Кракен правила площадки
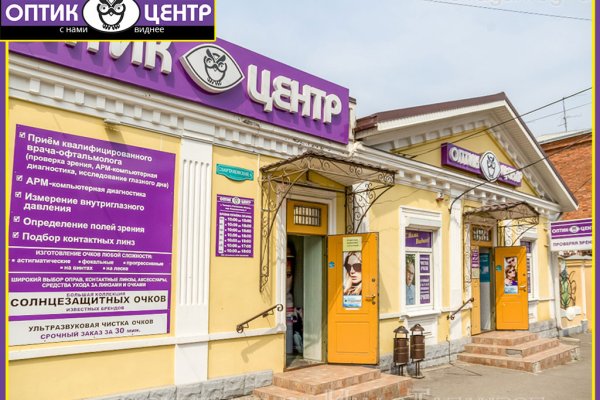
Или вы думаете, что основатель крупнейшего в даркнете портала с наркотиками Silk Road Росс Ульбрехт шифровался не так тщательно, как вы? Иногда отключается на несколько часов. Шаг 1: Установка Tor Browser Чтобы попасть на темную сторону интернета, нужно использовать специальный браузер. Onion - Konvert биткоин обменник. Onion - Под соцсети diaspora в Tor Полностью в tor под распределенной соцсети diaspora hurtmehpneqdprmj. Только английский язык. Tor поверх VPN подразумевает доверие VPN-провайдеру, но не вашему интернет-провайдеру, и является лучшим вариантом для доступа к сайтам.onion. Такая модель значительно усложняет отслеживание. После того, как Kraken рассмотрит заявку и подтвердит данные, можно пополнять счет и приступать к торгам? Это помогает группам пользователей создавать закрытые анонимные сети. Поначалу биржа предлагала к торгам скудный выбор криптовалют (BTC, ETH и LTC). Криптовалюты Bitcoin (XBT Ethereum (ETH Tether (usdt Monero (XMR Ethereum Classic (ETC). Английский язык. Теоретически вы можете попасть на вымогательство, стать информатором или «живцом» в других делах. И не вызовет сложности даже у новичка. Поэтому злоумышленник может перехватить только исходящий или только входящий трафик, но не оба потока сразу. По статье 228231 УК РФ штраф до 1 млн рублей и лишение свободы на срок до 10 лет. Поисковик Ahmia отличается тем, что он доступен как в даркнете, так и в клирнете. Mixermikevpntu2o.onion - MixerMoney bitcoin миксер.0, получите чистые монеты с бирж Китая, ЕС, США. На уровне Intermediate система запросит информацию о роде занятий пользователя, копию документа, удостоверяющего личность и подтверждение резидентства? Onion - Verified,.onion зеркало кардинг форума, стоимость регистрации. Также появляется возможность торговать фьючерсами. Отзывы о бирже Kraken На нашем портале доступны отзывы по бирже криптовалют Кракен. Форум Форумы lwplxqzvmgu43uff. Для мобильных устройств: Скачать TOR - iphone android При необходимости настраиваем мосты, с помощью внутренних функций. Org,.onion зеркало торрент-трекера, скачивание без регистрации, самый лучший трекер, заблокированный в России на вечно ). Legal обзор судебной практики, решения судов, в том числе по России, Украине, США. Существует несколько уровней верификации: Starter. Равно как и анонимность. Безопасность Безопасность yz7lpwfhhzcdyc5y.onion - rproject. Onion/ - Ahima, поисковик по даркнету. Onion - XmppSpam автоматизированная система по спаму в jabber. Onion-сайты v2 больше не будут доступны по старым адресам. Не пользуйтесь, чем попало и на что Вас выведет первая строка в поисковике, чаще всего это подставные сайты, которые заберут Ваши деньги и никаких надежд на их возврат не будет, на таких даркнет-маркетах обитают так называемые "кидалы". RiseUp RiseUp это лучший темный веб-сайт, который предлагает безопасные услуги электронной почты и возможность чата. Вывод средств возможен на незаблокированную учетную запись, либо через переоформление аккаунта со сбрасыванием условий KYC. Перейдите в «Настройки сети». Onion - Daniel Winzen хороший e-mail сервис в зоне.onion, плюс xmpp-сервер, плюс каталог онион-сайтиков. Или ваш компьютер начнёт тормозить, потому макет что кто-то станет на нём майнить. Обратите внимание, года будет выпущен новый клиент Tor. Регистрация на бирже Kraken После система перенаправит пользователя на страницу, содержащую форму регистрации. Kraken channel - даркнет рынок телеграм 10 581 subscribers Информационный канал теневого рынка кракен, вход - зеркалаонион. Что-то про аниме-картинки пок-пок-пок. Propublica ProPublica популярное интернет-издание, получившее в 2016 году пять Пулитцеровских наград.
