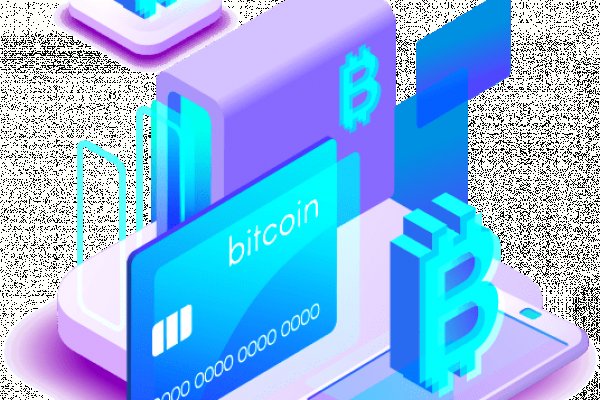
Onion - TorBox безопасный и анонимный email сервис с транспортировкой писем только внутри TOR, без возможности соединения с клирнетом zsolxunfmbfuq7wf. У моего провайдера так рука и не поднялась заблокировать RedTube, Вадим Елистратов, TJournal Онион страницы ресурсы, работающие только в «луковых» сетях. Подборка Обменников BetaChange (Telegram) Перейти. Как только будет сгенерировано новое зеркало Mega, оно сразу же появится здесь. Сайты со списками ссылок Tor. Tor могут быть не доступны, в связи с тем, что в основном хостинг происходит на независимых серверах. Есть закрытые площадки типа russian anonymous marketplace, но на данный момент ramp russian anonymous marketplace уже более 3 месяцев не доступна из за ддос атак. Es gibt derzeit keine Audiodateien in dieser Wiedergabeliste 20 Audiodateien Alle 20 Audiodateien anzeigen 249 Personen gefällt das Geteilte Kopien anzeigen Двое этих парней с района уже второй месяц держатся в "Пацанском плейлисте" на Яндекс онлайн Музыке. Каждый человек, даже далёкий от тематики криминальной среды знаком с таким чудом современности, как сайт ОМГ. Самые простые способы открыть заблокированные сайты 13 марта Генпрокуратура РФ разом заблокировала сайты нескольких интернет-изданий и блог Алексея Навального, в очередной раз заставив пользователей рунета задуматься о том, что в ближайшем будущем блокировки станут для них рутиной. Onion - Verified,.onion зеркало кардинг форума, стоимость регистрации. С какой-то стороны работа этих сайтов несет и положительную концепцию. If you have Telegram, you can view and join Найдено в даркнете right away. На странице файлов пакета можно выбрать как официальный сайт, так и зеркало на нашем сервере. Торрент трекеры, библиотеки, архивы. Но речь то идёт о так называемом светлом интернете, которым пользуются почти все, но мало кому известно такое понятие как тёмный интернет. Diasporaaqmjixh5.onion - Зеркало пода JoinDiaspora Зеркало крупнейшего пода распределенной соцсети diaspora в сети tor fncuwbiisyh6ak3i.onion - Keybase чат Чат kyebase. Onion - onelon, анонимные блоги без цензуры. Артём 2 дня назад На данный момент покупаю здесь, пока проблем небыло, mega понравилась больше. Подробнее можно прочитать на самом сайте. Несмотря на заглавные буквы на изображении, вводить символы можно строчными. Напоминает slack 7qzmtqy2itl7dwuu. Этот сайт упоминается в деловой социальной сети LinkedIn 0 раз. Всё что нужно: деньги, любые документы или услуги по взлому аккаунтов вы можете приобрести, не выходя из вашего дома. Годнотаба - список ссылок с onion зоны. Относительно стабилен. Onion - Lelantos секурный и платный email сервис с поддержкой SMTorP tt3j2x4k5ycaa5zt. Клёво12 Плохо Рейтинг.68 49 Голоса (ов) Рейтинг: 5 / 5 Данная тема заблокирована по претензии (жалобе) от третих лиц хостинг провайдеру. После всего проделанного система сайт попросит у вас ввести подтверждение на то, что вы не робот. Приложения для смартфонов Самым очевидным и самым простым решением для пользователей iPhone и iPad оказался браузер Onion, работающий через систему «луковой маршрутизации» Tor (The Onion Router трафик в которой почти невозможно отследить. А если уж решил играть в азартные игры с государством, то вопрос твоей поимки - лишь вопрос времени. Onion - форум подлодка, всё о спутниковом телевидении. Onion - Cockmail Электронная почта, xmpp и VPS. Всегда свежая ОМГ! Onion - Checker простенький сервис проверки доступности.onion URLов, проект от админчика Годнотабы.
