Kraken магазин ссылка
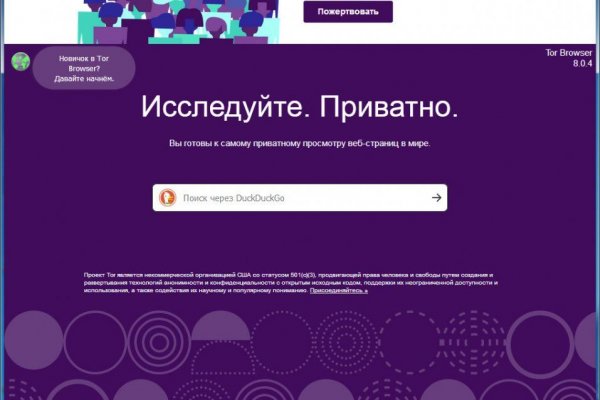
Этот магазин имеет репутацию самой безопасной и надежной площадки на даркнете, так что вы можете быть уверены в безопасности и конфиденциальности своих транзакций. Там же размещены актуальные зеркала, которые постоянно обновляются. Кракен Онион - одна из самых надежных тор-площадок на даркнете. Таким образом, вы можете уменьшить свои издержки и увеличить прибыль. Kraken Darknet - это популярный маркетплейс на даркнете, который предлагает широкий ассортимент товаров, включая наркотики, оружие, краденое программное обеспечение и многое другое. Но, как и большинство сайтов на даркнете, доступ к нему возможен только через Tor. Где кракен был раньше? Лучшего качества пока это и не встречал. Также можно использовать зеркала на Кракен Онион, которые являются альтернативными ссылками на площадку. В случае, если оригинальная ссылка на Кракен Онион была заблокирована, можно воспользоваться зеркалом, чтобы продолжить пользоваться площадкой. Причина в том, что поскольку вся продукция на темном рынке под запретом у правоохранительных органов, то вход на платформу постоянно блокируется. Вводим проверочную капчу, тут все проще простого. Этот браузер обеспечивает анонимность и безопасность в интернете, защищая вашу личную информацию. Важно помнить, что Kraken Darknet принимает только криптовалюту в качестве актуальное формы оплаты. Вы должны быть внимательными и следовать инструкциям по входу на площадку Кракен. Надоели ненаходы и ужасное отношение модераторов других маркетплейсов в Даркнете? Он используется для обеспечения анонимности и безопасности пользователей, которые хотят посещать сайты, которые не доступны в обычном Интернете. А так как по запрету двойного размещения их больше нигде нет, беру исключительно на кракен. Onion/ Эти ссылки также являются официальными зеркалами Kraken Darknet и могут использоваться для получения доступа к магазину, если первая ссылка не работает. Кроме того, на этой площадке можно заказать различные услуги, такие как хакинг, атаки DDoS и многое другое. Как зайти на Kraken Darknet? Они используют хитрые методы, чтобы обмануть людей и украсть их деньги и личные данные. С его настройкой справится даже школьник, все просто и понятно. Соверши покупку и они отпадут. И вот, можно сказать старый друг вернулся. Одной из ключевых функций, доступных на этих ссылках, является загружаемый цифровой кошелек, который использует несколько уровней протоколов безопасности, разработанных самой kraken, чтобы гарантировать, что данные пользователей остаются конфиденциальными при работе онлайн как или через мобильные устройства. А чтобы не потерять их, поместите себе в закладки. Перейти в kraken Admin К сожалению Hydra упала, мы запускаем проект kraken! Кракен Official Onion In 2019, the development team made a decision to simplify access to the Kraken Onion for all users. Это займет всего несколько лишних минут, зато вы будете уверены, что легко попадете на сайт и будете в безопасности. Именно эти символы должны стоять в конце ссылки. Чтобы купить что-то на Kraken Darknet, нужно сначала установить Tor и зайти на сайт магазина по ссылке, которую можно найти на различных даркнет-форумах. По нему видно, что и разработчики и админы вернулись с гидры. Это делает площадку одним из лучших выборов для покупки на даркнете. Мы подробно описали как зайти на зеркало Кракен без VPN. Чтобы не искать ссылку на сайт kraken darknet в интернете, вы можете воспользоваться специальными инструментами, которые помогут вам найти рабочее зеркало. Кроме того, площадка славится своими высококачественными товарами. Почему стоит выбрать Kraken Darknet? Любые другие варианты приведут человека на мошеннический сайт. Если клиент решил вывести свои средства, нет ничего сложного, это можно сделать легко и без комиссии. Если вы ищете место, где можно найти практически все, что угодно, то kraken darknet - это то, что вам нужно. Некоторые пользователи могут испытывать затруднения при поиске Kraken Darknet.