Кракен правила площадки - Кракен наркотики россия
а сайта omgДля того чтобы всегда попадать только на официальные зеркала omg shop, вам необходимо вооружиться информацией. Прежде чем мы перейдем к списку доменов, мы хотим рассказать вам о важности знания настоящих ссылок, не секрет что существует масса различных паразитов нашего сайта. omg shop настолько огромный и всеобъятный, что только ленивый не сделал на него фейк, поэтому будьте осторожны и всегда перепроверяйте адреса по которым вы переходите, особенно при пополнении личного баланса биткоин. Ниже для вас опубликованы настоящие зеркала магазин наркотиков и нелегальных услуг:Также помимо различных фейков и мошенников, на криптомаркет запрещенки из-за своей популярности по всей России, часто пытается прикрыть роскомнадзор! Именно поэтому существую домены .onion, ведь в даркнете уже намного тяжелее властям вставлять нам палки в колеса. Попасть по такой ссылке на omg site, можно скачав Tor browser и скопировав ссылку в новоустановленный браузер - tor browser project. Поэтому в случай если какой-либо домен не доступен когда вы его пытаетесь посетить, возможно выдает ошибку или попросту белый экран, есть вероятность того что его прикрыли власти или же мы сражаемся с очередной ДДОС-атакой, в такие моменты лучше всего ипользовать tor omg и использовать onion links:Немного о omg shopomg shop - это крупнейший черный криптомаркет, где работает огромное количество продавцов и с каждым днем всё больше и больше покупателей. Всвязи со спецевичностью товара, многие клиенты переживают о своих личных данных и средствах, но команда проекта omg создала двухфакторное шифрование данных аккаунтов, которая предотвратит любую попытку взлома.
Сервисы магазина запрещенки постоянно совершенствуются и набираются опыта, наш магазин растет и товар с каждым днем пополняется новыми видами услуг и наркотиков. Наша команда тщательно следит за качеством продаваемого товара путем покупки у случайно выбранных продавцов их услуг, все проверяется и проводится анализ, все магазины с недопустимой нормой качества - удаляются из omg site!Также есть необходимость сохранить к себе в браузер настоящие ссылки гидры, чтобы иметь возможность всегда попасть в ваш любимый магазин.Если вы нуждаетесь в большей информации, то мы рекомендуем вам посетить различные статьи посвещенные часто задаваемым вопросам. Перейти к мануалам. На сайте полным-полно различных статей, вам лишь необходимо найти ту что вам нужно, на официальном сайте присутствуют много статей, вы можете получить информацию от того как зайти на гидру онион до того как совершить первую покупку на гидре.После того как вы стали чуть умнее и научилсь пользовать тор гидрой, мы хотим пожелать вам приятных покупок и хорошоге времяприпровождения, не попадайтесь в руки мошенникам и перепроверяйте все линки по которым вы переходите, всего хорошего!Теги:чёрный магазин, наркомаркет, официальные адреса омг, как зайти на онион гидру
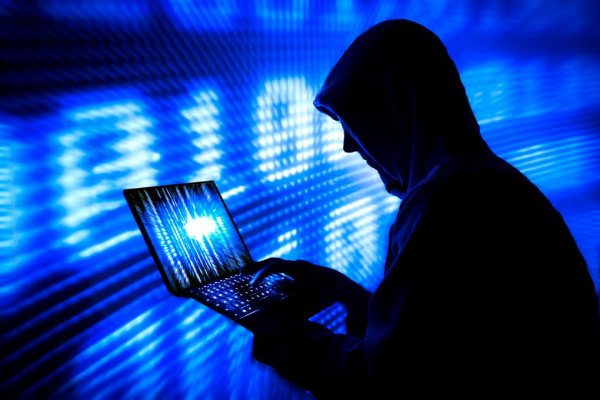
Метадоновая зависимость как проявляется После метадона появляется чувство эйфории, сопровождающееся: беспричинным весельем; разговорчивостью, болтливостью; стремлением выполнять различные действия; беззаботностью; благодушием; погружение в наркотический сон (залипание, втыкание). Реже метадоно-зависимые могут принимать внутримышечно или микстурой. Функции рецептора подтипа µ3 неизвестны. Начните с бесплатного разговора с консультантом по зависимости. Симптомы проявляются в течение 48 часов после родов. Острые отравления метадоном (дольфином) (обзор) Выводы Метадон наркотик из группы опиоидов, оказывающий обезболивающее действие. Социальная адаптация применение полученных знаний и навыков в жизни, профессиональное