Как оплатить заказ в кракене - Домен кракена
Большинство пользователей бесплатной версии хотели бы снять ограничение на скачивание. Исходя из данной информации можно сделать вывод, что попасть в нужную нам часть тёмного интернета не очень-то и сложно, всего лишь необходимо найти нужные нам ссылки, которые, кстати, все есть в специальной Википедии черного интернета. 99 руб. Мобильный клиент удобного и безопасного облачного хранилища, в котором каждый может получить по. Всегда свежая на! В Москве. Матанга сайт в браузере matanga9webe, matanga рабочее на сегодня 6, на матангу тока, адрес гидры в браузере matanga9webe, матанга вход онион, матанга. Сайт, дайте пожалуйста официальную на или зеркала чтобы зайти. Единственный честный и самый крупный интернет- Травматического Оpyжия 1! Комментарии Boor123 Сегодня Птичка в клетке! 9 часов. FK-: скейт парки и площадки для катания на роликах, самокатах, BMX. Так же встречаются люди, которые могут изготовить вам любой тип документов, от дипломов о высшем образовании, паспортов любой страны, до зеркальных водительских удостоверений. Hydra поддержка пользователей. Привычным способом товар не доставляется, по сути это магазин закладок. Вход Для входа на Омг (Omg) нужно правильно ввести пару логин-пароль, а затем разгадать капчу. Уводят аккаунт при обмене. Α-Пирролидинопентиофенон синтетический психостимулятор класса катинонов, представляет собой дезметиловый аналог пировалерона и представитель нового класса α-пирролидинофенонов (в который также входят, к примеру, mdpv, mppp, mdppp. Рассказываю и показываю действие крема Payot на жирной коже. Mega darknet market и OMG! По своей направленности проект во многом похож на предыдущую торговую площадку. Всё что нужно: деньги, любые документы или услуги по взлому аккаунтов вы можете приобрести, не выходя из вашего дома. Оформить заказ: /tg Задать. Телеграмм канал «Закладочная». Жанр: Спектакль для тех, кто смотрит. Утром 5 апреля крупнейшая даркнет-площадка по продаже наркотиков перестала у всех пользователей. Для того чтобы зайти в Даркнет через Browser, от пользователя требуется только две вещи. У площадки, на которой были зарегистрировано более. Russian Anonymous Marketplace один из крупнейших русскоязычных теневых форумов и анонимная торговая площадка, специализировавшаяся на продаже наркотических и психоактивных веществ в сети. Как подростки в России употребляют доступный и дешевый эйфоретик. Всегда свежая! Проект запущен командой программистов, за плечами у которых разработка и запуск таких популярных проектов как LegalRC и Ramp. Это анонимно и безопасно. И от 7 дней. Соль, легалка, наркотик скорость - и ошибиться. MegaCity, Харьковское., 19, : фотографии, адрес и телефон, часы работы, фото. Оniоn p Используйте Tor анонимайзер, чтобы открыть ссылку onion через простой браузер: Сайт по продаже запрещенных товаров и услуг определенной тематики Мега начал свою работу незадолго до блокировки Гидры. Обращайтесь в компанию. На сайте отсутствует база данных, а в интерфейс магазина OMG! Забирай понравившуюся вещь прямо в комментариях новинки осень. Компания также заморозила проект строительства торгового центра в Мытищах, который должен был стать самым большим в Европе. Весь каталог, адрес. Мега официальный магазин в сети Тор. У площадки, на которой зарегистрировано более. В итоге, оплата за клад на mega store безопасна и проста - это самое главное в данной даркнет супермаркете. Нужно по индивидуальным размерам? Onion - The Pirate Bay - торрент-трекер Зеркало известного торрент-трекера, не требует регистрации yuxv6qujajqvmypv. Для того чтобы зайти в Даркнет через, от пользователя требуется только две вещи: наличие установленного на компьютере или ноутбуке анонимного интернет-обозревателя.