Kraken магазин ссылка - Kraken зеркало рабочее
Быстрое пополнение кошелька. Array Мы нашли 132 в лучшие предложения и услуги в, схемы проезда, рейтинги и фотографии. Есть простой, но эффективный способ определить правильную ссылку на кракен: у официального магазина домен бывает только onion и com. В 2022 году все. И предварительно, перед осуществлением сделки можно прочесть. Onion - SleepWalker, автоматическая продажа различных виртуальных товаров, обменник (сомнительный ресурс, хотя кто знает). Onion - Архив Хидденчана архив сайта hiddenchan. Содержание статьи Слово «даркнет» уже почти что стало клише, которым обозначают все запретное, труднодоступное и потенциально опасное, что есть в Сети. Ссылка на переходник Kraken вход через ТОР официальная ссылка на площадку Kraken вход через VPN. Знание ссылки на веб-ресурс, размещенный в «Дип Вебе». В опциях можно воспользоваться VIP-звонками с популярных мессенджеров, анонимно скачивать и загружать контент, менять IP и подключаться к конкретному серверу. Onion - Verified зеркало кардинг-форума в торе, регистрация. Отзывов не нашел, кто-нибудь работал с ними или знает проверенные подобные магазы? 3.На сайте Кракен запрещены такие действия как шантаж в сторону продавца. Постараюсь объяснить более обширно. А ещё его можно купить за биткоины. Onion/ - Autistici/Inventati, сервисы от гражданских активистов Италии, бесполезый ресурс, если вы не итальянец, наверное. Часто недоступен из-за огромного наплыва посетителей. Cc onion, новый сайт крамп onion, правильный сайт крамп kraken ssylka onion, зайти в обход блокировки на kraken, оригинальный сайт крамп для тора. Примените настройки, нажав на «ОК». Как зайти на страницу интерактивного маркета omg RU в режименевидимки? Еще интереснее случай случился с одним популярным основателем известной площадки сети. Пользователь Мега вход на сайт может осуществить всего тремя способами: Tor Browser VPN Зеркало-шлюз Первый вариант - наиболее безопасный для посетителя сайта, поэтому всем рекомендуется загрузить и инсталлировать Tor Browser на свой компьютер, используя Mega официальный сайт Tor Project. В СМИ и интернете часто приходится слышать такое выражение, как даркнет сайты. Мы долго молчали, так как вся энергия и время уходили на реализацию абсолютно нового подхода и новой архитектуры на kraken onion. Площадка kraken kraken БОТ Telegram Приемлемые тарифы комиссионных отчислений. Kp6yw42wb5wpsd6n.onion - Minerva зарубежная торговая площадка, обещают некое двойное шифрование ваших данных, присутствует multisig wallets, саппорт для разрешения ситуаций. Литература. Телеграмм БОТ @legalrc_24biz_bot Cайт Автопродаж legalRC в обход блокировки. Вместо 16 символов будет. Также для более высокой степени безопасности рекомендуется использовать VPN.
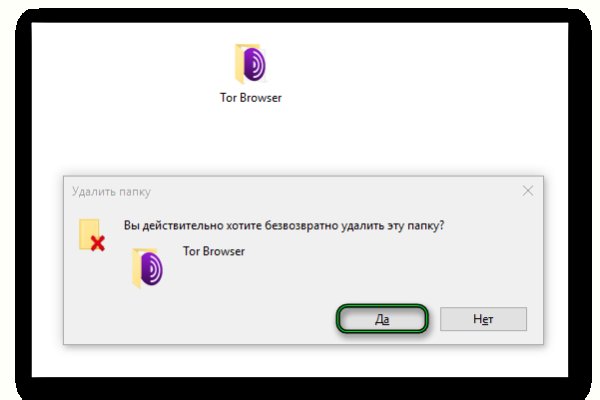
Децентрализованный и зашифрованный интернет Даркнет - это анонимная и неконтролируемая часть интернета, недоступная обычным поисковым системам типа Google. Кардинг / Хаккинг Кардинг / Хаккинг wwhclublci77vnbi. Хорошего пользования. Как зайти на сайт. При первом пополнении депозита криптовалютой, потребуется сгенерировать их адрес. Терминал для торговли деривативами состоит из меню создания заявки, панели выбора актива, графического виджета TradingView, ордербука и торговой истории. Магазин моментальных покупок Гидра обрел большую популярность в сети, в следствии чего был заблокирован по приказу РосКомНадзора. Те, кто преуспел, создают свои подпольные "корпорации" и привлекают сообщников за границей. Эта криптовалюта использовалась как основное средство расчетов на площадке. Раньше была Финской, теперь международная. Чтобы это сделать, надо скопировать адрес onion биткоин кошелька, который был выдан. Компании-провайдеры подключают к этим узлам своё оборудование, после чего предоставляют всем желающим доступ к международной компьютерной сети,.е. Вы должны создать учетную запись с реферальным кодом, чтобы активировать вознаграждение. С ростом сети появляется необходимость в крупных узлах, которые отвечают за маршрутизацию трафика. Владельцы форумов усложняют регистрацию, чтобы не допустить роботов, собирающих информацию для поисковиков и полицейских служб типа Европола. Гидра в Tor будут не доступны с Сохраните новые. Переходим на официальный сайт биржи. Вот и всё, собственно, мы рассказали вам о безопасных способах посещения магазина моментальных покупок. Вообще, я не представляю даже как взлетит курс битка. Даркнет-маркет явление относительно молодое и возможное только благодаря таким техническим особенностям как тор-браузер и bitcoin. Смените данные прокси-сервера или отключите эту функцию целиком (для этого нужно деактивировать пункт. Материал по теме Можно ли заблокировать даркнет Регуляторы пытаются ограничить доступ к сети Tor, но адресно заблокировать конкретный сайт в даркнете технически невозможно, рассуждает директор центра противодействия кибератакам Solar jsoc компании «Ростелеком-Солар» Владимир Дрюков. "Глобальная угроза киберпреступности и программ-вымогателей, которые исходят из России, а также способность криминальных лидеров безнаказанно действовать там, глубоко беспокоят Соединенные Штаты - заявила министр финансов Джанет Йеллен. Такой протокол обычный браузер просто «не поймет».