развитие, работа, семья. Чем дольше пациент употребляет тем выше у него толерантность, и смертельная доза должна быть больше. Обычно воздействие таких «аналогов» на организм в десятки раз токсичней, чем действие заводского препарата. В конце концов, ситуация ухудшается, вплоть до галлюцинаций и бреда. Если наблюдается потеря сознания, то нужно уложить пострадавшего на бок, аккуратно поместив голову на его согнутую руку. Общие сведения Метадон является синтетическим лекарственным препаратом группы опиоидов. Метадон действует аналогично морфину, героину и другим опиоидным наркотическим средствам. Химическая формула чистого метадона C21H27NO, а научное название Methadon. В моче Продукты обмена метадона могут находиться в моче в течение трех суток. Гистамин увеличивает проницаемость капилляров. Опасность приема таблеток в том, что их местное раздражающее влияние на слизистые оболочки желудка и кишечника становится причиной органического поражения с развитием трофической язвы. Как облегчить синдром отмены В центрах лечения и реабилитации наркозависимых ломку можно пережить в коме, в которую пациента вводят искусственно. Как бросить метадон? Лечение наркозависимостоскве Оказать помощь человеку с зависимостью от метадона сможет только врач-нарколог. Способы употребления метадона Основной способ употребления метадона среди молодежи пероральный. Характерные изменения в поведении и самочувствии: затрудненное, редкое дыхание; раздражительность и плохое настроение; недовольство собой, жизнью, окружающими; повышенное артериальное давление; частые судороги; тошнота, рвота, понос или запор. Сколько стоит метадон На черном рынке стоимость одной дозы метадона колеблется от 10 до 50 долларов. Уличные торговцы добавляют в него примеси, из-за которых он приобретает различный оттенок. На практике лишь 2 процента людей способны пережить состояние абстинентного синдрома. Они расслабляются при ходьбе. Запомните, что любой наркоман всегда находится либо под действием наркотика, либо в состоянии абстиненции. После этого человек впадает в дремотное состояние, переходящее в поверхностный сон. Каждая ампула содержит 1 куб. Прочие эффекты метадона: утрата болевой чувствительности; ощущение необычайной легкости в теле; приступы паники; галлюцинации; учащение сердцебиения; расстройства сна; нарушения памяти; расстройства работы опорно-двигательного аппарата; желание получить новую дозу наркотика. Метадон это опасный наркотик, употребление которого чревато отравлением с серьезными последствиями. Лечение наркомании Зависимость от метадона Метадоновая зависимость считается одной из самых сильных. Употребляется наркоманами, на сленге называется мед. Почему лекарство Риталин популярно в студенческой среде? Почти всегда они добываются криминальным путем. Кроме того, уже с первых высоких доз появляется физическая зависимость и без последующего употребления у пациента может начаться ломка. Привыкание происходит через несколько регулярных употреблений, а в случае передозировки нередко наступает смерть. Наркоманы стали использовать метадон чаще, потому что он действует дольше других опиатов. Наиболее опасной примесью является димедрол, которым наркоторговцы усиливают эффект метадона. Там вы можете поделиться своей историей, получить поддержку и задать вопросы психологам и психотерапевтам. Стеснительные и скромные становятся душой компании, а творческие люди начинают творить с удвоенной силой. Ощущение спокойствия сменяется тревогой. Ему назначается детоксикационная и симптоматическая терапия. Препарат, попадая в кровь, легко достигает тканей мозга, почек, печени, сердца. При необходимости может быть проведена аппаратная очистка крови от продуктов распада метадона.