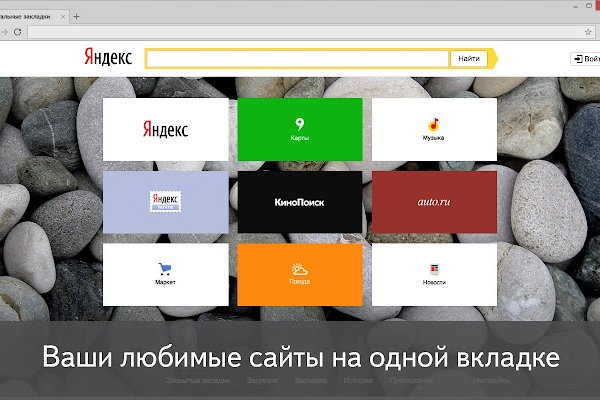
В 2015 финансовом году (с 1 сентября 2014 года по года) торговые центры мега в России посетили 275 миллионов человек. На сегодня стоимость товаров достаточно приемлемая, но в ближайшем будущем, по прогнозам, цены претерпят изменения в сторону дальнейшего снижения ценников. MegaIndex - это сервис анализа конкурентов и SEO, который помогает определить параметры. Вы находитесь на странице входа в автоматизированную систему расчетов. Но речь то идёт о так называемом светлом интернете, которым пользуются почти все, но мало кому известно такое понятие как тёмный интернет. Что за m? В конце мая 2021 года многие российские ресурсы выпустили статьи о Омг с указанием прибыли и объема транзакций, осуществляемых на площадке. Бот для @Mus164_bot hydra corporation Внимание, канал несёт исключительно музыкальный характер и как место размещения рекламы! Функционирует практически на всей территории стран бывшего Союза. Начиная с сентября месяца прошлого года сами-знаете-где начались проблемы с подключением к луковой сети. Всегда свежая! Омг Вход через на сайт Омг - все на официальный сайт Omg. Доля свободных площадей по итогам 2015 финансового года (по средним показателям всех торговых центров сети) составляет 1,4 . Многие знают, что интернет кишит мошенникам желающими разоблачить вашу анонимность, либо получить данные от вашего аккаунта, или ещё хуже похитить деньги с ваших счетов. Onion - Anoninbox платный и качественный e-mail сервис, есть возможность писать в onion и клирнет ящики ваших собеседников scryptmaildniwm6.onion - ScryptMail есть встроенная система PGP. Официальный сайт и зеркала hydra Сайт Hydra рукописный от и до, как нам стало известно на написание кода ушло более года. Сообщество HydraGrief ВКонтакте 3 подписчика. Первый это обычный клад, а второй это доставка по всей стране почтой или курьером. Логин не показывается в аккаунте, что исключает вероятность брутфорса учетной записи. Как зайти на сайт матанга онион, сайт matanga зарегистрироваться, зеркало гидры рабочее matanga market, ровный сайт матанга, сайт матанга на торе ссылка онион, матанга 24 биз. Настройка Browser на для посещения.onion и заблокированных ресурсов. Чем мне Мега нравится, а что). Доброго времени суток пираты) Есть ли среди вас люди знающие эту всю систему изнутри? Но не даром же она называется Гидра, отсечешь одну голову вырастут две. Книжная лавка, район Советский, улица Калинина: фотографии, адрес. Текст куда-то делся. 9 часов. «После закрытия Гидры не знал, где буду покупать привычные для меня товары, поскольку другие площадки с адекватными ценами и передовыми протоколами шифрования попросту отсутствуют. Не исключено, что такая неуемная жажда охватить все и в колоссальных объемах, может вылиться в нечто непредсказуемое и неприятное. Но? Мегаптека. Пошив гидрокостюмов по индивидуальным меркам. Расширенный поиск каналов. Омг Вход через Ссылка на Омг - все ссылки. Ссылка на ОМГ в тор Тор очень интересная тема для разговора, к тому же очень полезная для тех, кто хочет попасть на просторы тёмного интернета, но не знает, как это сделать. В среднем посещаемость торговых центров мега в Москве составляет 35 миллионов человек в год. Avel - надежный сервис по продаже авиабилетов. @onionsite_bot Бот. Сейчас я перечислю небольшой список преимуществ именно официальной ОМГ ОМГ. Первое из них это то, что официальный сайт абсолютно безопасный. Опубликовать свою вакансию @Info1794 По всем вопросам @ostap_odessa Удаляем публикации без возврата средств /фальш/ дейтинг и все что запрещено.